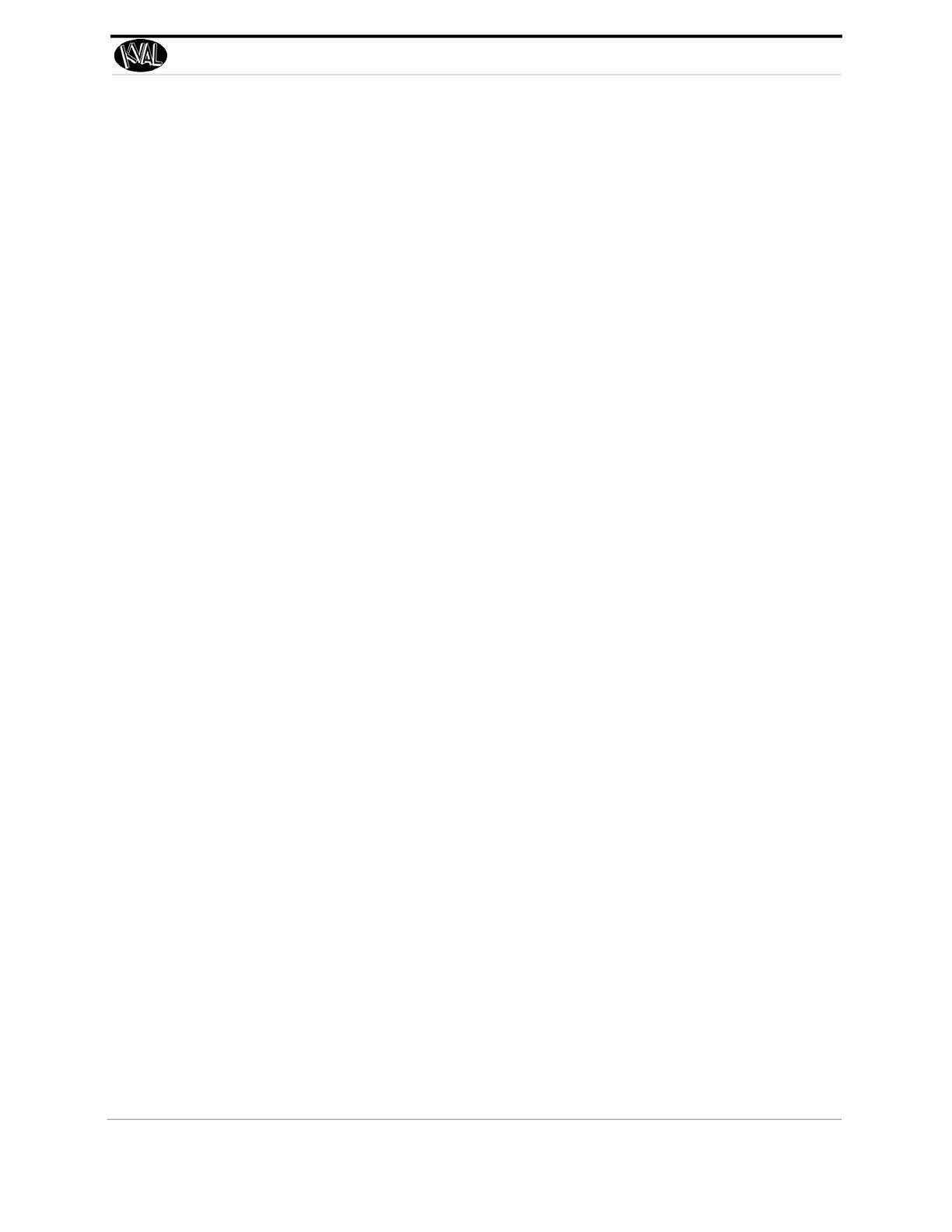
ON-3 Operation and Service Manual
Table of Contents
Chapter 1 Introduction to the ON-3
Overview of the ON-3 .............................................................. 1-2
ON-3 as a Door Feeder ........................................................................1-2
ON-3 as a Door Stacker .......................................................................1-2
Available Options..................................................................................1-2
Safety First!.............................................................................. 1-5
Safety Sheet Sign-Off Sheet.................................................................1-5
Safety Terminology of Labels................................................................1-5
Safety Guidelines..................................................................... 1-6
Training.................................................................................................1-6
Protective Gear.....................................................................................1-6
When the Machine is Powered and Running........................................1-6
Lockout Tagout Guidelines ...................................................... 1-7
Follow the P-R-O-P-E-R lockout rule of thumb.....................................1-7
Lockout Tagout Procedure....................................................... 1-8
Pre-Steps Before Lockout Tagout.........................................................1-8
Lockout Tagout Power ..........................................................................1-8
Lockout Tagout Air Supply ....................................................................1-9
Start Maintenance.................................................................................1-9
Post Maintenance Steps.......................................................................1-9
Zero-Energy to Start-Up .......................................................... 1-11
Inspect ................................................................................................1-11
Clean Up.............................................................................................1-11
Replace Guards..................................................................................1-11
Check Controls ...................................................................................1-11
Remove Locks....................................................................................1-11
Perform Visual Checks .......................................................................1-11
Close the Cage Gate ..........................................................................1-12
Getting Help from Kval............................................................. 1-13
Kval Return and Warranty Policy............................................. 1-14
Send the Item .....................................................................................1-14
Acceptance of Return .........................................................................1-14
Refund Turnaround Time....................................................................1-14
Kval Errors..........................................................................................1-14
Customer Errors .................................................................................1-15
Shipper Errors.....................................................................................1-15
Warranty Replacement Parts..............................................................1-15
Safety Sign-Off Sheet .............................................................. 1-17
A Note to the Operator .....................................................................1-17