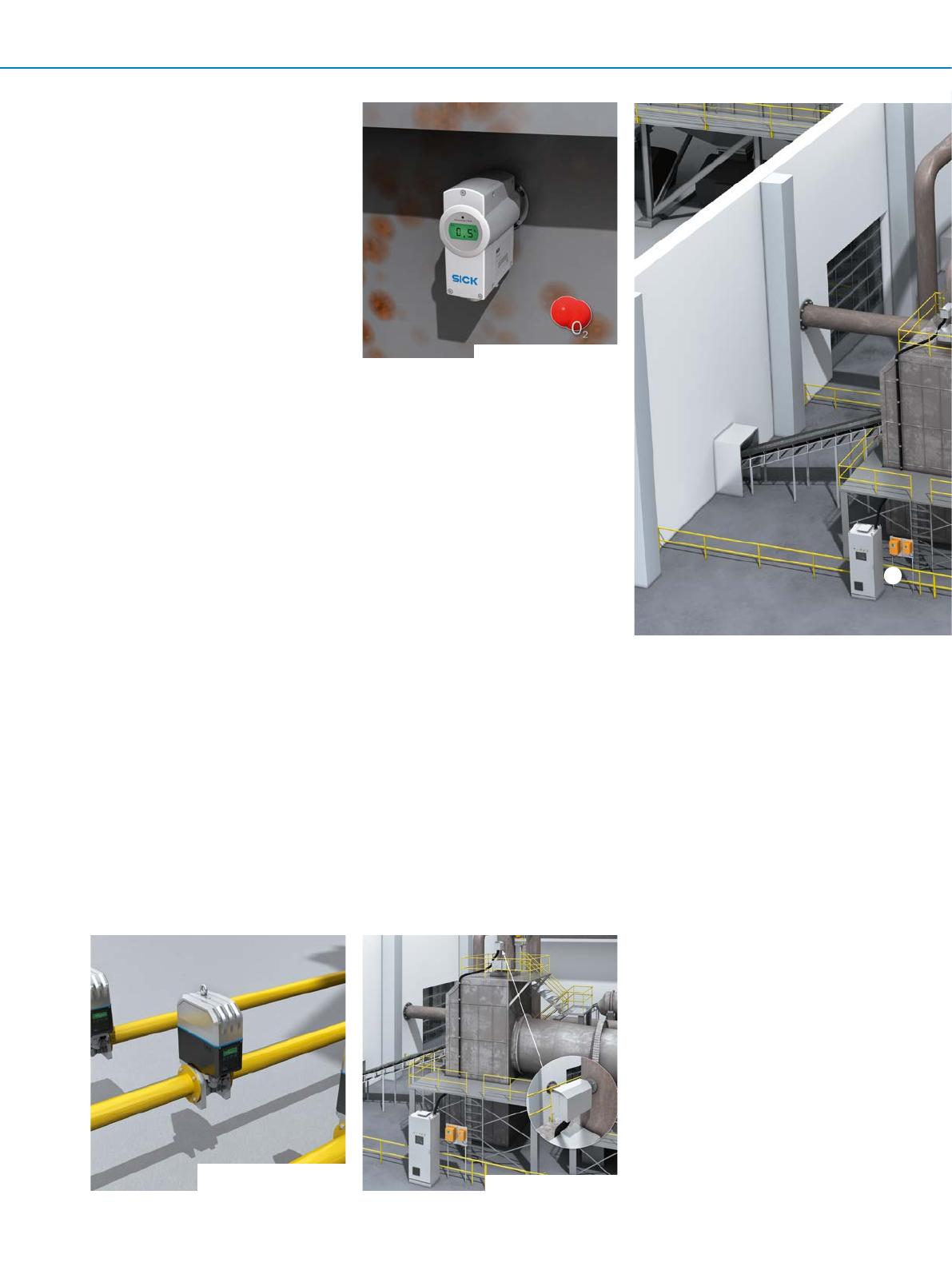
ALUMINUM | SICK18 8026472/2021-03-22
Subject to change without notice
Focus 2: Chip drying
SECONDARY ALUMINUM AND RECYCLING
3
1
Monitoring of fuel stores
Use of aluminum chips in a furnace
means they must rst be thermally pre-
treated. Rotary kilns heat up the chips
to remove not only moisture but also any
contaminants, such as lubricating oils,
grease, lacquer or paint residues. These
kilns are usually red by fossil fuels. Var-
ious sensors can be employed at their
supports to monitor ll levels, pressure
and, in particular, the protective gas
atmosphere. A variety of sensors, such
as TRANSIC100LP are available for use
in explosion-hazardous areas.
TRANSIC100LP g p. 79
3
Gas analysis for process control and optimization in drying ovens
Aluminum chips are a byproduct of the
procedure when further processing
semi-nished products. The chips can
contain signicant organic contaminants
in the form of paints, lacquers, grease
and other impurities. Therefore these
impurities must be thermally treated
and dried before being melted. This
heating of the chips creates poisonous
exhaust gases which are destroyed
during post-combustion.
The METPAX300 process gas analysis
system monitors the exhaust gas from
the drying kilns thereby ensuring an opti-
mal combustion of poisonous gases.
FLOWSIC500 g p. 86
FLOWSIC600-XT g p. 87
2
Flow measurement of fuel at
drying oven
Rotary kilns dry aluminum chips to
remove moisture and contaminants.
The kilns are generally red by natural
gas. To ensure optimal and efcient
operation of the kilns’ burners, it is
necessary to precisely measure the gas
ow per unit of time. The FLOWSIC500
and FLOWSIC600-XT ultrasonic gas
ow meters guarantee high precision
measurement.
METPAX300 g p. 79
This graphic is not presented in the overview.