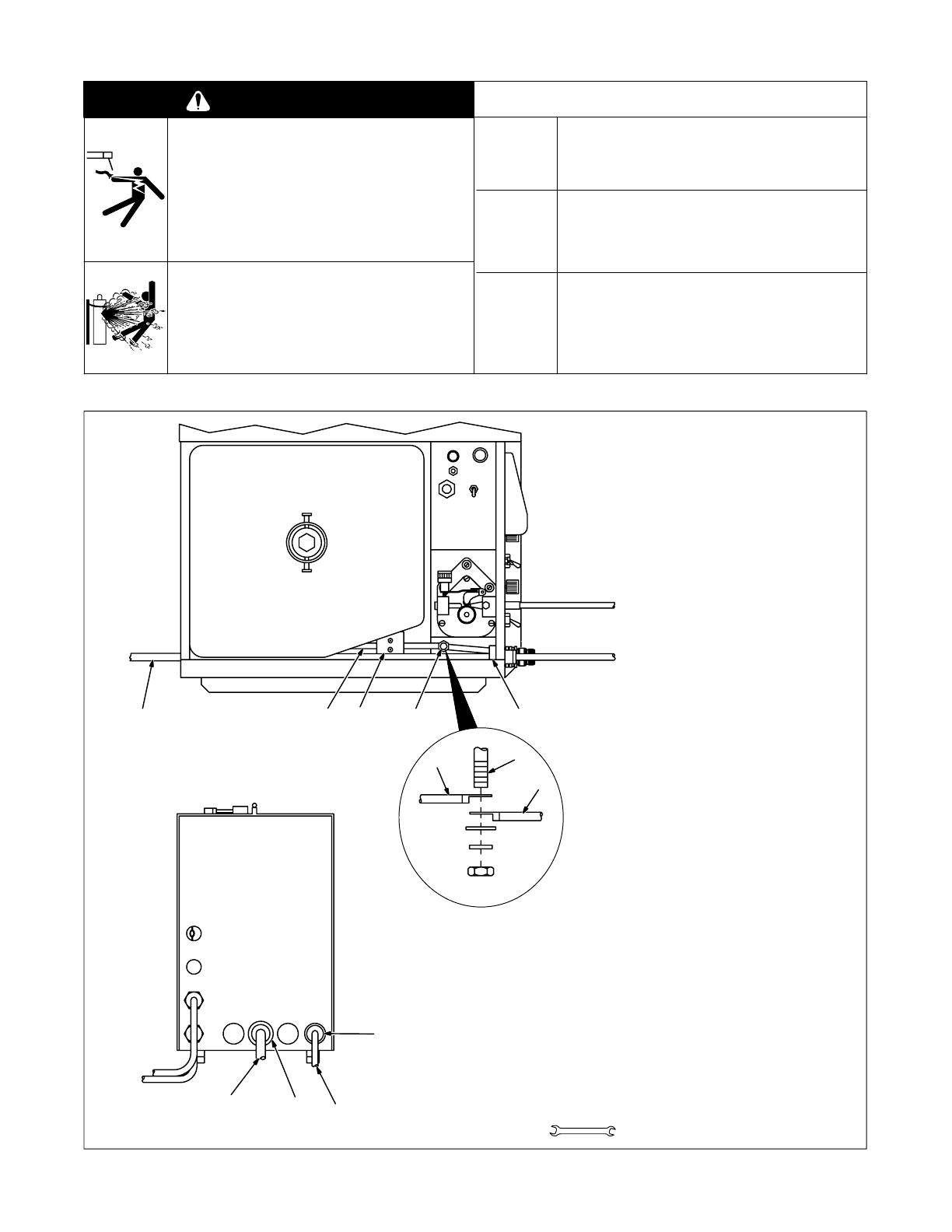
OM-1581 Page 8
3-4. Internal Connections To Feeder
ELECTRIC SHOCK can kill.
• Do not touch live electrical parts.
• Turn OFF wire feeder and welding power source,
and disconnect input power before inspecting or
installing. Stop engine on welding generator.
The welding wire, drive rolls, drive assembly, and all
metal parts touching the welding wire are electrically
live when welding or feeding wire using gun trigger.
CYLINDERS can explode if damaged.
• Keep cylinders away from welding and other
electrical circuits.
• Never touch cylinder with welding electrode.
• Always secure cylinder to running gear, wall, or
other stationary support.
HIGH GAS PRESSURE can cause gun
gas valve to leak.
• Do not use gas pressure above 50 psi (345 kPa) or
mechanical gas valve in gun can leak.
OVERHEATING can damage gun parts.
• If using recirculating coolant system, do not make
connections from coolant system to water valve;
instead make connections directly from coolant
system to gun hoses.
INCORRECT COOLANT FLOWRATE
can damage gun parts.
• Maintain minimum 1 qt/min flowrate at all times.
WARNING
wfwarn7.1* 9/91
A. Air-Cooled Feeder Connections
1 Gas Hose Grommet
2 10 ft (3 m) Gas Hose
3 Rear Of Gas Fitting
Route one end of gas hose through
grommet, and connect hose to rear
of GAS fitting in feeder. Connect re-
maining end of hose to regulator/
flowmeter.
4 Weld Cable To Welding Power
Source
Select and prepare weld cable ac-
cording to welding power source
manual.
5 Weld Cable Grommet
6 Reed Switch
7 Weld Cable Terminal In Feeder
Route one end of weld cable through
grommet, through reed switch, and
connect to weld cable terminal in
feeder. Connect remaining end of
cable to positive (+) weld output ter-
minal on welding power source.
8 Gun Weld Cable
Be sure that terminal of welding pow-
er source weld cable is in direct con-
tact with terminal from gun weld
cable. Close and latch door.
Ref. ST-151 771
Tools Needed:
5/8 in, 1-1/8 in
Top View
4
7
8
Connect To
Positive (+) Weld
Output Terminal On
Welding Power Source
Connect To
Regulator/
Flowmeter
1
5
246 7 3
Rear Panel
Figure 3-8. Air-Cooled Feeder Connections