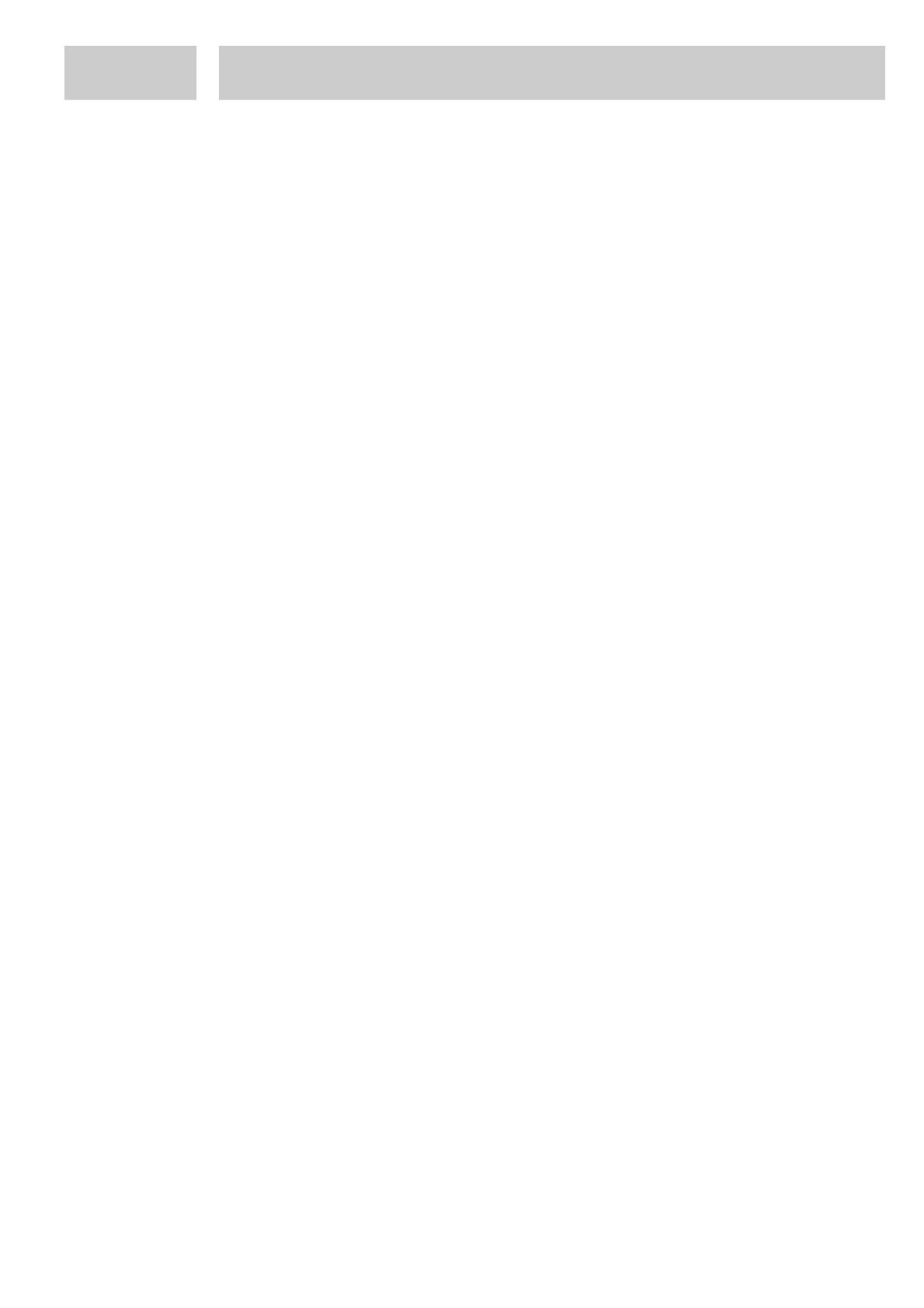
48
Contents
1 INTRODUCTION.................................................................... 50
2 SAFETY ................................................................................. 52
2.1 How to Use this Operating and Service Manual.................................................52
2.2 Informal Safety Measures...................................................................................53
2.3 Intended Use, Warranty......................................................................................53
2.4 Qualification of Operating and Service Staff.......................................................53
2.4.1 Operating staff ....................................................................................................54
2.4.2 Servicing staff .....................................................................................................54
2.5 Organisational Measures....................................................................................54
2.6 Risk Sources.......................................................................................................55
2.7 Safety Systems...................................................................................................55
2.8 Preparation for Operation – Visual Inspection....................................................56
2.9 Safeguard Against Unauthorised Use.................................................................56
3 OPERATION .......................................................................... 57
3.1 Dispensing Station – Total View.........................................................................57
3.2 Displays and Operating Elements.......................................................................58
3.3 Initial Start-up......................................................................................................59
3.3.1 Unpacking...........................................................................................................59
3.3.2 Transportation.....................................................................................................59
3.3.3 Installation...........................................................................................................59
3.3.4 Initial priming with product ..................................................................................60
3.4 Calibration of pumps...........................................................................................62
3.5 Replace Product Container.................................................................................64
3.6 Factory Settings..................................................................................................66
3.7 Operator menu settings ......................................................................................66
3.7.1 Volume ratio........................................................................................................67
3.7.2 Product specific adaptation of the dispensing system........................................68
3.7.3 Maximum pump capacity....................................................................................69
3.7.4 Operating mode..................................................................................................69
3.7.5 Dispense time.....................................................................................................70
3.8 Service menu setup............................................................................................71
3.8.1 Enter password...................................................................................................72
3.8.2 Retract time.........................................................................................................72
3.8.3 Automatic mixer flush cycle (optional) ................................................................73
3.8.4 Flush time (optional) ...........................................................................................74
3.8.5 Enter calibration factor........................................................................................75
3.8.6 Select User Interface language...........................................................................75