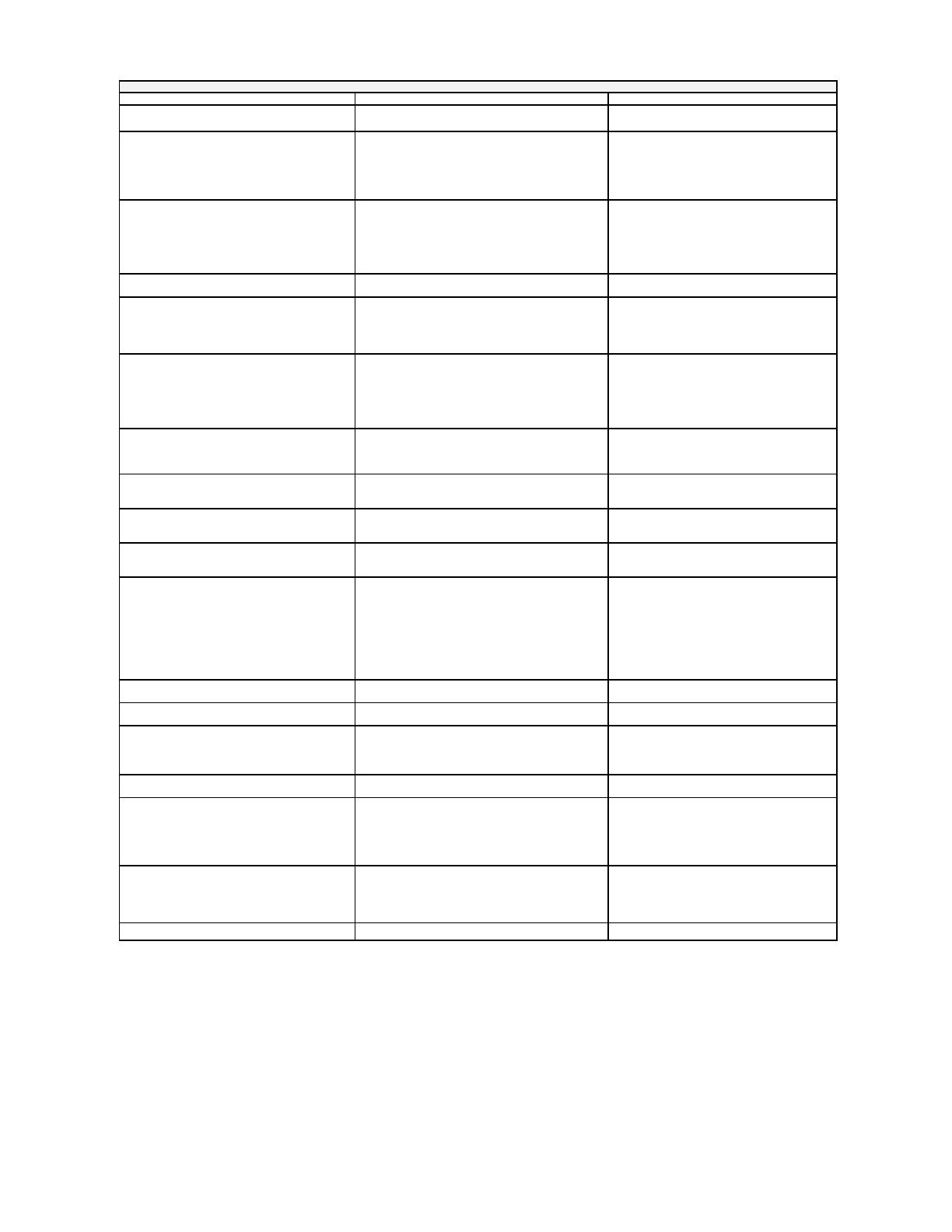
17
A representative menu is posted. Item names and setting value are subject to change.
*1 At Cool and Heat Hi speed trim, *VXC200601* with **VC960804C, **VM970804C and *MVC800804C combination trim more than 5% settings are
invalid. Trimmed up CFM makes miss matching error.
*2 Other than the above, depending on the connected indoor unit, there are restrictions on the positive side Trim setting.
If you want to change the Cool Airow Trim to positive side, be sure to conrm the Airow Trim restrictions in the latest indoor unit installation manual.
The latest manual can be obtained from the website “PartnerLink(InfoFinderPlus/Literature)”.
[PartnerLink URL]
https://partnerlinkmarketing.goodmanmfg.com/goodman/info-nder-plus
*3 The Inverter system uses lower compressor speed and lower indoor unit CFM to optimize system performance.
To obtain 100% CFM for home circulation, use full Trim setting instead of Int/Low speed.
This is recommended for applications with unusually cold return temperatures such as basements.
*4 Please refer to the page of “DEHUMIDIFICATION SELECT “ for details of this function.
SUBMENU ITEM INDICATION(Units) COMMENTS
BOOST MODE ENABLE OFF or ON BOOST MODE is ON by default. See BOOST MODE
section of this manual for more details.
BOOST TEMP Always Active or 70F to 105F in increments
If enabled, when the ambient outdoor temperature is
greater than this selected value, boost mode will be
operational.
Below this temperature the mode will not function.
There is also an option to keep boost mode
countinuously enabled.
INDOOR/OUTDOOR HEIGHT DIFFERENCE
Both Units at Same Level,
Outdoor Unit is Lower, or
Indoor Unit is Lower
If the outdoor & indoor units are within +/- 15 ft. vertical
distance, select SAME LEVEL. If the outdoor unit is
more than 15 ft. below the indoor unit, select OUTDOOR
LOWER. If the outdoor unit is more than 15 ft. above the
indoor unit, select INDOOR LOWER.
RESET FOR SYSTEM SETUP NO or YES Selecting yes will reset any system setting to their factor
defaults.
SYSTEM VERIFICATION TEST OFF or ON
System Verification Test must be run after installation.
This is approximately a 5-15 minute test. If operation
mode is set to COOL mode, the system will enter
CHARGE mode upon completion, otherwise it will stop.
PUMP DOWN OFF or ON
Enter PUMP DOWN Mode.
This procedure runs the equipment for approximately 15
minutes and allows accumulation of refrigerant at
the outdoor unit for purposes of removing & replacing th
indoor unit or outdoor unit.
ACTIVATE CHARGE MODE OFF or ON
Enter Charging Mode. This allows for a steady system
operation for a duration of approximately 1 hour to allow
for refrigerant charging of the system via the charge port.
COOLING TRIM FACTOR(HIGH)
*1, 2 -15% to +15% in 5% increments Select this airflow trim when inverter system is running
high compressor speeds during a cooling cycle.
COOLING TRIM FACTOR(MID) -15% to +15% in 5% increments,20 30, Full(Max)
*3
Select this airflow trim when inverter system is running
mid-range (intermediate) compressor speeds during a
cooling cycle.
COOLING TRIM FACTOR(LOW) -15% to +15% in 5% increments,20 30, Full(Max)
*3 Select this airflow trim when inverter system is running
low compressor speeds during a cooling cycle.
COOLING AIRFLOW PROFILE A, B, C, or D
If it is desirable to quickly ramp up the indoor airflow
select profile A.
If it is desirable to reach nominal airflow quickly, but a
slower ramp up time is required, select profile B.
If dehumidification is required immediately when cooling
mode begins select profile C.
If a slower airflow ramp up / ramp down time is required
in addition to dehumidification select profile D.
BLOWER ON DELAY-COOLING 5, 10, 20 or 30 Seconds Delay between compressor turning on and indoor blower
turning on during a cooling cycle.
BLOWER OFF DELAY-COOLING 30, 60, 90 or 120 Seconds Delay between compressor shutting off and the indoor
blower shutting off after a cooling cycle.
DEHUMIDIFICATION ENABLE*4 Standard, OFF, A, B or C Selecting "OFF" disables dehumidification selecting.
"Standard", "A", "B" or "C" enables dehumidification.
RESET COOLING SETTINGS NO or YES Selecting yes will reset any cooling setting to their
factory defaults.
RPS RANGE FOR COOLING **.* to **.* RPS,…(Total 5 Ranges)
When determining the appropriate compressor speed for
cooling, select the range that contains the desired value.
The Selected RPS for Cooling menu is where you will
select your desired value within this selected range.
SELECTED RPS FOR COOLING **.* RPS
This value will be a number inside the RPS Range for
Cooling.
If you'd like to select a RPS from a different range, you
must change the RPS Range for Cooling setting first,
then restart the device setting page
RESET FAULT HISTORY NO or YES Selecting yes will clear the fault histories of device.
AIR CONDITIONER(AC) / DEVICE SETTING