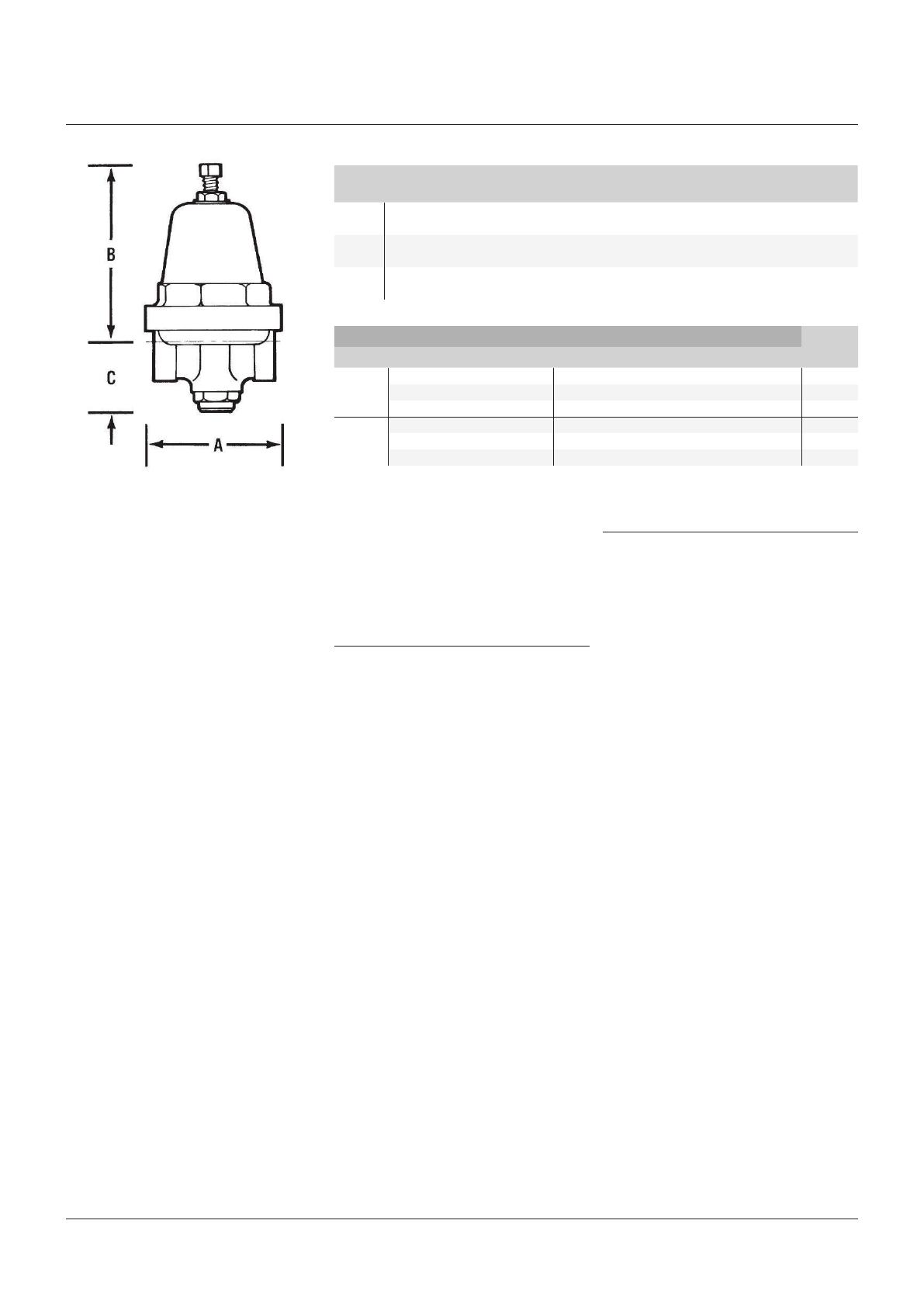
3
CASH VALVE A-360 AND A-361 PRESSURE REGULATORS
INSTALLATION, OPERATION AND MAINTENANCE INSTRUCTIONS
SPECIFICATIONS
Each Type A-360 or A-361 pressure regulator
is equipped with a pressure spring selected to
provide the desired outlet or reduced pressure
setting. The range of adjustment or satisfactory
"working range" of individual springs is shown
above for each valve size. Every regulator has
the "set" pressure and range of adjustment
stamped on a tag fastened to the valve. The
ranges shown below are recommended for
best performance.
Size,
in. (mm.)
Range of Adjustment, psi (bar)
¼
(6.35)
0-5
(0-0.35)
2-35
(0.14-2.41)
20-70
(1.38-4.83)
60-125
(4.14-8.62)
75-200
(5.17-13.8)
100-250
(6.89-17.2)
⅜
(9.53)
0-5
(0-0.35)
2-35
(0.14-2.41)
20-70
(1.38-4.83)
60-125
(4.14-8.62)
75-200
(5.17-13.8)
100-250
(6.89-17.2)
½
(12.7)
0-5
(0-0.35)
2-25
(0.14-1.72)
20-60
(1.38-4.14)
40-80
(2.76-5.52)
75-125
(5.17-8.62)
100-250
(6.89-17.2)
SPRING RANGES
DIMENSIONS
Description Dimensions, in. (mm) Ship. Wt.,
lbs. (kg)
Type Size, in. (mm) Style A B C
A-360
¼ (6.35) 2-Way 2½ (64) 4½ (114) 1⅛ (29) 2 (0.9)
⅜ (9.53) 2-Way 2½ (64) 4½ (114) 1⅛ (29) 2 (0.9)
½ (12.7) 2-Way 2⅞ (73) 4½ (114) 1⅝ (41) 2½ (1.1)
A-361
¼ (6.35) 4-Way 2½ (64) 4½ (114) 1⅛ (29) 2⅛ (1.0)
⅜ (9.53) 4-Way 2½ (64) 4½ (114) 1⅛ (29) 2⅛ (1.0)
½ (12.7) 4-Way 2⅞ (73) 4½ (114) 1⅝ (41) 2⅝ (1.2)
VCIOM-14994 © 2020 Emerson Electric Co. All rights reserved 07/20. Cash Valve is a mark owned by one of the companies in the Emerson Automation Solutions
business unit of Emerson Electric Co. The Emerson logo is a trademark and service mark of Emerson Electric Co. All other marks are the property of their
prospective owners.
The contents of this publication are presented for informational purposes only, and while every effort has been made to ensure their accuracy, they are not to be
construed as warranties or guarantees, express or implied, regarding the products or services described herein or their use or applicability. All sales are governed
by our terms and conditions, which are available upon request. We reserve the right to modify or improve the designs or specifications of such products at any time
without notice.
Emerson Electric Co. does not assume responsibility for the selection, use or maintenance of any product. Responsibility for proper selection, use and maintenance
of any Emerson Electric Co. product remains solely with the purchaser.
Emerson.com/FinalControl
HOW TO ORDER
To order repair parts, refer to the exploded view
of the Type A-360 to identify the part required.
When ordering, please use the part names
listed and provide the valve serial number
stated on the identification tag. Also state the
following: "Repair Parts for A-360 or A361"
and provide:
1. Valve size
2. Service (air, water, oil, non-corrosive liquids,
or gas)
3. Inlet pressure
4. Outlet or delivery pressure range and setting
5. Part description
6. Quantity of each part
7. Valve assembly or serial number stated
on the metal identification tag under the
adjusting screw lock nut.
Servicing the Seat Disk and Bottom O-Ring
1. Loosen the lock nut and turn the adjusting
screw counterclockwise until the pressure
spring is no longer under tension. When
reassembling, run the adjusting screw down
until the lock nut almost touches the spring
chamber. This will give you approximately
the same set as before disassembly.
2. Remove the bottom plug. Take care, as
the bottom plug is under slight tension
as a result of the piston spring acting
against the bottom plug. Remove the
piston subassembly, piston spring, and
bottom o-ring. Lubricate bottom o-ring with
Dow Corning Molykote 111 or equivalent
before installing. Unscrew the pusher
post from the piston to remove the seat
disk. Do not lubricate the seat disk. When
reassembling, ensure that the pusher post
is seated completely against the seat disk;
torque the bottom plug to approximately
10 ft-lbs (13.6 N•m).
3. Remove any debris from the valve body.
4. Inspect all parts for wear and damage and
replace if necessary.
5. Reassemble the valve in reverse order. DO
NOT OVERTIGHTEN. Follow the Operation
Instructions to reset the delivery pressure.