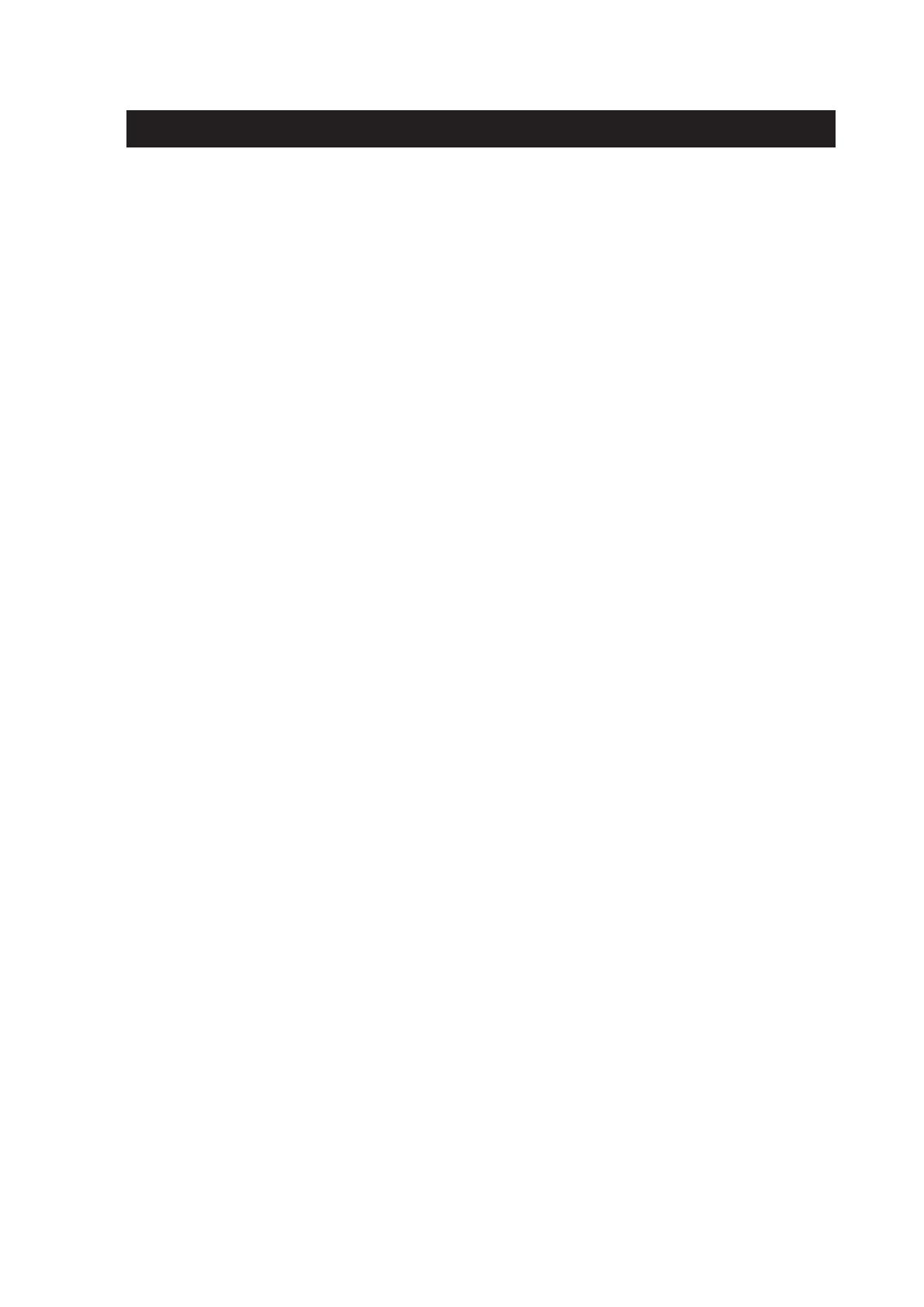
1. Safety ……………………………………………………………………………………………………………1
1.1 The safety symbols used in the manual …………………………………………………………… 1
1.2 Warning …………………………………………………………………………………………………………1
1.3 Caution ……………………………………………………………………………………………………………2
1.4 Earthing and earth fault protection ……………………………………………………………………3
1.5 Electro-magnetic compatibility (EMC) ………………………………………………………………4
1.6 Using an RCD or an RCM device ………………………………………………………………………4
2. Receiving the delivery ……………………………………………………………………………………………………5
2.1 Package label …………………………………………………………………………………………………5
2.2 Type designation code ………………………………………………………………………………………5
2.3 Unpacking and lifting the AC drive ……………………………………………………………………6
2.3.1 Weight of the AC drive …………………………………………………………………………6
2.3.2 Lifting the frames MR8 and MR9 …………………………………………………………6
2.4 Accessories ……………………………………………………………………………………………………7
2.4.1 Frame MR4 …………………………………………………………………………………………8
2.4.2 Frame MR5 …………………………………………………………………………………………8
2.4.3 Frame MR6 …………………………………………………………………………………………9
2.4.4 Frame MR7 ………………………………………………………………………………………10
2.4.5 Frame MR8 ………………………………………………………………………………………10
2.4.6 Frame MR9 ………………………………………………………………………………………11
2.5 "Product modified" label …………………………………………………………………………………11
2.6 Disposal ………………………………………………………………………………………………………11
3. Mounting …………………………………………………………………………………………………………12
3.1 General information about mounting ………………………………………………………………12
3.2 Dimensions for wall mounting ………………………………………………………………………12
3.2.1 Wall mounting of MR4 ………………………………………………………………………12
3.2.2 Wall mounting of MR5 ………………………………………………………………………13
3.2.3 Wall mounting of MR6 ………………………………………………………………………14
3.2.4 Wall mounting of MR7 ………………………………………………………………………15
3.2.5 Wall mounting of MR8, IP21 and IP54 …………………………………………………16
3.2.6 Wall mounting of MR8, IP00 ………………………………………………………………17
3.2.7 Wall mounting of MR9, IP21 and IP54 …………………………………………………18
3.2.8 Wall mounting of MR9, IP00 ………………………………………………………………19
TABLE OF CONTENTS