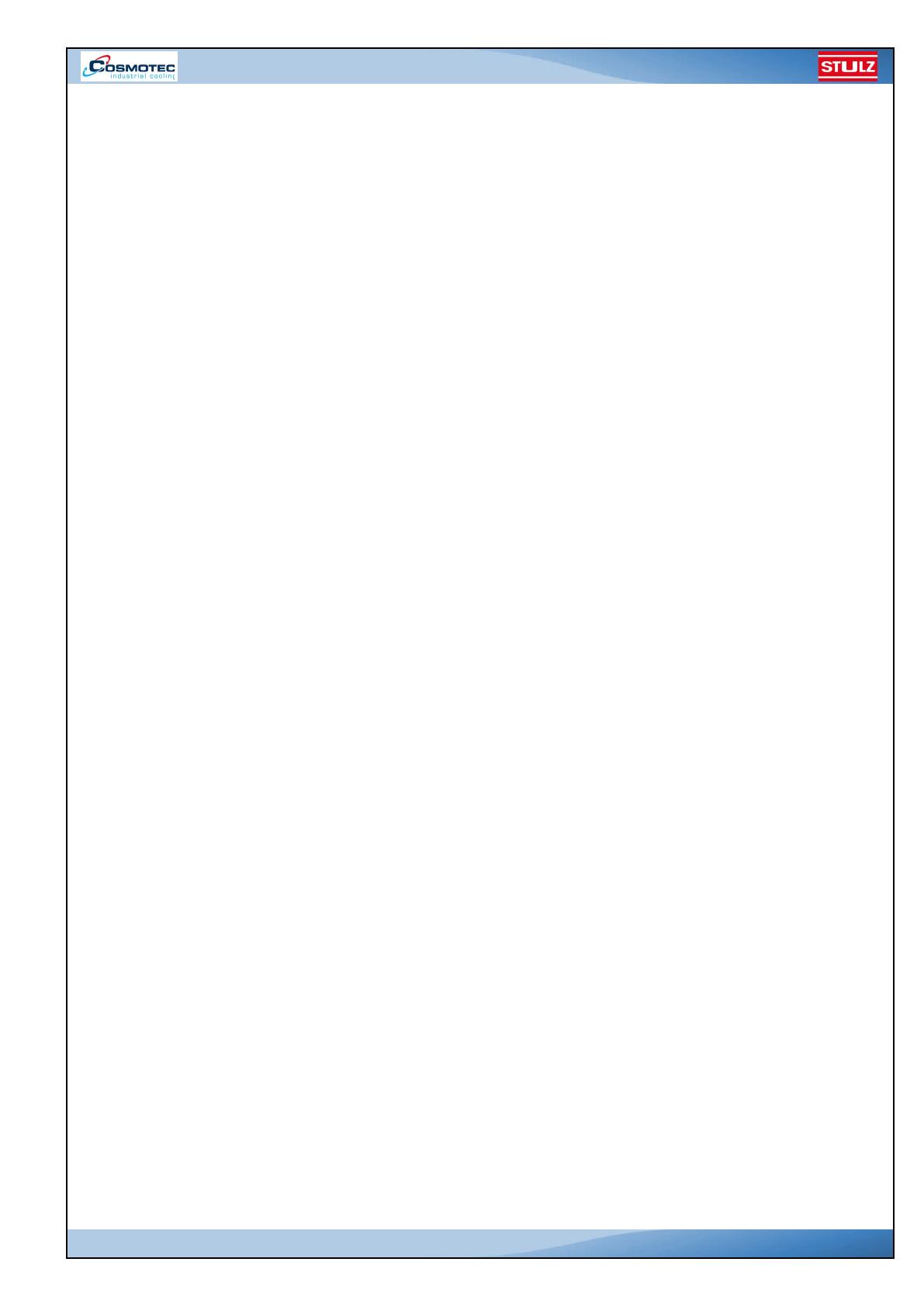
EN//0915/WLA Compact/3
Summary
1. Introduction .....................................................................................................................5
1.1. General information........................................................................................................5
1.2. Symbols used in the manual .........................................................................................5
1.3. Annexes ...........................................................................................................................5
2. Safety ............................................................................................................................... 6
2.1. Introduction .....................................................................................................................6
2.2. General rules ...................................................................................................................6
2.3. Residual risk ...................................................................................................................7
2.4. Safety data ......................................................................................................................9
2.5. Labels ........................................................................................................................... 16
2.6. Intended and unintended use ......................................................................................18
3. Coding ...........................................................................................................................19
4. Description .................................................................................................................... 20
4.1. Layout of the components, principle and mode operation. ......................................20
4.2. Refrigerant diagrams ....................................................................................................20
4.3. Components of the refrigerant circuit ........................................................................25
4.4. Safety components of the refrigerant circuit .............................................................25
4.5. Protection components of the refrigerant circuit ......................................................26
4.6. Hydraulic diagrams ......................................................................................................26
4.7. Components of the hydraulic circuit ..........................................................................27
4.8. Air circuit .......................................................................................................................27
4.9. Protection and control electric components .............................................................27
5. Technical data ............................................................................................................... 29
5.1. Application limits..........................................................................................................29
5.2. Technical data ............................................................................................................... 31
5.3. Dimensional drawings .................................................................................................38
6. Handling and storage ...................................................................................................41
6.1. Reception ......................................................................................................................41
6.2. Handling ........................................................................................................................42
7. Installation ....................................................................................................................43
7.1. Positioning ....................................................................................................................43
7.2. Hydraulic connections .................................................................................................44
7.3. Electrical connections .................................................................................................45
7.4. Commissioning preliminary operations ..................................................................... 46
8. Commissioning.............................................................................................................48
8.1. Start up .......................................................................................................................... 48
8.2. Checks to be performed after start up ........................................................................49
8.3. Deactivation ..................................................................................................................49
9. Maintenance .................................................................................................................. 50
9.1. Warnings .......................................................................................................................50
9.2. Routine maintenance ...................................................................................................51
9.3. Special maintenance ....................................................................................................53
10. Troubleshooting............................................................................................................54