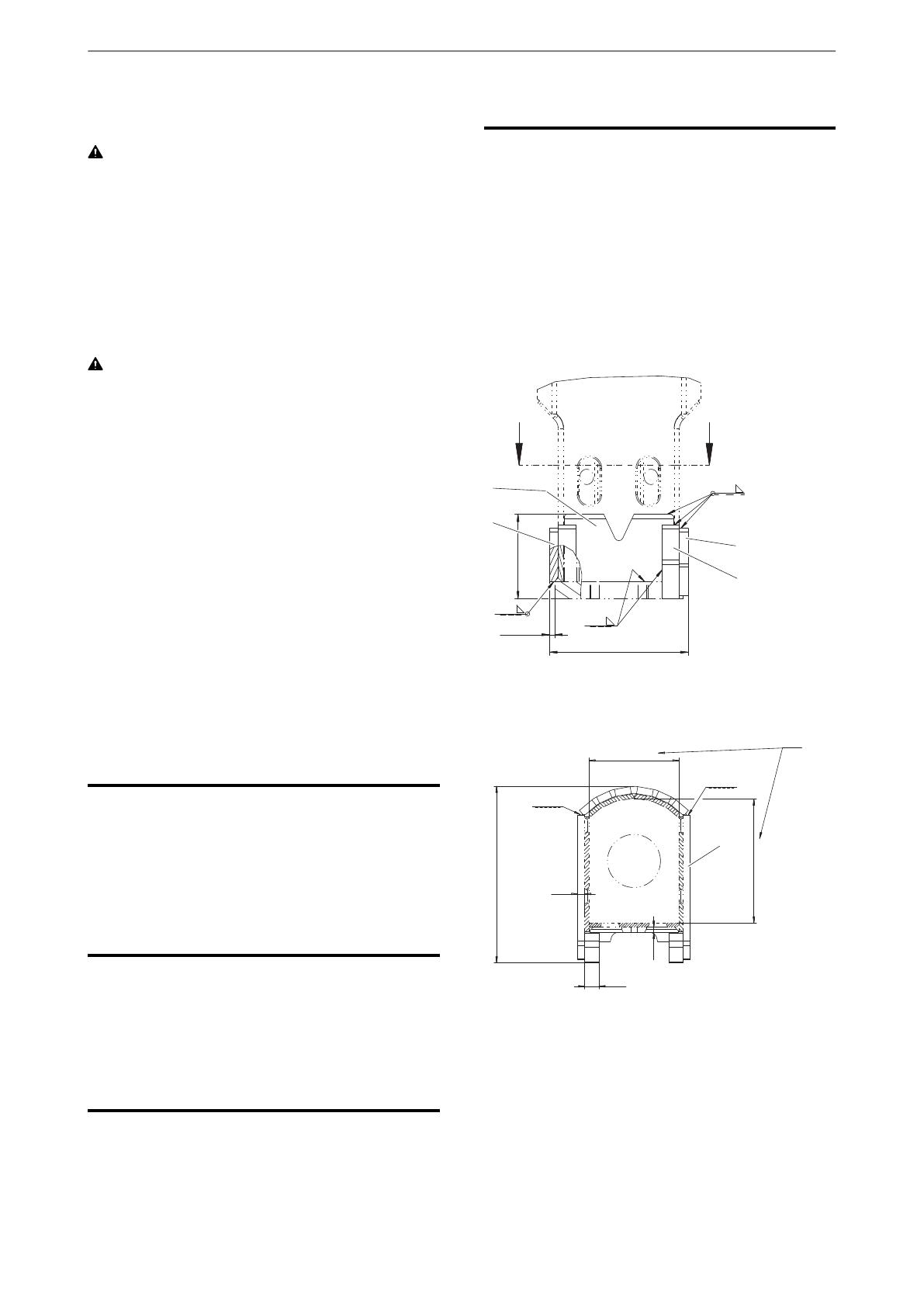
Welding
WARNING Harmful vapors
Chisel paste is flammable. Harmful vapors are
generated when chisel paste is burnt.
► Remove all chisel paste and other contamination
from the breaker box.
► Provide sufficient ventilation during welding.
► Wear personal protective equipment (ambient
air-independent breathing mask) if no air
extraction system is available.
WARNING Risk of fire / explosion
Flammable detergents and chisel paste residues can
ignite or cause an explosion during welding.
► Do not use flammable detergents.
► Carefully remove all detergent residues from the
breaker box.
NOTICE Damage to the breaker box
As the worn parts burn away, the breaker box may
buckle as high levels of heat are produced and the
steel’s properties may change.
► Once a wear part has burnt away, leave the
breaker box to cool before removing the next part.
♦
Remove worn parts one at a time using a flame
cutter or the weld seams removed using a cutting
wheel.
♦
Grind flame-cut areas on the breaker box flat.
Weld seam preparation
♦
Before starting welding work, remove all
contamination on and around the seam edges.
Scale, rust, oil, paint and moisture give off
hydrogen which can jeopardise welding results
and result in cracks.
Preheating temperature
To avoid cracking, a higher working temperature is
recommended depending on steel plate grade,
overall plate thickness and hydrogen content.
♦
Preheat new wear parts to 150 °C to 200 °C.
Optional welding processes
> arc-welding DIN EN ISO 4063
> gas-shielded welding DIN EN ISO 14610
Post-treatment of welds
♦
Make welds without notches or grind free of
notches in order to reduce tension.
♦
Run a non-destructive surface crack test (but at
least a visual weld seam check) of all weld seams.
Tack welds and root beads are the points which are
most susceptible to the formation of cold cracks.
♦
If you find cold cracks in a welded joint, you have
to grind them out or gouge them out with a
carbon arc (grind joint edges) and then perform
a repair weld.
(11.5)
AA
1
4
3
2
B-B
a5
a5
a5
(195)
(318)
Functional dimensions (X) must not be under-run!
Pay attention when welding!
Y
A-A
Y
3
254
+2
0
350
(499)
+2
0
(20)
(40)
(15)
X
3390 7531 018
RX 22Optional equipment