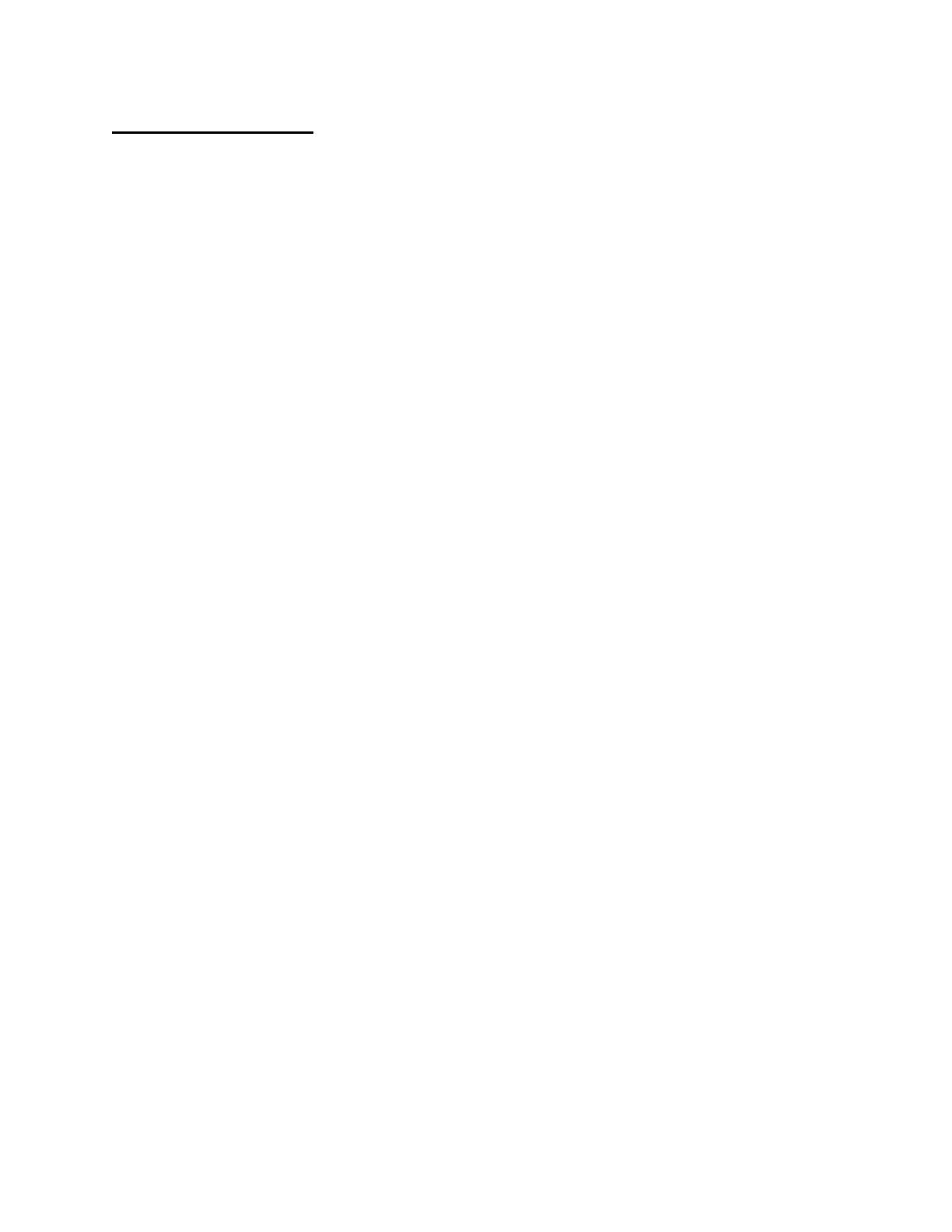
TABLE OF CONTENTS
1. PRODUCT MANUAL SAFETY INFORMATION ................................................................................ 5
2. CRITICAL INSTALLATION CONSIDERATIONS ............................................................................... 7
2.1 GENERAL ..................................................................................................................................... 7
2.2 PERSONS AUTHORIZED TO OPERATE RADIO CONTROLLED EQUIPMENT ....................... 7
2.3 SAFEY INFORMATION & RECOMMENDED TRAINING FOR OPERATORS ............................ 8
2.4 PRE-OPERATION TEST .............................................................................................................. 9
3. INTELESMART2 INSTALLATION ................................................................................................... 10
3.1 PRE-INSTALLATION .................................................................................................................. 10
3.2 RECEIVER UNIT MOUNTING LOCATION CONSIDERATIONS ............................................... 10
3.3 ANTENNA MOUNTING CONSIDERATIONS ............................................................................. 10
3.4 LINE INPUT CONSIDERATIONS ............................................................................................... 11
3.5 WIRING CONSIDERATION ........................................................................................................ 11
3.6 RECEIVER/EQUIPMENT INTERFACE CONSIDERATIONS .................................................... 12
3.7 RECEIVER UNIT ENCLOSURE MOUNTING ............................................................................ 12
3.8 RECEIVER INSTALLATION ....................................................................................................... 12
3.9 MECHANICAL DRAWINGS ........................................................................................................ 13
4. WIRING ............................................................................................................................................ 15
4.1 ALARMS AND HORNS ............................................................................................................... 15
4.2 POWER ....................................................................................................................................... 15
4.2.1 DC Power ............................................................................................................................ 15
4.2.2 AC Power ............................................................................................................................ 15
4.3 COMMONS ................................................................................................................................. 16
4.4 POWER OR HOT ROUTING ...................................................................................................... 16
4.5 MACHING STOP (MC) RELAYS ................................................................................................ 16
4.6 WIRING DIAGRAMS ................................................................................................................... 16
CONNECTING OUTPUTS TO DRIVES ..................................................................................... 18
4.7 18
4.8 ANALOG INPUT ......................................................................................................................... 18
4.9 DIGITAL INPUTS ........................................................................................................................ 18
4.10 EXPANSION MODULES ............................................................................................................ 19
5. NORMAL OPERATION .................................................................................................................... 20
5.1 INITIALIZATION .......................................................................................................................... 20
6. INTELESMART2 EXPANSION MODULE TYPES ........................................................................... 21
6.1 RELAY EXPANSION MODULE .................................................................................................. 21
7. PROGRAMMING WITH RCP .......................................................................................................... 24
7.1 ACCESS CODES ........................................................................................................................ 24
7.2 CHANGING ACCESS CODES ................................................................................................... 24
7.3 CONNECTING THE INTELESMART2 TO A COMPUTER ........................................................ 25
7.4 PROGRAMMING WITH RCP ..................................................................................................... 25
7.4.1 inTeleSmart2 Configuration Page ....................................................................................... 28
7.4.2 Programming Page ............................................................................................................. 32
7.4.3 FDP Page ............................................................................................................................ 33
7.4.4 Saving, Downloading, And Reading The Programs And Other RCP Software Functions . 34
8. RECEIVER CHANNEL CONFIGURATION SETTINGS .................................................................. 36
8.1 FCC STATEMENTS .................................................................................................................... 36
8.2 433MHz CHANNEL SET ............................................................................................................. 37
8.3 419MHz CHANNEL SET ............................................................................................................. 38