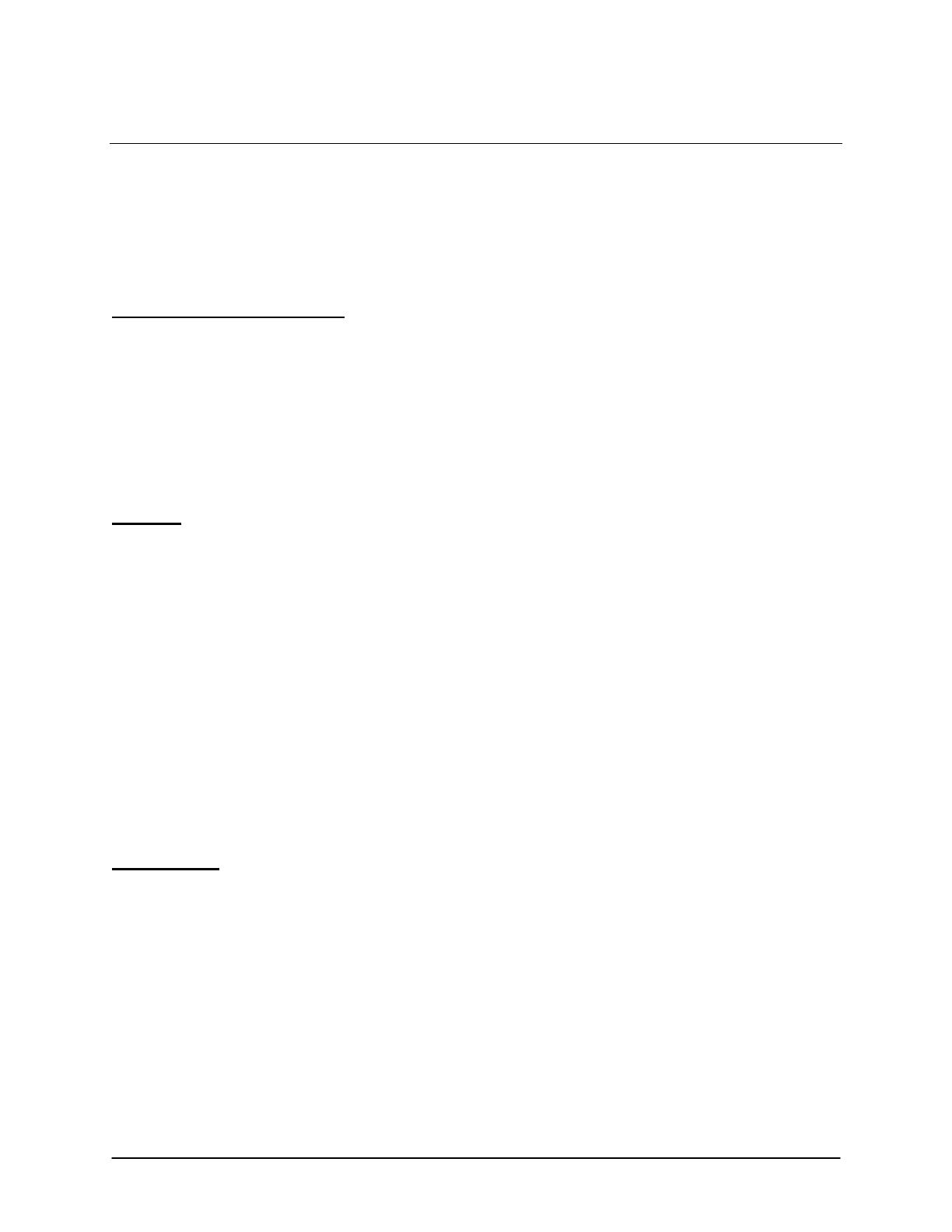
6 of 51
Lab 1: See What the Kinetix 300 Can Do
The Kinetix 300 can operate in two modes when being controlled over Ethernet from a Logix Controller.
The modes are ‘Ethernet/IP External Reference’ and ‘Indexing’.
Ethernet/IP External Reference:
In this Drive Mode, the controller program can take advantage of the Kinetix 300 Add-On Profile (AOP)
that is included in RSLogix5000 v19. After adding a Kinetix 300 drive to the I/O Configuration the AOP
creates an Input and Output TAG structure that can be used to read status information from the drive and
write configuration data to the drive.
The drive can then perform three different types of motion, based on application need. They are position,
velocity or current. In this lab we will demonstrate a simple point-to-point incremental position motion
profile.
Indexing:
In this Drive Mode, we can execute any of the 32 indexes configured in the drive or write indexes down to
the drive as needed via a message instruction. We will demonstrate how to write several index
configurations to the drive using an AOI and then execute them.
The following lab steps the user through loading the necessary files to get the Kinetix 300 servo drive up
and running to see some of its’ functionality in action.
In this lab, you will:
Download configuration file to the Kinetix 300 via MotionView software.
Download RSLogix5000 program file (.acd) to the Compact GuardLogix controller.
Run the drive to execute a velocity jog and configured index moves.
IMPORTANT:
This demo unit processor contains a flash card with logic files that are designed to
download on a power cycle (demo unit power OFF/ON). WHEN YOU NEED TO CYCLE THE DEMO
POWER, YOU WILL NEED TO DOWNLOAD YOUR LAB PROGRAM (.ACD file) TO OVERWRITE THE
FLASH CARD LOGIC FILE!
Follow the steps below to set up the Demo hardware box (before Lab 1). Important: doing this will ‘reset’
your demo unit to a known, default state
1. Turn Power on the demo unit (Power toggle switch above the input power).
2. Connect the Ethernet cable going into the Ethernet module on the Compact GuardLogix rack
3. Make sure there is an Ethernet cable connected from the Ethernet switch and your PC workstation
(this is likely already done for you)