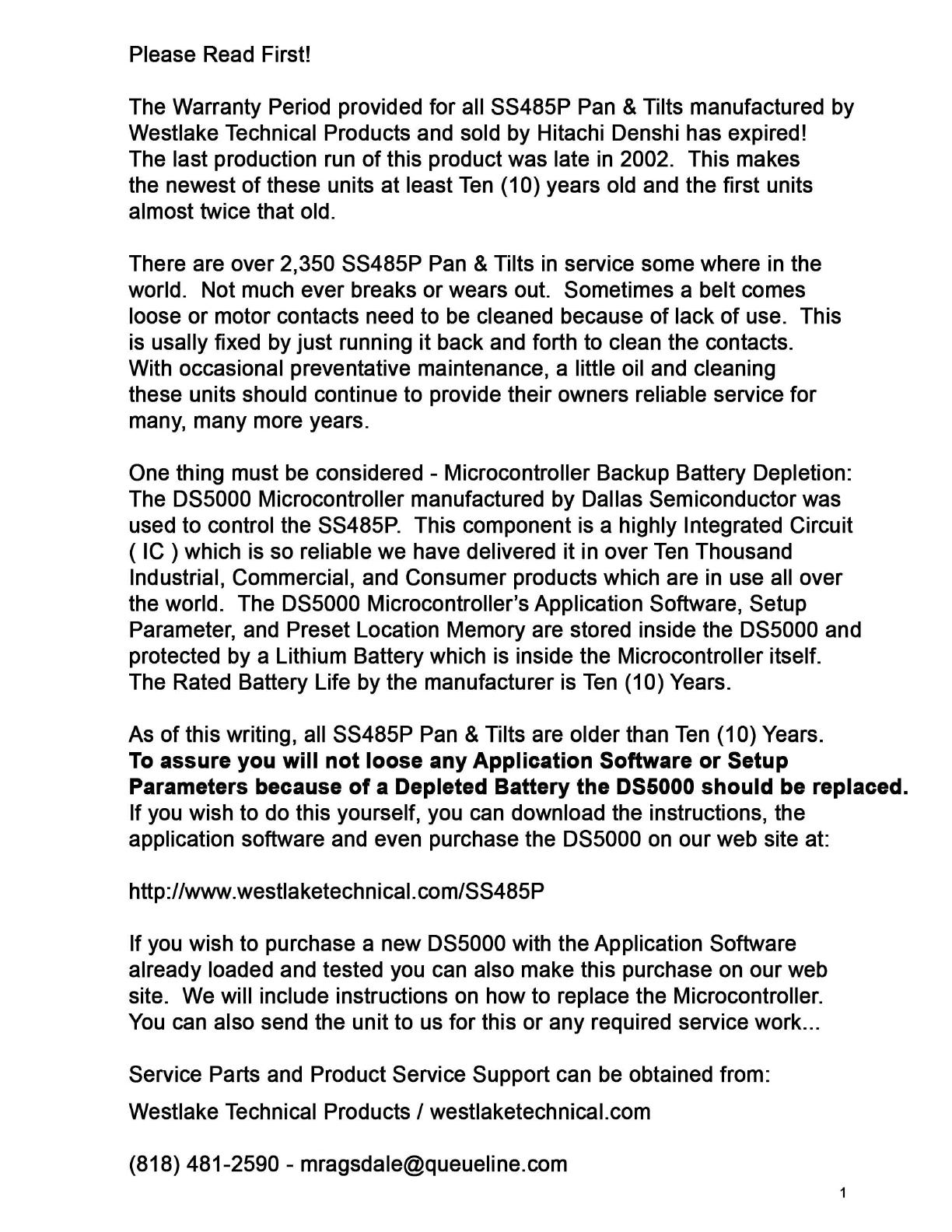
Please Read First!
The Warranty Period provided for
all SS485P Pan & Tilts manufactured by
Westlake Technical Products and sold by Hitachi Oenshi has expired!
The
last production run
of
this product was late
in
2002. This makes
the newest
of
these units at least
Ten
(10) years old and the first units
almost twice that old.
There are
over
2,350 SS485P Pan & Tilts
in
service some where
in
the
world. Not much ever breaks
or
wears out. Sometimes a belt comes
loose
or
motor contacts need to be cleaned because
of
lack
of
use. This
is
usally fixed by just running it back and forth to clean the contacts.
With
occasional preventative maintenance, a little oil and cleaning
these units should continue to provide their owners reliable service for
many, many more years.
One thing must be considered - Microcontroller Backup Battery Oepletion:
The OS5000 Microcontroller manufactured by Oallas Semiconductor was
used to
control the SS485P. This component is a highly Integrated Circuit
(
IC ) which is so reliable we have delivered it in
over
Ten
Thousand
Industrial, Commercial, and Consumer products which are
in
use all over
the
world. The OS5000 Microcontroller's Application Software, Setup
Parameter, and Preset Location Memory are stored inside the OS5000 and
protected by a Lithium Battery which is inside the
Microcontroller itself.
The Rated Battery Life by the manufacturer is
Ten
(10) Years.
As
of
this writing, all SS485P Pan & Tilts are older than
Ten
(10) Years.
To
assure you will not loose any Application Software or Setup
Parameters because of a Depleted Battery the
056000
should be replaced.
If you wish to do this yourself, you can download the instructions, the
application software and even purchase the OS5000 on our web site at:
http://www.westlaketechnical.com/SS485P
If
you wish to purchase a new OS5000 with the Application Software
already loaded and tested you can also make this purchase on our web
site. We
will include instructions on how to replace the Microcontroller.
You can also send the unit to us for this
or
any required service work ...
Service
Parts
and
Product Service Support can
be
obtained
from:
Westlake Technical
Products I westlaketechnical.com
(818) 481-2590 -
mragsdale@queueline.com
2821 Erwin Ranch Road, PO Box 254, Big Bear City, CA 82314