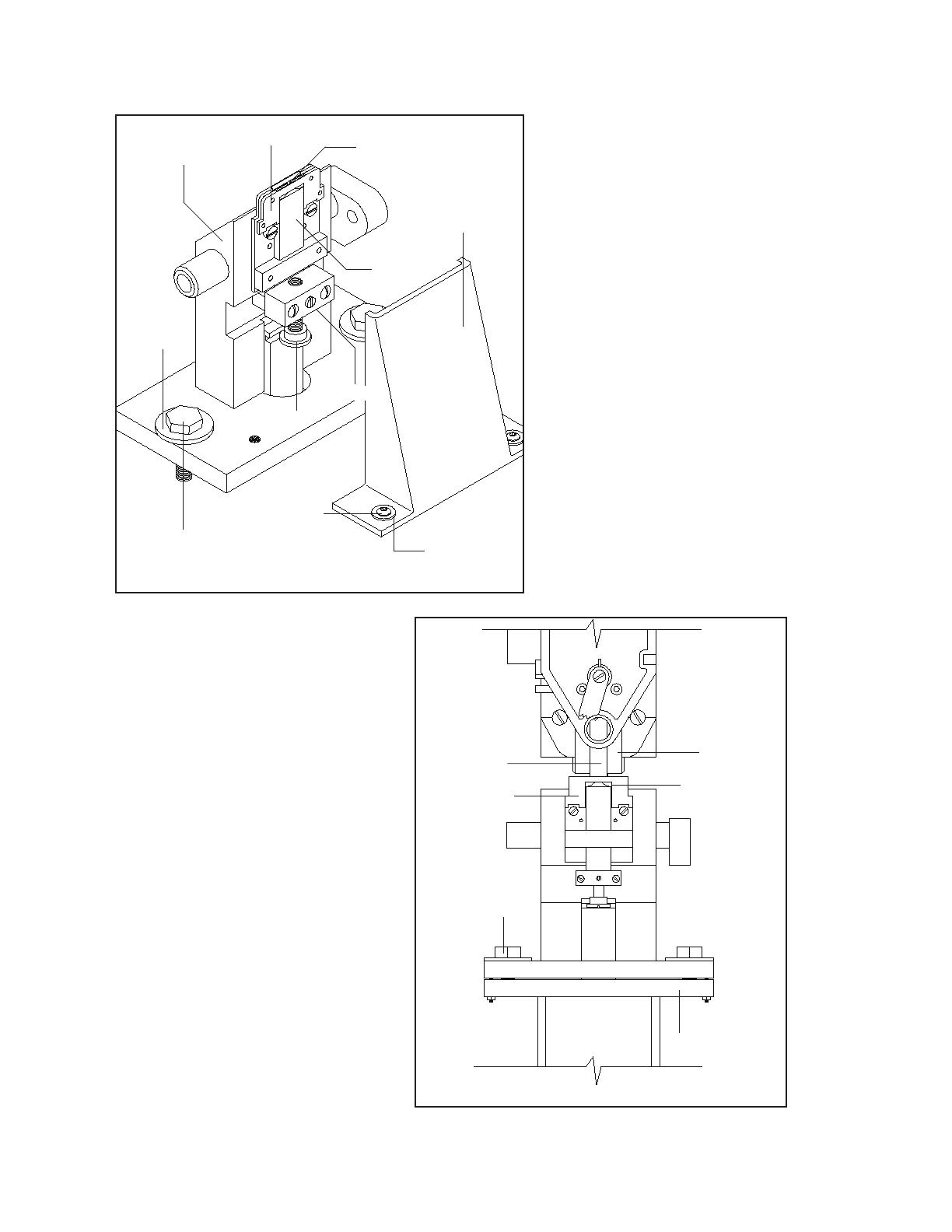
Points (7024B, 7257B).
Loosen the two (2) Screws (G30159)
securing the Clincher Mount Assembly
to the Frame Weldment (G30001A).
With wire threaded through the machine
and the compression set to 1/8” turn the
machine over manually, but stop as the
staple begins to exit the Bender Bar.
Adjust the Clincher Mount Assembly,
side to side, so that the Driver is
centered above the Clincher Points and
in line front to back, so that the legs
of the staple line up with the Clincher
Points. Re-check the side-to-side
adjustment after completing the front-
to-back adjustments and then tighten
the two (2) Screws (PG10512) securing
the clincher Head Guard to the Clincher
Mount Assembly. After tightening,
re-run this procedure to ensure
proper alignment.
and the two (2) Washers (PW14)
securing the Clincher Guard
(G30113) to the Clincher
Mount Assembly (G30044A)
and remove it. Loosen the Set
Screw (UA1428.1) and rotate the
Clincher Slide Adjustment Screw
(18186), which raises or lowers
the Clincher Slide (18182), adjust-
ing the Clincher Points as needed.
Tighten the Set Screw and replace
the Clincher Guard with the two
(2) Washers and two (2) Screws.
If the stitch clinches prop-
erly but the legs are angled away
from its crown, the Clincher Plate
(7253A) may not be aligned with
the Driver (7089E or F). Refer to
both Figure 12 and Figure 13 and
the following instructions for
directions on centering the Clincher
Figure 12 - Adjusting the Clincher Points
18
Figure 13 - Centering the Clincher Points
UA1428.1
18182
18186
PW14 (2)
UA3806.16 (2)
G30044A
7253A
7257B (2) ROUND
OR 7024B (2) FLAT
G30113
7253A
7089E or F
G30159
G30001A
7086A
G30159 (2)
PW12.4 (2)
7257B (2) ROUND
OR 7024B (2) FLAT