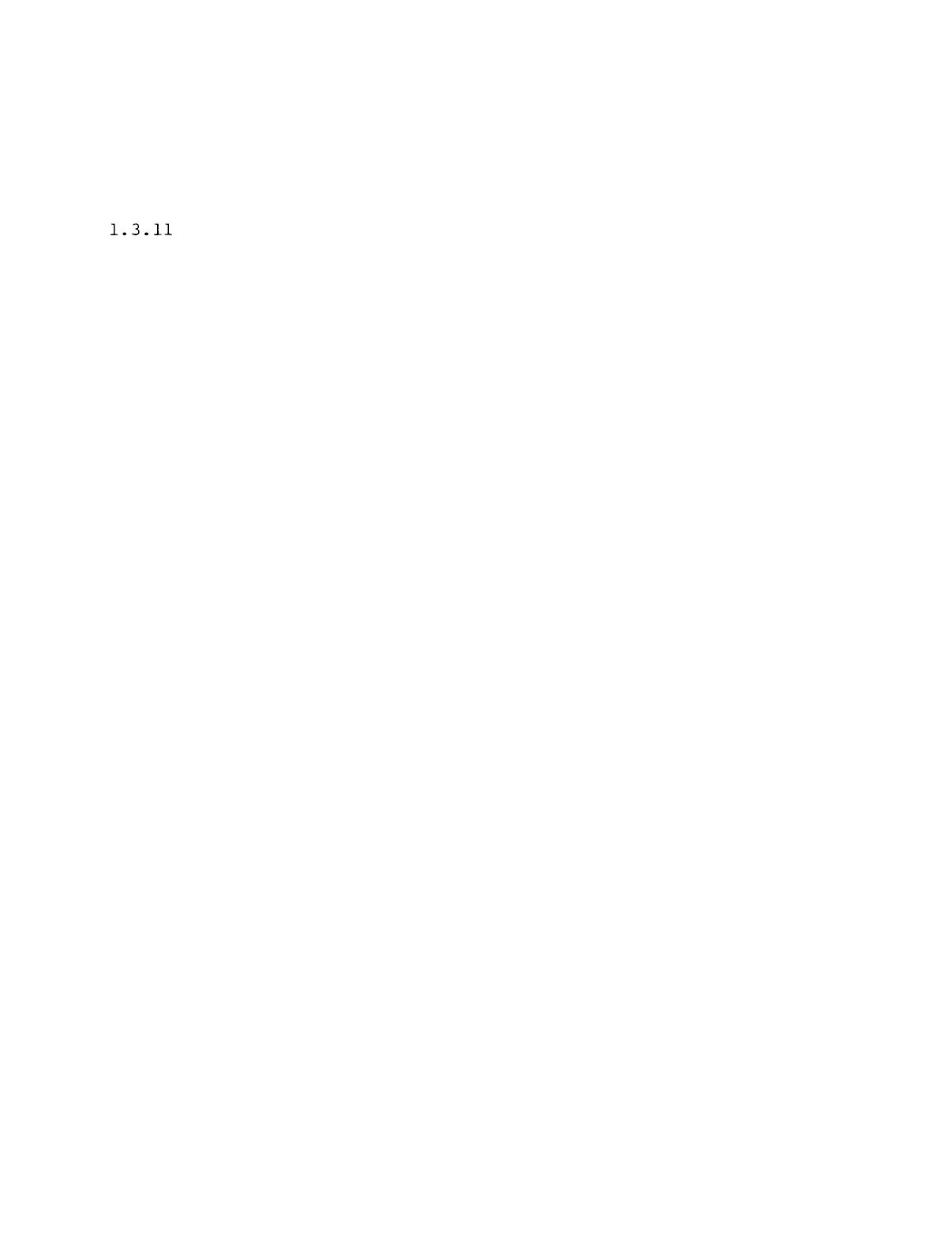
1.3.9 The orientation of the spindle is not correct . . . . . .
48
1.3.10 The acceleration/deceleration time increases . . . . . . .
53
1.3.11 The speed detection signal, up to speed signal,
or zero speed signal is not issued . . . . . . . . . . . . . . . . .
54
1.3.12 The tapping operation cannot be correctly performed. 55
1.3.13 The threading operation cannot be correctly
performed
. . . . . . . . . . . . . . . ..I...........
. . . . . . . . . . . . .
57
2. Checking and replacing parts
............................
58
2.1
Replacing fuses
......................................
59
2.2
Replacing thermal protectors
.........................
59
2.3
Replacing amplifier cooling fan
......................
59
2.4
Replacing printed circuit board
......................
61
2.4.1
Replacing SF-PW module
.............................
61
2.4.2
Replacing SF-OR or SF-10 card
......................
62
2.4.3
Replacing SF-TL card
...............................
63
2.4.4
Replacing SF-CA card
...............................
64
2.5 Checking transistor module (This method is the same
both in the power side and regeneration side)
........
65
2.6
Checking diode stack
.................................
68
2.7
Replacing transistor module and diode stack
..........
70
2.8
Replacing motor cooling
..............................
71
2.9
Adjusting and replacing motor built-in encoder
.......
74
2.9.1
Adjusting printed circuit board
....................
74
2.9.2
Replacing encoder and printed circuit board
........
77
3. Spindle orientation control circuit . . . . . . . . . . . . . . . . . . . . .
79
3.1
Structure . . . . . . . . . . . . . . . . . . . . . . . . . . . . . . . . . . . . . . . . . . . .
80
3.1.1 Spindle orientation using magnesensor (1 point) . . . . 80
3.1.2
Spindle orientation using encoder . . . . . . . . . . . . . . . . . .
82
(4096 points,
with index function)
3.2
Control circuit and parameter setting . . . . . . . . . . . . . . . .
84
3.2.1 Where the speed selection signal function is
provided (SF-OR card)
. . . . . . . . . . . . . . . . . . . . . . . . . . . . . .
84
3.2.2 Where the equipment is linkedwith the NC through
the bus . . . . . . . . . . . . . . . . . . . . . . . . . . . . . . . . . . . . . . . . . . . .
89