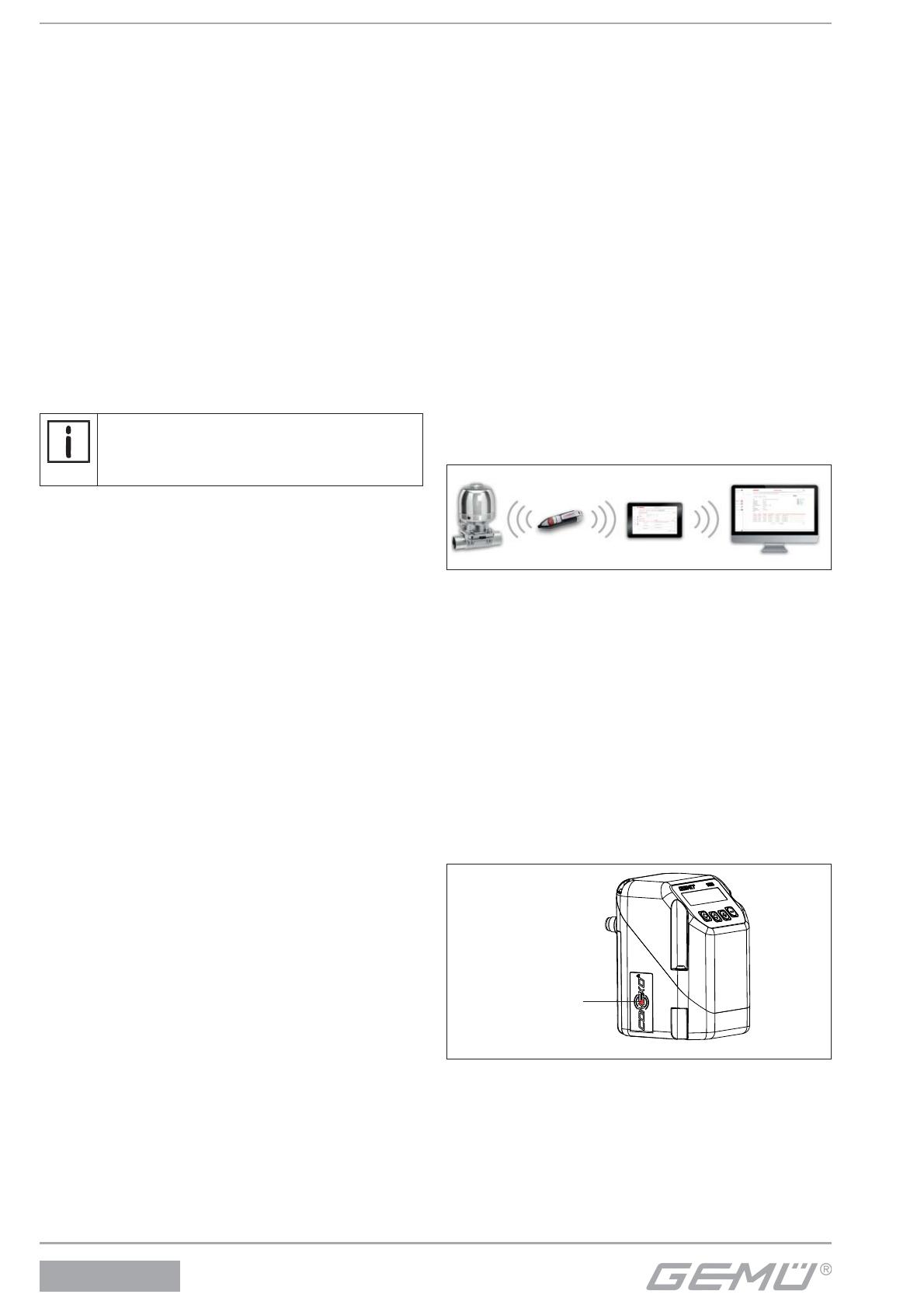
4 / 40
3030
mFlow
1.4 Correct use
7 The GEMÜ 3030 mFlow is suitable for use as defined in the
datasheet. In order to ensure correct product function, the
following notes should be observed. Pay attention to the
information on the product labels.
7 Non-observance of these notes and the notes in the general
operating instructions will void the guarantee on the GEMÜ
3030 mFlow and lead to a loss of legal liability.
7 The GEMÜ 3030 mFlow is used exclusively to measure flow
rates and flow velocities of liquid media and must be used
as specified in the datasheet.
7 Any other use or use above and beyond this is not
permitted. GEMÜ shall not be liable for any consequential
damage. The user carries sole risk.
7 Please pay attention to the pertinent technical safety
regulations when planning both the use and operation of the
device. The designer, plant constructor or operator is always
responsible for positioning and installing the GEMÜ 3030
mFlow.
1.5 Information on use in damp conditions
Under no circumstances whatsoever may the
GEMÜ 3030 mFlow be cleaned with a high
pressure cleaning device, because the protection
class IP 65 is not su cient for this.
The following information is intended to help when installing
and operating the GEMÜ 3030 mFlow in damp conditions:
Lay cables and pipework so that condensate or rain water
that remains on the pipework/cables cannot enter the cable
glands of the M12 plugs of the GEMÜ 3030 mFlow.
Check that all of cable glands for the M12 plug and the
fi ttings are mechanically secured.
1.6 Tools required for installation and assembly
The tools required for installation and assembly are not
included in the scope of delivery.
2 Manufacturer's information
2.1 Transport
G Only transport the flowmeter by suitable means. Do not drop
it and handle it with care.
G Dispose of packing material according to relevant local or
national disposal regulations / environmental protection
laws.
2.2 Delivery and performance
G Check that all parts are present and check for any damage
immediately upon receipt.
G The scope of delivery is apparent from the dispatch
documents and the design from the order number.
G The flowmeter's performance is tested at the factory.
2.3 Storage
G Store the flowmeter free from dust and moisture in its
original packaging.
G Avoid UV rays and direct sunlight.
G Maximum storage temperature: 60 °C.
2.4 Function
The magnetically inductive fl owmeter GEMÜ 3030 mFlow is
suitable for electrically conductive media (conductivity 20 S/
cm) and enables precise measurement of fl ow velocities and
volumetric fl ows of inert and corrosive liquids.
The fl owmeter works largely independently of the pressure,
temperature, density and viscosity of the medium.
The GEMÜ 3030 mFlow has two relay outputs, an RS-232
interface and a pulse and internally supplied current output
(4-20 mA).
As an option, the fl owmeter comes with an infrared interface
and/or a Profi bus DP interface, which can be used to operate
the GEMÜ 3030 mFlow.
The information required can be called-up on the two-line
display of the GEMÜ 3030 mFlow. Self-explanatory help texts
that explain the meaning of the parameters called-up are also
displayed.
The GEMÜ 3030 mFlow is operated using four keys.
2.5 GEMÜ CONEXO
The interaction between valve components equipped with
RFID chips and the corresponding IT infrastructure actively
increases process reliability.
Thanks to serialization, every valve and every relevant valve
component such as the body, actuator or diaphragm, and
even automation components, can be clearly traced and read
using the CONEXO pen RFID reader. The CONEXO app,
which can be installed on mobile devices, not only facilitates
and improves the „installation qualifi cation“ process, but also
makes the servicing process much more transparent and
easier to document. The app actively guides the maintenance
technician through the maintenance schedule and directly
provides him with all the information assigned to the valve,
such as test reports, testing documentation and maintenance
histories. The CONEXO portal acts as a central element,
helping to collect, manage and process all data.
For further information on GEMÜ CONEXO please visit:
www.gemu-group.com/conexo
Installing the RFID transponder
RFID transponder