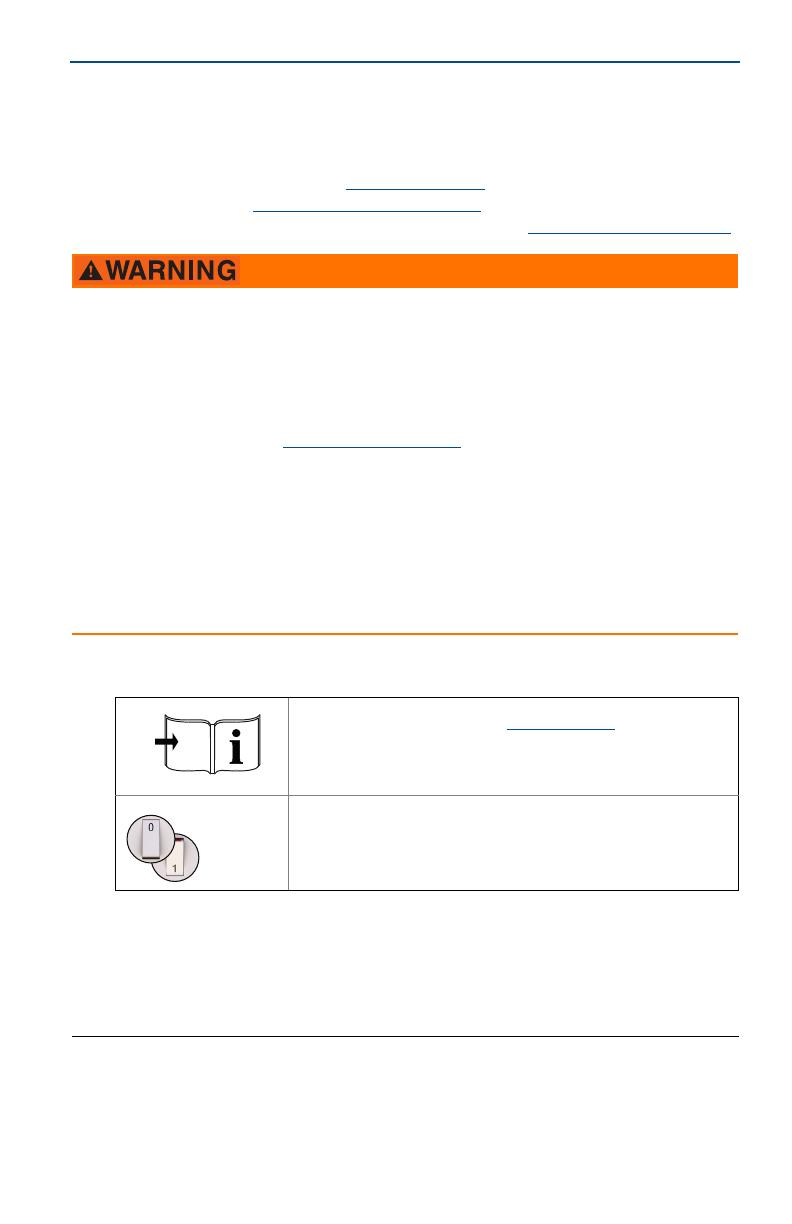
May 2017
2
Quick Start Guide
1.0 About this guide
This Quick Start Guide provides basic guidelines for Rosemount 2140 and
2140:SIS Vibrating Fork Liquid Level Detectors (“level detectors”).
Refer to the Rosemount 2140 Reference Manual
for more instructions, and the
Rosemount 2140 Product Certifications Manual for approvals information and
safety matters. Manuals are available electronically at Emerson.com/Rosemount.
1.1 Symbols used in this guide
1.2 Required equipment
Standard tools e.g. screwdrivers and wire strippers/cutters.
1.3 Contents
Failure to follow safe installation guidelines could result in death or serious injury.
Use the level detector only as specified in this guide and the product reference manual.
The level detector must be installed, connected, commissioned, operated, and maintained by suitably
qualified personnel only, observing national and local requirements that may apply.
The weight of a level detector with a heavy flange and extended fork length may exceed 37 lb. (18 kg).
A risk assessment is required before carrying, lifting, and installing the level detector.
Explosions could result in death or serious injury.
Refer to the Rosemount 2140 Product Certifications Manual
for restrictions associated with the
intrinsically safe, explosion-proof/flameproof and dust approvals for this product.
Electrical shock could cause death or serious injury
Make sure that the level detector is not powered when removing the terminal cover and
making terminal connections.
If the level detector is installed in a high voltage environment and a fault condition or installation error
occurs, high voltage may be present on leads and terminals.
External surfaces may be hot.
Care must be taken to avoid possible burns. The flange and process seal may be hot at high process
temperatures. Allow to cool before servicing.
Refer to the Rosemount 2140 Reference Manual for further
information.
Adobe
®
Acrobat
®
Reader software is needed to view the
document contents.
Switch off power (0) to the level detector.
Switch on power (1) to the level detector.
Installation . . . . . . . . . . . . . . . . . . . . . . . . . . . . . . 3
Adjust display orientation (optional) . . . . . . . . 8
Prepare the electrical connections . . . . . . . . . . 9
Connect wiring and power up . . . . . . . . . . . . . 10
Confirm system readiness . . . . . . . . . . . . . . . . 15
Configure level detector using Guided Setup 15