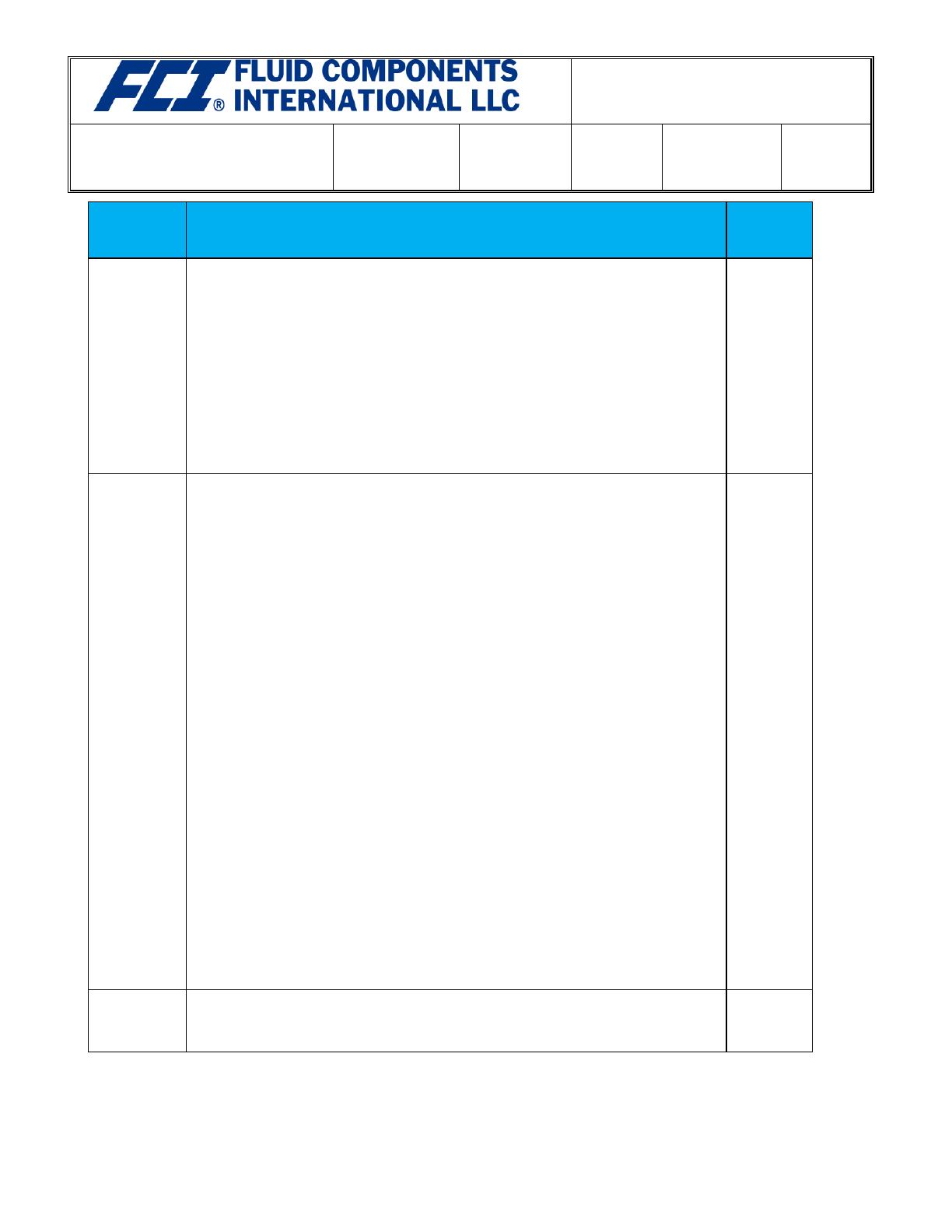
Company Headquarters: 1755 La Costa Meadows Drive, San Marcos, CA
DOCUMENT NUMBER
07QA070003
SUBJECT
Quality Manual
CAGE CODE
64818 DATE
6/15/2023
SECTION
General
PAGE
vii of xvii
REVISION
U
REVISION DESCRIPTION DATE
R
Corrected the Table of Contents.
SCOPE OF WORK exception for FCI Aerospace from the same as commercial work but
without Conditioners.
Removed Appendix A (Form 05QA000220)
Removed Appendix C (Form 05QA000162)
Appendix D has been moved and renamed as Appendix A.
Removed Appendix E (Form 05QA000219)
Removed Appendix F(Form 05QA000201)
Section 1, 4.2.a) PoI Moved from Appendix F to Form 05QA000201.
Section 1, 5.2 Quality Policy Moved from Appendix E to form 05QA000219
Section 2, 4.2.a) PoI Moved from Appendix F to Form 05QA000201.
Section 2, 5.2 Quality Policy Moved from Appendix E to form 05QA000219
Section 3, 1.1 “Appendix D to this manual …” is “Appendix A to this manual…”
Section 3, 1.1 “see Appendix A, Company Organization Chart” is “see 05QA0000220, FCI
10/5/2021
T
Section General, Signature page Director of Administration & Quality, Ron Ogle replaced
with Director, Legal & Administration, Melissa Alexander, Added Eric Wible, Director of
Industrial Operations.
Section General, page iii added for Safety
Section General, Appendix A President removed the Directory of Administration & Quality
from the implementation of the Quality Management System.
Section General, Appendix A General Manager FCI Aerospace and FCI Nuclear corrected
Responsible Manager to Accountable Manager.
Section General, Appendix A, Added Executive Director, Industrial Operations (From
Director of Engineering…)
Section General, Appendix A, Director of Administration changed to Director Legal &
Administration with responsibilities changed removing Quality and Maintenance.
Section General, Appendix A, Quality Manager removed the reporting to the Director of
Administration.
Section General, Appendix A, Removed the Director of Engineering…to Executive
Director…
Section General, Appendix A, Removed Director of Manufacturing leaving manufacturing
Manager
Section General, Appendix A, Added Document Management.
Section General, Appendix B, Added Column for ISO9001.
Section 1, Para 6.2.1. b) Typo Fixed
Section 1, Note: Notification ISO IEC 80079-34 Removed Director of Quality and QA
Manager to Quality Assurance Management. And revised retention from “for ten years” to
“for a minimum of ten years. See 05QA000182 Quality Record Retention.”
Section 1, Para 9.2.2. B Fixed Typo
Section 2, Para 1.2.2 Added for ASY15A in the Tech Center
Section 3, Para 7.1.1 Removed “For ISO 17025 accredited Calibration Service & Testing
providers that have a third party accreditation approval from sources recognized by the
Nuclear Regulatory Commission, a survey may be waived (04QA704044)
7.1.1 Added “ILAC Process… “
7/22/2022
U
Scope of Work: Added “For FCI Aerospace in the Tech Center the Scope is: The
manufacturing of sensors for Aviation, Space & Defense applications.” 6/15/2023