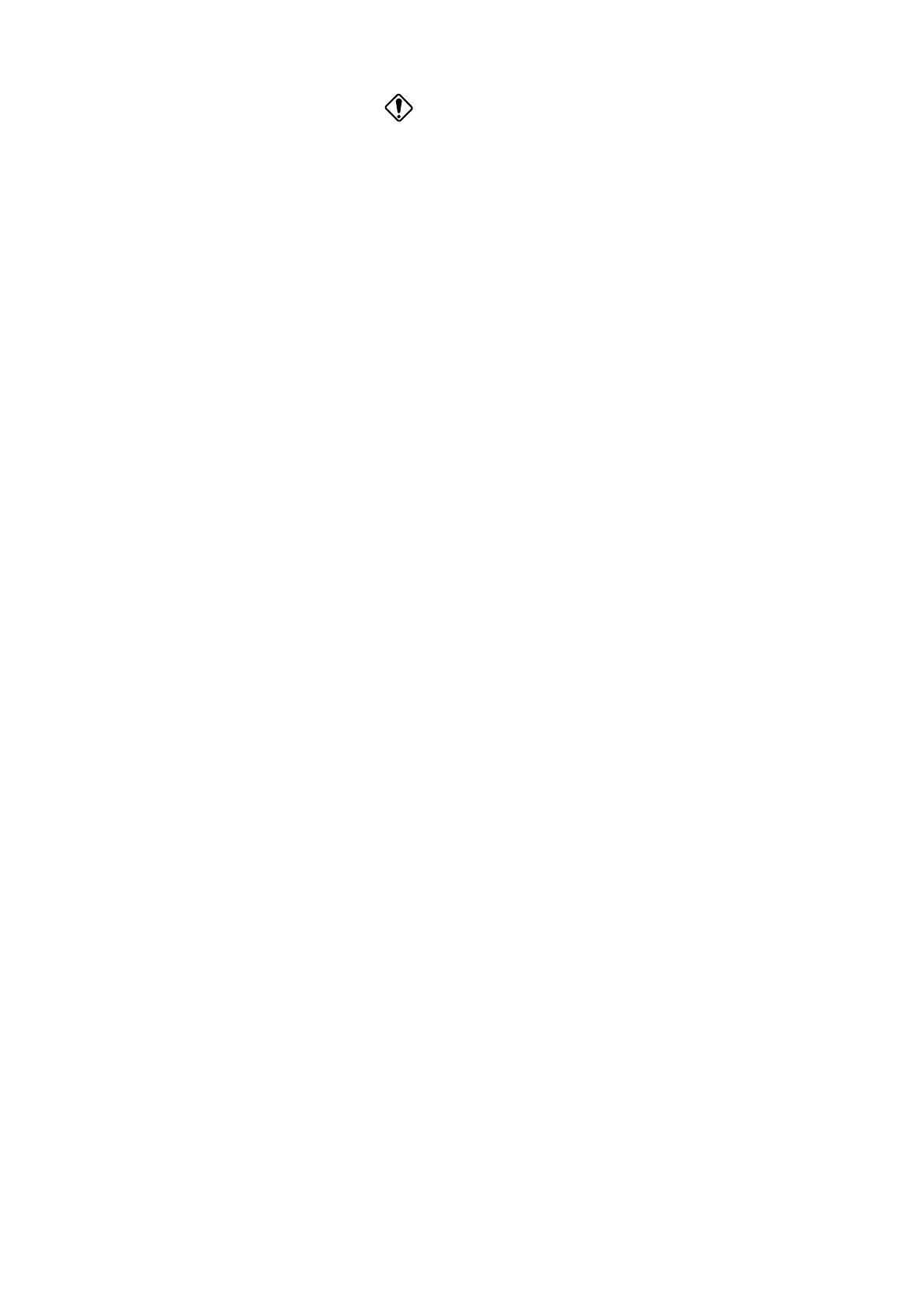
4
(General)
●
●
●
●
●
●
●
(Transportation)
●
(Wiring)
●
●
The operators in charge of transportation, installation, wiring, operation, handling,
maintenance, and inspection should have enough knowledge and technical skill
related to the product. Negligence may cause explosion, ignition of fire, fire, electric
shock, injuries, and damage to the device.
Follow the instruction manual when connecting the product to the power supply
cable. If the product is connected to an incorrect terminal, it may cause fire, damage
to the driver, or electric shock.
Do not forcibly bend, pull, and tuck the motor lead wires or power supply cables.
Negligence may cause electric shock.
If the product is used in lifting and lowering device, install a safety device on the
device side to prevent it from falling. Negligence may cause accidents leading to
injury or death, or damage to the device due to falling down of the lifting and
lowering unit.
If the product is used in lifting and lowering operations, make sure to calculate
resistance value for the consumption of regenerative power generated during
lowering operations, and then apply a suitable regenerative power resistance. If
applied resistance is insufficient, the driver turns on the lamp for alarm for excessive
regeneration and stops the power supply to the motor. The device may fall down if a
P type motor that does not have a built-in electromagnetic brake is used.
Ensure that the driver does not come in contact with water. Negligence may
damage the driver.
When transporting the driver, carry the cooling fin, do not carry the plastic case and
the terminal cover. Negligence may cause coming out and falling down of the unit
and injuries.
If the product is used in a device such as a personnel transport device, make sure
to install a protective device for safety purpose. Negligence may cause accidents
leading to injuries or death, or damage to the device.
Do not use the product in an explosive environment. Negligence may cause
explosion, ignition of fire, fire, electric shock, injuries, and damage to the device.
Do not operate the product when power supply is on. Before operating, turn off the
power supply. Negligence may cause electric shock.