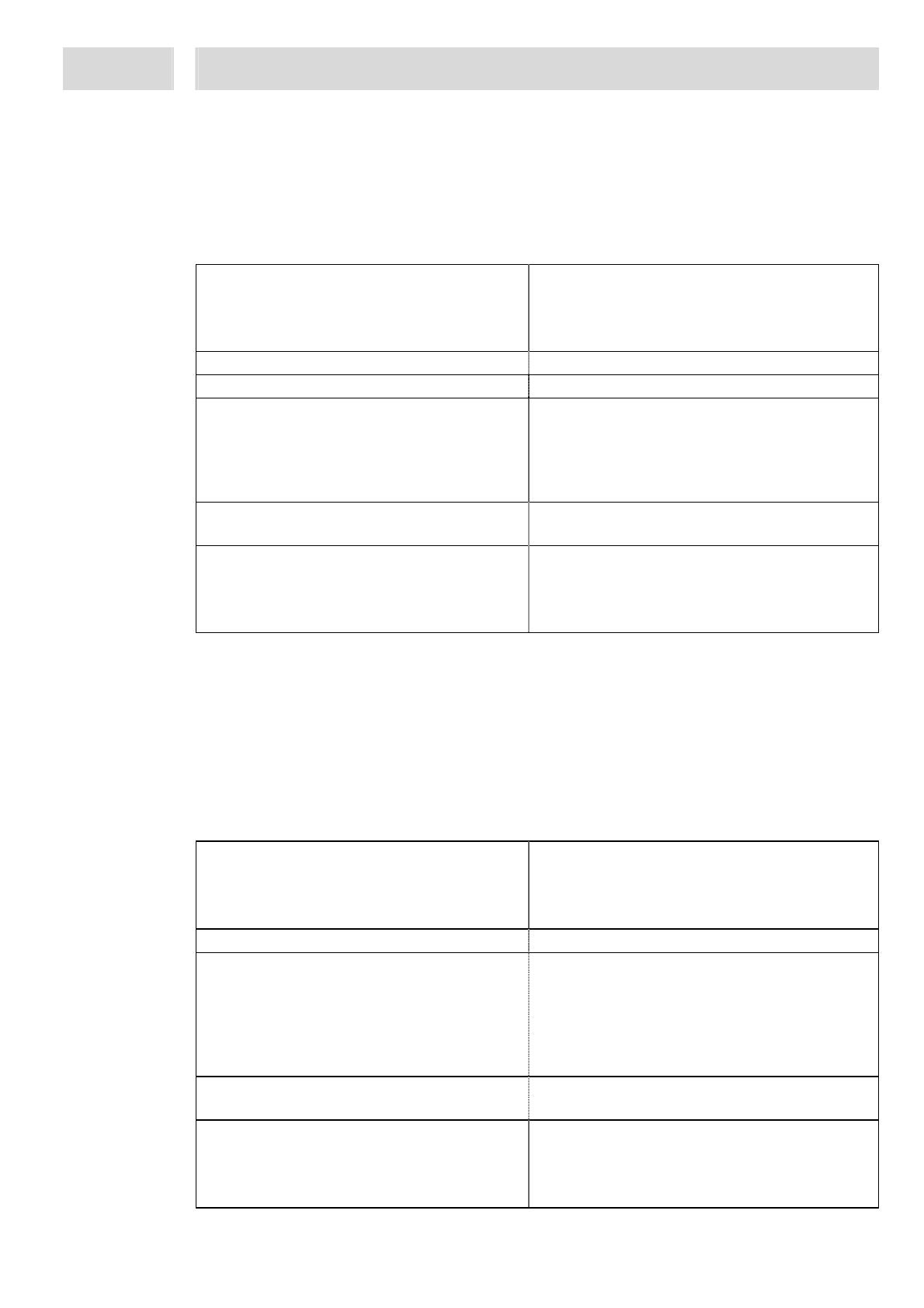
65
2 Description
2.7.1 Integrated pneumatic solenoid valve module: 1 dispense channel
All components are connected to the connectors of dispense channel A and actuated in the
dispense channel A system menu.
The Flow Monitor is connected to connection XS 3, the product reservoir is connected to
connection XS 2.
Connectable components LOCTITE designations
1 dispense valve with double acting actuator
(for dispense valves with single acting
actuator, close port 0 with blind plug).
– Diaphragm Valve 97135 or 97136
– Stationary Applicator Valve 97113 or 97114
– Cyanoacrylate Dispense Valve 97134 or 98013
– Light Cure Dispense Valve 98009
1 double acting advancing slide – Advance Slide 97118 or 97119
1 electric rotor unit – Rotospray 97115 or 97144
1 Dispense flow monitor
– Pressure based On-line Pre-amplifier
97211and dispense valve with pressure sensor,
or
– Calorimetric Pre-amplifier 97512 with
dispense valve 97830
1 DC motor
– Eccentric Rotor Pumps 97660, 97663, 97665
or 97669
1 Product reservoir – 0.5 l product reservoir 97125 or 97106
– 2 l product reservoir 97108
– Supply Pump 97809
– 2 l Bag Dispenser 97124
2.7.2 Integrated pneumatic solenoid valve module: 2 dispense
channels without advancing slide
All components are connected to the connectors of dispense channel A and actuated in the
dispense channel A system menu. In this configuration, the advancing slide connectors are used
for the 2nd dispense valve. Therefore, no advancing slide can be connected. The second dispense
valve with its flow monitor is actuated in the dispense channel B system menu. Flow monitors are
connected to connection XS 3, the product reservoir is connected to connection XS 2.
Connectable components LOCTITE designations
2 dispense valves with double acting actuator
(for dispense valves with single acting
actuator, close port 0 with blind plug).
– Diaphragm Valve 97135 or 97136
– Stationary Applicator Valve 97113 or 97114
– Cyanoacrylate Dispense Valve 97134 or 98013
– Light Cure Dispense Valve 98009
1 electric rotor unit – Rotospray 97115 or 97144
2 Flow monitors
– Pressure based On-line Pre-amplifier
97211and dispense valve with pressure sensor
for each dispense channel (splitter cable 97529
required) , or
– Calorimetric Pre-amplifier 97512 with
dispense valve 97830
1 DC motor
– Eccentric Rotor Pumps 97660, 97663, 97665
or 97669
1 Product reservoir – 0.5 l product reservoir 97125 or 97106
– 2 l product reservoir 97108
– Supply Pump 97809
– 2 l Bag Dispenser 97124