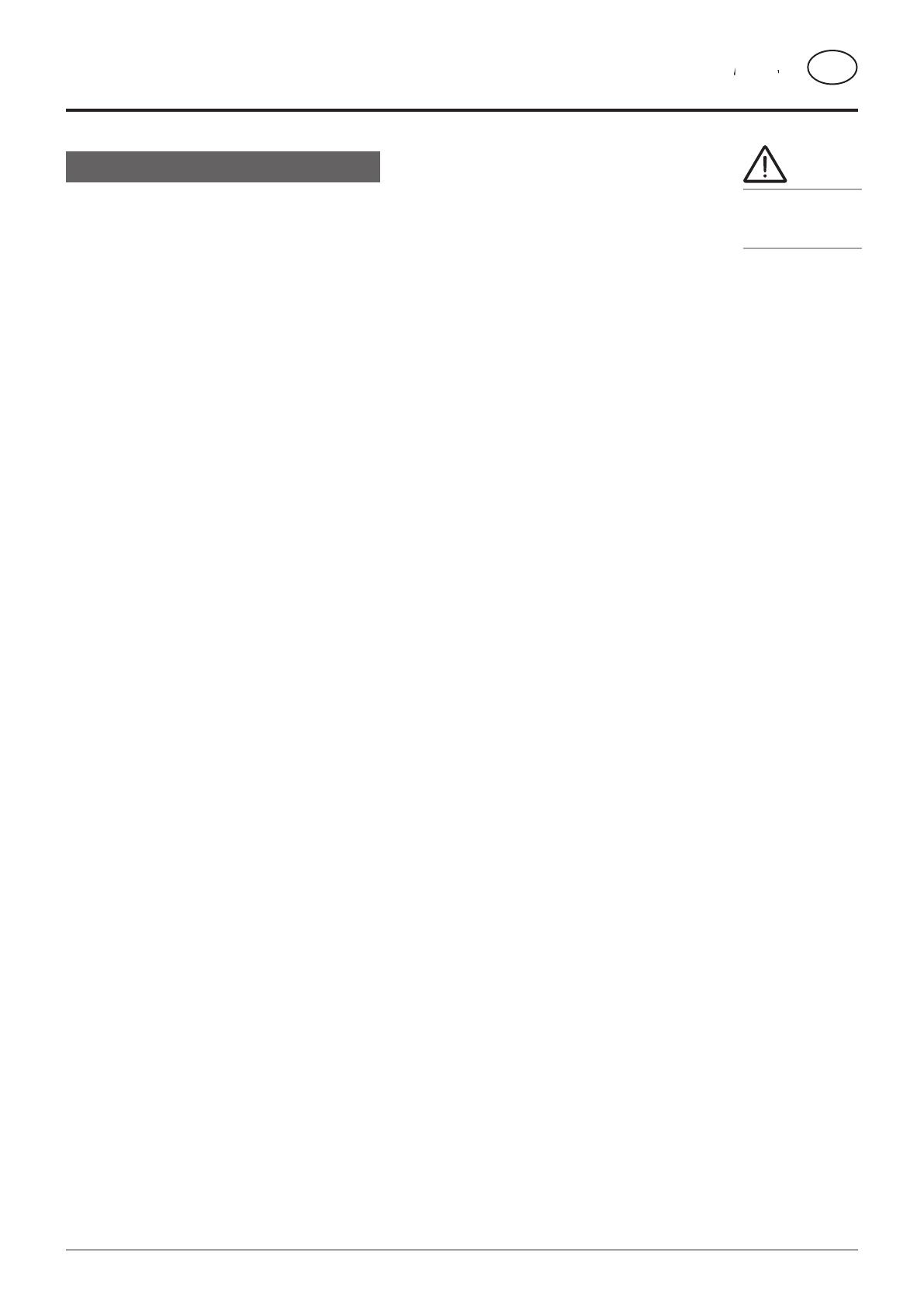
Table of contents
...............................................................
.....................................................................
...............................................................
..........................................
Travelling with implement in tow
...............................
Coupling and uncoupling the implement
...................................................
....................................................
..................................................
Checking before operation
........................................
..................................................................
.................................................................
.....................................................................
........................................................
Lifting unit (three-point linkage)
...............................
Hydraulic control on the lifting gear
Necessary hydraulic connections
............................
Necessary power connections
................................
Attach machine to lifting gear
..................................
........................................................
........................................................................
Make electrical connections
....................................
Swath rake braking system
....................................
.............................................
...........................................................
Hydraulic connection - Variant: Standard
Hydraulic connection - Variant: Power Control /
.......................................................
...........................................................
Remove / shut down machine
.................................
...........................................................
Changing from transport to working position
Conversion from working to transport position
Reducing the transport height
.................................
........................................
Changing from working position to field transport
....................................................................
............................................
Terminal performance features
................................
................................................................
........................................................
.................................................................
General safety information
......................................
.....................................................................
.................................................
Control structure - Swath rake with ISOBUS
....................................................................
.........................................................
General safety information
......................................
......................................................
.................................................
Key assignment for WTK joystick
............................
..................................................
General guidelines on working with the machine
Setting the working width
........................................
...........................................
Settings on rotor chassis
.........................................
1. Setting the transverse inclination
...........................................
Example: left rotor with tandem chassis:
3. Align indicators to one another
............................
Take care when turning on inclines!
...........................................................
General maintenance information
...........................
Cleaning of machine parts
.......................................
..................................................
.........................................................
.....................................................
...........................................................
Working on the hydraulic system
...........................
Working on the cardan shafts
.................................
.................................................
........................................................................
...............................................................
.........................................................
.................................................................
.................................................................
...................................................................
...........................................................
..............................................................
Disposal of old equipment
.......................................
Lifting points for lifting jacks
....................................
.................................................................
.................................................................
......................................................
General safety information
......................................
Coupling the air brake hoses
..................................
..........................................
...................................................
Mechanical braking force compensator
...........................................................
.........................................
..........................................................
...........................................
.........................................................
Using the rotary swath as designated
...............................................
..................................................
................................................................