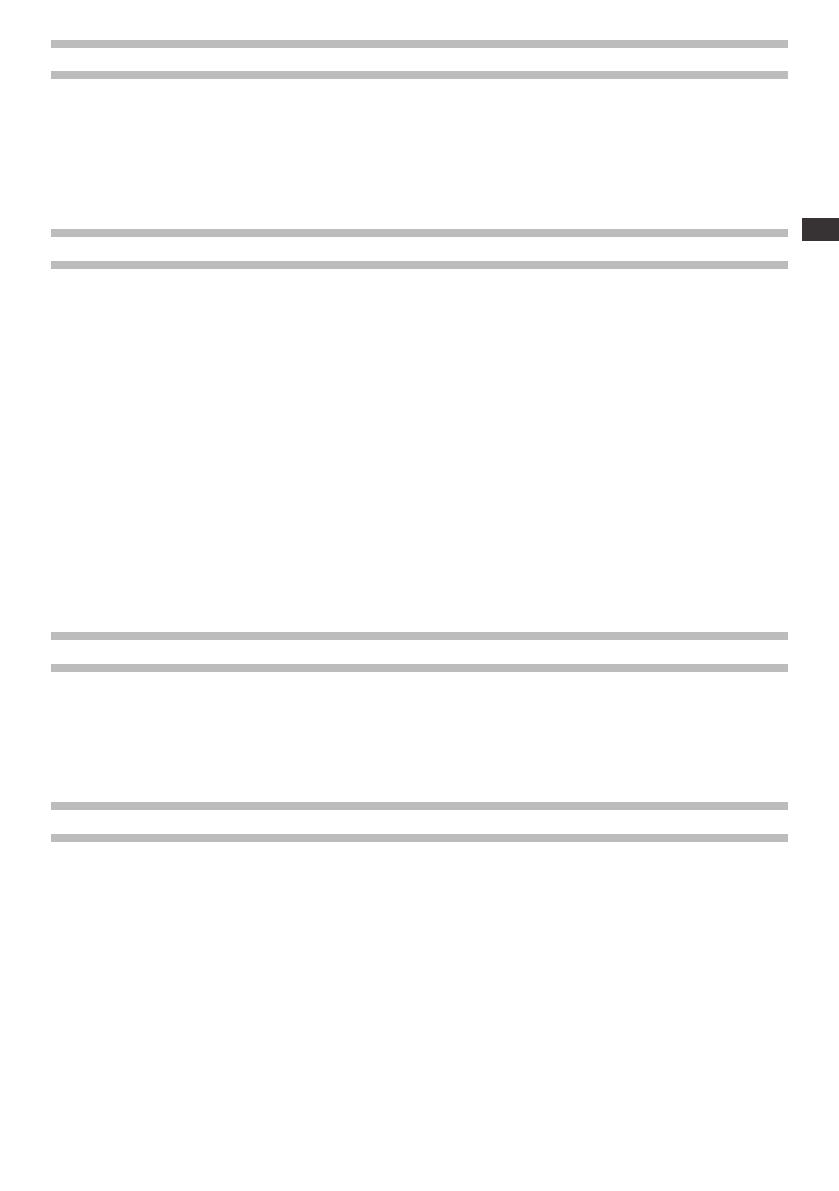
23
INSTALLATION FITTING THE ACCESSORIES
• Connect the quick t connector (27) on the hose (26) to the water outlet connector (5) and secure the
ring nut tightly by hand. Step H in Fig. 7.
• Screw the connector (25) on the high pressure hose onto the thread of the cleaner gun (17) and tighten
it using two 17/22 mm spanners (not supplied). Step G in Fig. 7.
• Insert the lter (29) and the seal (30) in the cup (28); screw the cup(28) onto the connector (4). StepI in
Fig. 8.
PRELIMINARY OPERATIONS
• Put the power cable support (7) on the sheet metal plate of the handle (3) and x it with the self-tapping
screw (10). Step A in Fig. 2.
• Insert the handle (3) in the steel pipes projecting from the machine and x it using the kit supplied: tighten
the threaded handwheels (11) on the nuts retained by their housings on the handle. Step B in Fig. 2.
• Use the handles (3) to move the high pressure cleaner to the area where it is to be used.
• Unwind the high pressure hose completely (26).
• Using a quick coupling (GARDENA® type or equivalent), secure a supply hose (35) with an internal diameter
of 13 mm/0.51 in to the water inlet lter cup (28). Step I in Fig. 8.
• Connect the water supply hose to a tap.
• Open the water tap (if connecting to the mains wa ter supply, you must use a backow hydraulic device
(36): please refer to the relative instruction manual), making sure that there is no dripping (or place the
suction pipe in a draft tank).
• Check the master switch (1) is set at “0” and connect the plug. Step D in Fig. 5.
• Move the master switch (1) to position “I”.
• Press the cleaner gun lever (23) and wait for an even stream of water to be produced.
• Move the master switch (1) to “0” and connect the lance pipe (19) to the cleaner gun (18), securing it
rmly. Step F in Fig. 7.
STANDARD OPERATION WITH COLD WATER AT HIGH PRESSURE
• Make sure that the hot water switch (31) is in position “0”.
• Turn the high pressure cleaner on again by turning the master switch (1) to “I”.
• Press the cleaner gun lever (23) and check the nozzle spray is even without dripping.
• The high pressure cleaner is set to operate at the maximum permissible pressure, if lower pressure values
are to be used, contact a Specialized Technician, who will reset the pressure control/adjustment valve .
STANDARD OPERATION WITH HOT WATER AT HIGH PRESSURE
• Make sure that the hot water switch (31) is in position “0”.
• Unscrew the cap (8) and ll the tank with automotive gas oil, making sure the fuel does not spill over. We
recommend using a funnel reserved exclusively for this purpose (maximum tank capacity 4l/1,06USgal);
replace and tighten the cap.
• Turn the high pressure cleaner on again by moving the master switch (1) to “I”
• Premere l’interruttore acqua calda (31) portandolo in posizione “I”.
• Press the cleaner gun lever (23) and check the nozzle spray is even without dripping.
• The high pressure cleaner is set to operate at the maximum permissible pressure, if lower pressure values
are to be used, contact a Specialized Technician, who will reset the pressure control/adjustment valve.
• When the fuel is low, the burner will stop working.
• The burner starts working after about three seconds from the opening of the spray gun and stops when
the spray gun is closed or when the maximum permissible temperature has been reached.
• If you want to switch from hot water operation to cold water operation, press the hot water switch (31)
to position “0”.
EN