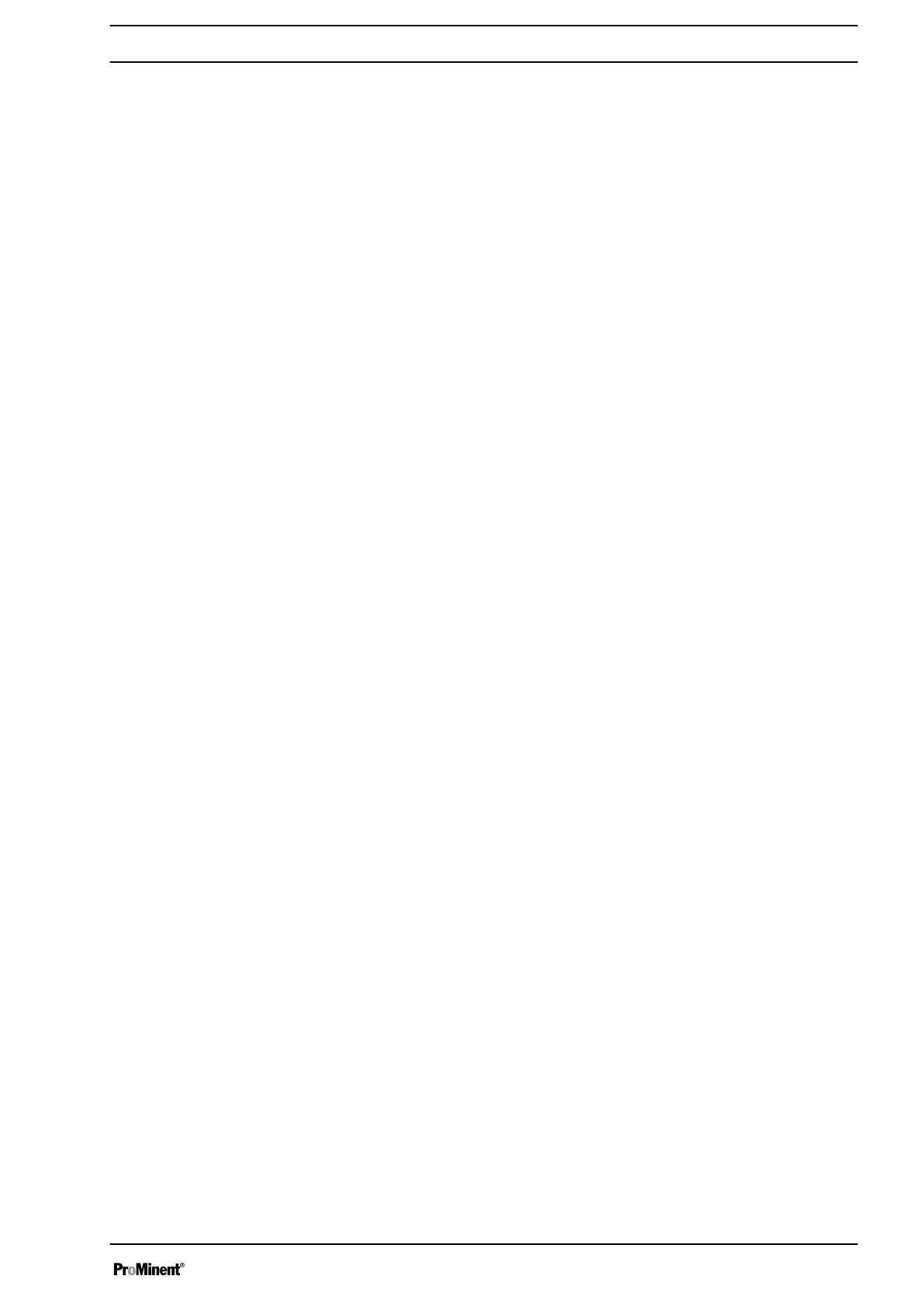
Table of contents
1
Identity code.................................................................................... 5
2 About this pump............................................................................... 8
3 Safety chapter................................................................................. 9
4 Storage, transport and unpacking................................................. 14
5 Overview of equipment and control elements............................... 15
5.1 Overview of equipment......................................................... 15
5.2 Control elements................................................................... 16
5.2.1 Control elements................................................................ 16
5.2.2 Key functions...................................................................... 18
6 Functional description.................................................................... 20
6.1 Device................................................................................... 20
6.2 Capacity................................................................................ 20
6.3 Operating modes................................................................... 20
6.4 Functions............................................................................... 20
6.5 Relay (options)...................................................................... 21
6.6 LED displays......................................................................... 21
6.7 Hierarchy of operating modes, functions and fault sta‐
tuses......................................................................................
22
7 Assembly....................................................................................... 23
7.1 Changing dosing head alignment.......................................... 23
8 Installation, hydraulic..................................................................... 26
9 Installation, electrical..................................................................... 29
9.1 Supply voltage connector - mains voltage............................ 30
9.2 Description of the terminals................................................... 31
9.2.1 "Config I/O” terminal........................................................... 31
9.2.2 "External control" terminal.................................................. 32
9.2.3 "Level switch" terminal....................................................... 33
9.2.4 "Metering monitor" terminal................................................ 34
9.2.5 "Hose rupture indicator" terminal....................................... 34
9.2.6 Relay.................................................................................. 35
10 Basic set-up principles................................................................... 39
10.1 Basic principles for setting up the control............................ 39
10.2 Checking adjustable variables............................................ 41
10.3 Changing to Setting mode................................................... 41
11 Initial commissioning..................................................................... 42
12 Set up /
‘Menu’
.............................................................................. 45
12.1
‘Information’
....................................................................... 45
12.2
‘Settings’
............................................................................ 45
12.2.1
‘Operating mode’
............................................................. 45
12.2.2 Dosing direction............................................................... 49
12.2.3 Concentration................................................................... 49
12.2.4 Calibrate........................................................................... 54
12.2.5 System............................................................................. 56
12.2.6 Inputs/outputs................................................................... 57
12.2.7
‘Priming time’
.................................................................. 59
12.2.8
‘Set time’
......................................................................... 59
12.2.9
‘Date’
............................................................................... 60
12.3
‘Hose replacement’
............................................................ 60
12.4 Timer................................................................................... 60
12.4.1 Activation / deactivation................................................... 60
12.4.2 Setting the timer............................................................... 61
12.4.3 Clear all............................................................................ 68
Table of contents
3