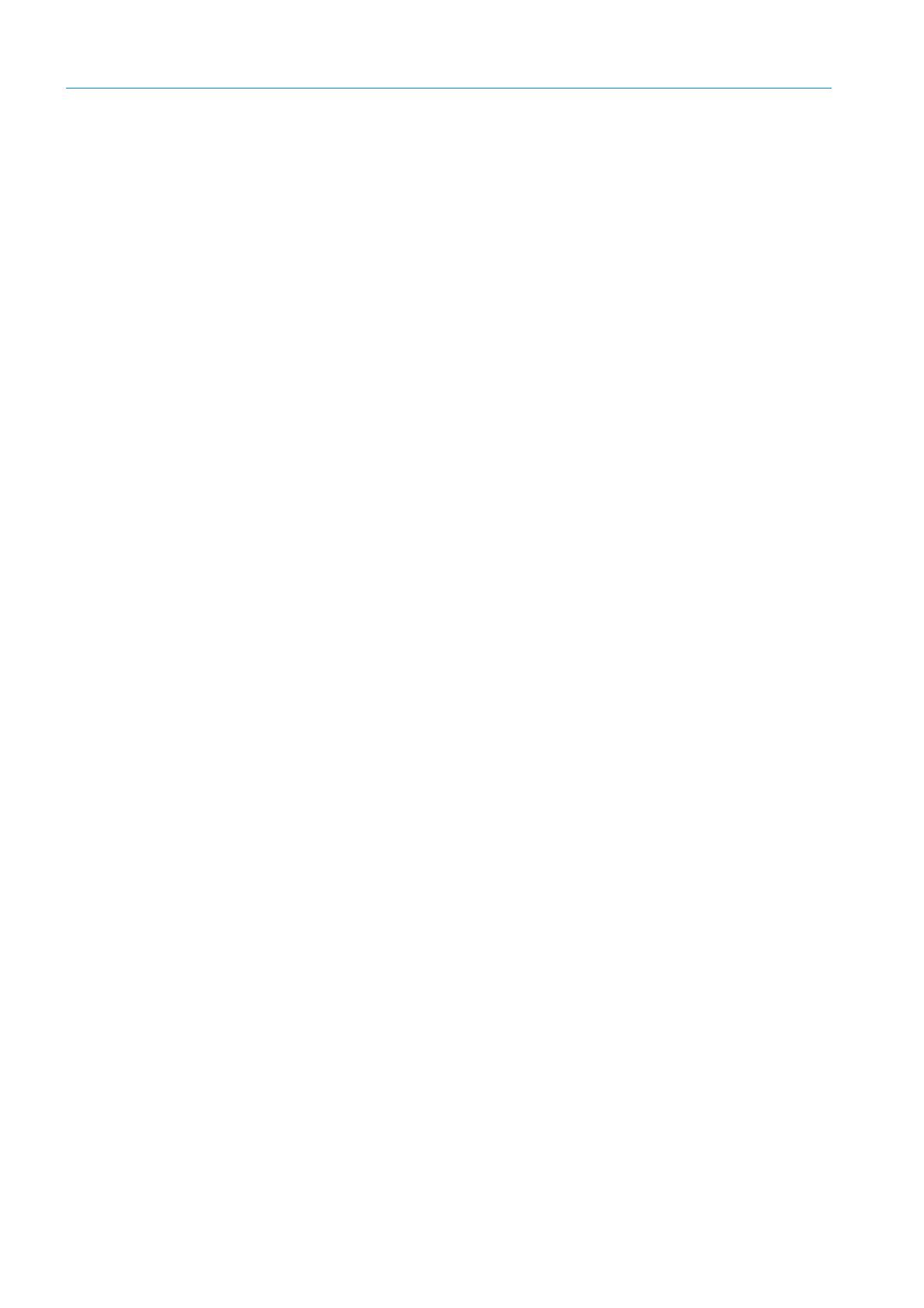
CONTENTS
4
8011703/XF49/V3-1/2019-09 | SICKO P E R A T I N G I N S T R U C T I O N S | VICOTEC320
Subject to change without notice
5.7 Electrical installation .................................................................................... 24
5.7.1 Electrical protection ..................................................................... 24
5.7.2 Connecting the sensors to the connection unit .......................... 25
5.7.3 Connection unit cabling ............................................................... 26
6 Commissioning ........................................................................................ 32
6.1 Necessary technical knowledge for commissioning ................................... 32
6.2 Commissioning checklist.............................................................................. 32
6.2.1 Device data................................................................................... 32
6.2.2 Tunnel data................................................................................... 32
6.3 Alignment ...................................................................................................... 33
6.4 Spectral analysis........................................................................................... 35
6.5 Visibility and smoke detection ..................................................................... 35
6.6 Signal outputs............................................................................................... 36
6.7 Saving data ................................................................................................... 36
7 Operation ..................................................................................................37
7.1 Operating the VICOTEC320 .......................................................................... 37
8 Using the VICOTEC320............................................................................38
8.1 Software SOPAS ET....................................................................................... 38
8.1.1 Functions (overview) .................................................................... 38
8.1.2 Installing the SOPAS ET software ................................................ 38
8.2 Using SOPAS ET ............................................................................................ 38
8.2.1 Creating a connection .................................................................. 38
8.2.2 Reading out the VICOTEC320 and operating manually.............. 44
8.2.2.1 Exporting messages ................................................. 47
8.2.3 Saving the current parameter set................................................ 48
9 Maintenance............................................................................................. 49
9.1 Cleaning ........................................................................................................ 49
9.1.1 Cleaning sensors .......................................................................... 49
9.1.2 Tunnel cleaning ............................................................................ 49
9.2 Maintenance work ........................................................................................ 50
9.2.1 Persons authorized to carry out maintenance............................ 50
9.2.2 Replacing the activated charcoal ................................................ 50
9.2.3 Replacing the drying agent cartridge .......................................... 51
9.2.4 Replacing the sender lamp and LED ........................................... 52
9.2.5 Replacing the CO sensor.............................................................. 56
9.2.6 Span Test...................................................................................... 57
9.2.6.1 Determination and setting of the span factors ....... 59
10 Troubleshooting .......................................................................................60
10.1 Error messages............................................................................................. 60