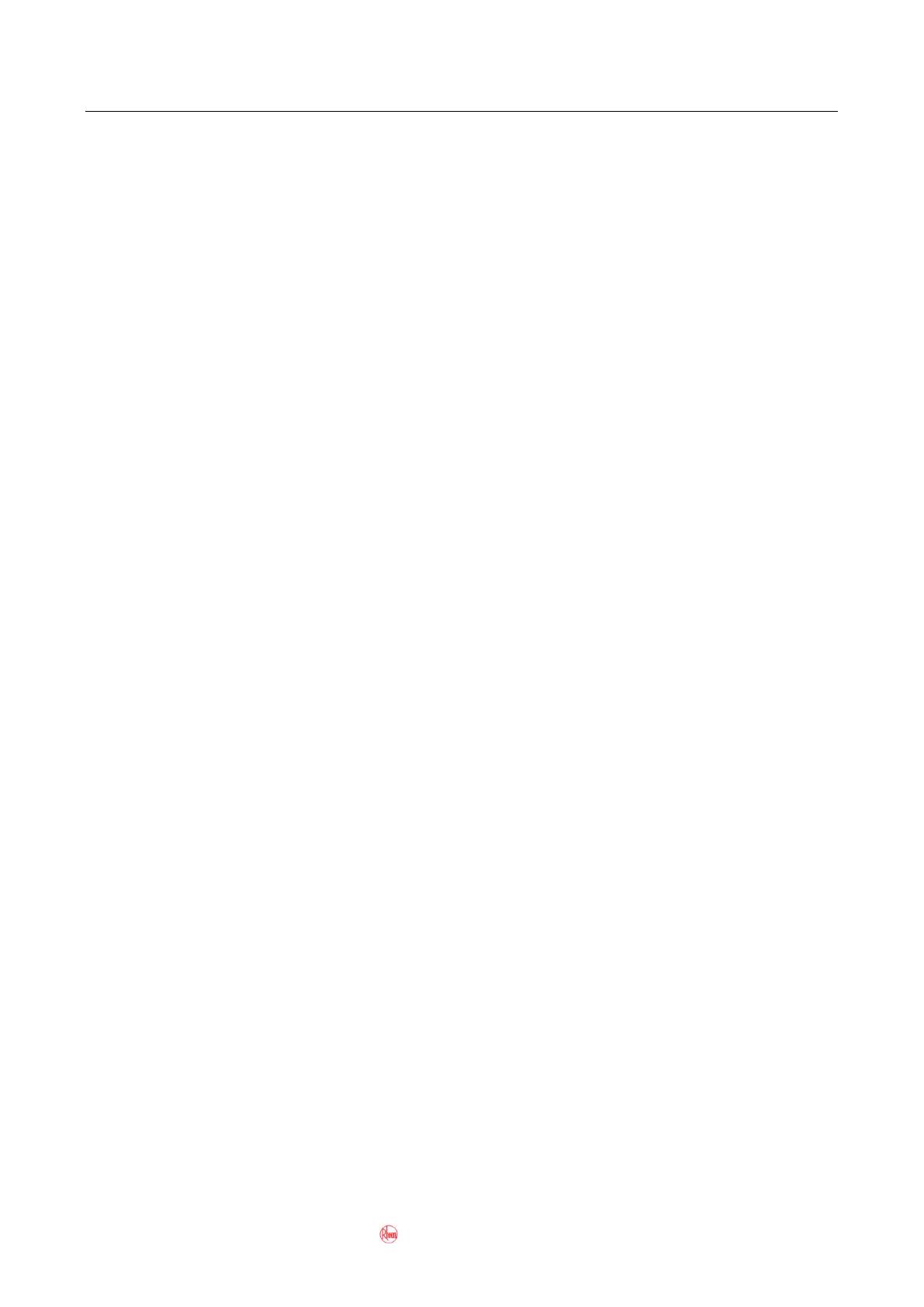
TM036 Vermont Gas Fireplace & Gas Log Fire Service Instructions REV: A
D.O.I: 17/01/2008
This document is stored and maintained electronically by Service. All printed copies not bearing this statement in RED are deemed “uncontrolled”
Contents
Safety Warning .................................................................................................................... 3
Introduction .......................................................................................................................... 3
Model Identification .............................................................................................................. 3
Specifications ....................................................................................................................... 4
Fluing ................................................................................................................................... 5
Wiring Diagrams .................................................................................................................. 6
Components and Their Function .......................................................................................... 7
Gas Valve Features ............................................................................................................. 8
Operation ............................................................................................................................. 9
Lighting Instructions ........................................................................................................... 12
Remote Controller Operation ............................................................................................. 12
Recognition Signal ......................................................................................................... 12
On (Manual) Mode ......................................................................................................... 13
Auto Mode ...................................................................................................................... 13
Off Mode ........................................................................................................................ 14
Other Functions .............................................................................................................. 14
Preventative Maintenance ................................................................................................. 15
Common Faults ................................................................................................................. 16
Fault Finding ...................................................................................................................... 17
Checking Inlet Gas Pressure .......................................................................................... 17
Checking Burner Gas Pressure ...................................................................................... 17
Adjusting the Pilot Flame ................................................................................................ 18
Adjusting the Ignition Plug Gap ...................................................................................... 18
Gas Valve Safety Shutdown Test ................................................................................... 18
Fault Indication ............................................................................................................... 18
Error Code 3 ............................................................................................................... 19
Error Code 8 ............................................................................................................... 19
Fault Diagnosis Sequence (General Fault Finding Chart) .............................................. 20
Fault Finding Chart 1 ...................................................................................................... 21
Fault Finding Chart 2 ...................................................................................................... 22
Fault Finding Chart 2.1 & 2.2 ......................................................................................... 23
Fault Finding Chart 3 ...................................................................................................... 24
Fault Finding Chart 4 ...................................................................................................... 26
Fault Finding Chart 5 ...................................................................................................... 27
Fault Finding Chart 5.1 & 5.2 ......................................................................................... 28
Fault Finding Chart 6 ...................................................................................................... 29
Fault Finding Chart 6.1 & 6.2 ......................................................................................... 32
Fault Finding Chart 6.3 ................................................................................................... 33
Electrical Insulation Testing ............................................................................................ 33
Fault Finding Chart 7 ...................................................................................................... 34
Fault Finding Chart 8 ...................................................................................................... 35
Component Replacement Procedures – LHEC30 ............................................................. 35
Component Replacement Procedures – RFSDV34 ........................................................... 41
Exploded View 1 – LHEC30 ............................................................................................... 47
Exploded View 2 – RFSDV34 ............................................................................................ 49
Gas Type Conversions ...................................................................................................... 51
Warranty ............................................................................................................................ 52
Document Revision History ................................................................................................ 53