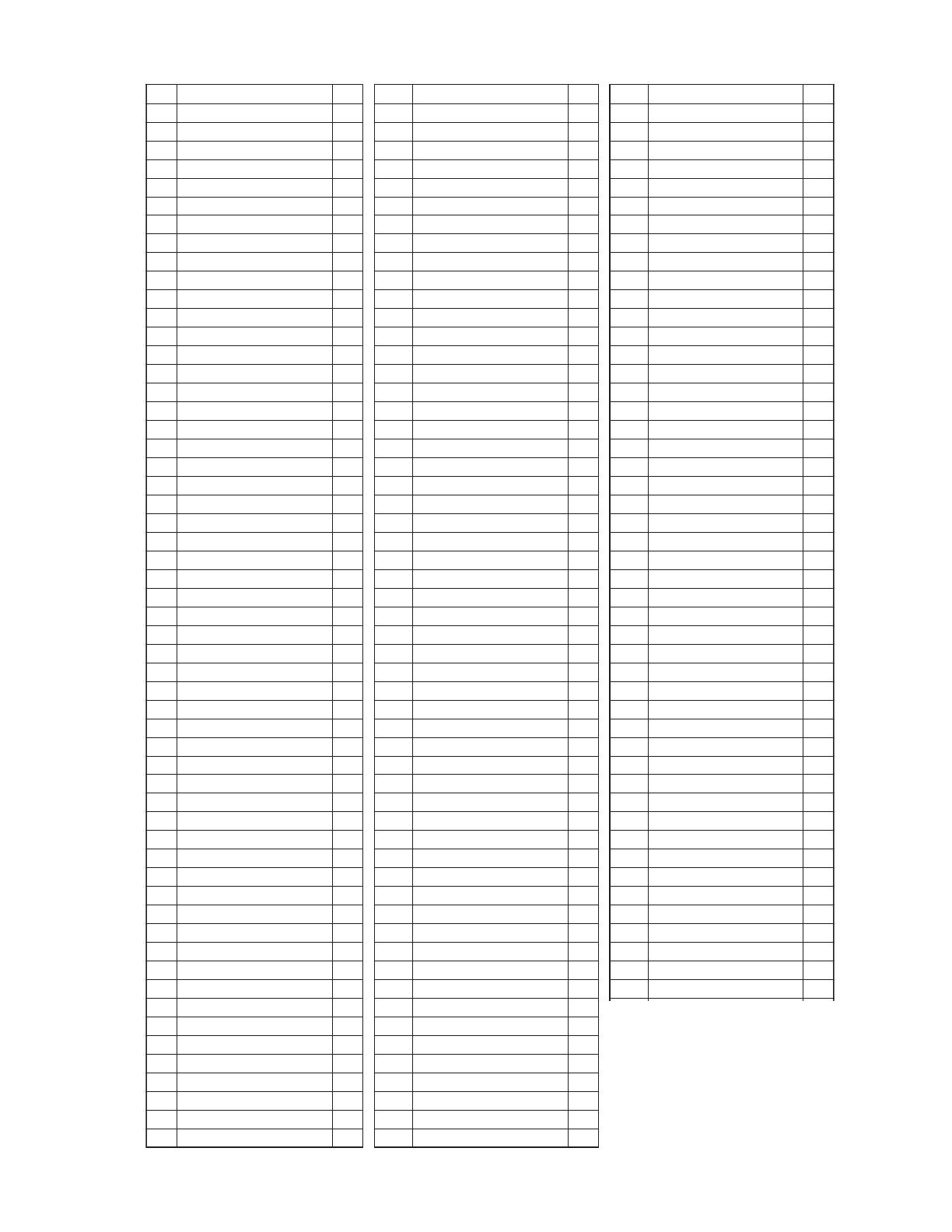
SKU 42933 For replacement parts, please call 1-800-444-3353. Page 16
traPnoitpircseDyt'QtraPnoitpircseDyt'QtraPnoitpircseDyt'Q
1etalpemaN175tloBpotStliT1011wercSdeeF1
28×5MwercS285)2(gnirpSeru
sserP1111elbaC1
35rehsaW195revoCeldnaH1211esaBmrA1
4ediuGtsuD10621×9.3tSwercSgnippaT231121rehsaW1
5bonKxednIekoY3165.6×9.2tSwerc
SgnippaT2411)5(gnirpSerusserP2
66MtuN9626revoCeldnaH151106×21MtloB1
7wercSgnipmalCdrauG13602×4niPgnirpS1611eceiPreffuB2
8drau
GelbixelF146tuNtelloC171121MtuN2
9lebaL1568×5MwercS1811revoCelbaC1
01drauGytefaS166eldnaHpmalC1911)5(gnirpSerusserP1
11etalPdrau
G176draoBgnirpS2021retsloBdexiF1
215rehsaWgnirpS186draoBlebaLelacS1121redniBelbaC1
31y'ssAmrAkcabkcik-itnA196csiDlaiD1221hcti
wS1
41tloBdutS10761×8.4tSwercSgnippaT6321esaChctiwS1
51)tfel(41×8MtloB117bonKkcoLleveB1421yeK1
61egnalFedistuO127)1(gnirpSeru
sserP1521AelbaT1
71edalBwaS137pilc-C1621BelbaT1
81egnalFedisnI1a47bonKkcoLleveB1721CelbaT1
91tfahSraeG1b47bonKkcoLegairraC1821tuNts
oPediuG1
02)1(gnirpSerusserP157niPbonK1921pilc-C1
126gniRgniniateR167tfahSgniraeB403121×6niPgnirpS2
22niPreppotS17792006gnira
eB4131nmuloC1
3222×4ByeK187tfahSreppotS1231liaRediuG1
4283×8.4tSwercSgnippaT29761rehsaWnihT233101×5MwercS1
5202×5MwercS108egairr
aC1431recapS1
62revoCesaCraeG1188rehsaWgnirpS85314rehsaW2
728×4MwercS2288MtuN8631eguaG1
8240108gniraeB1386rehsaW5731pmalCwercS2
92rehs
aWreppotS148faeLgnirpSdexiF1831rehsaWgnipmalCnmuloC1
03raeGtuptuO158tloBdaeH.xeH193121×5MwercS1
1302gniRgniniateR168elffaB
hctiwS104121rehsaW1
23014101KgniraeBeldeeN178AeldnaH114156×21MtloBkcoLmrA1
3307×5wercSdooW288)4(gnirpSerusserP1241bonKxedn
ImrA1
4321rehsaWnihT298elffaBssorC1341)3(gnirpSerusserP1
53tfahSelddiM109recapS1441pilc-C1
63316121KgniraeBeldeeN119)4(gnirpS
erusserP1541esaBnmuloC1
73raeGelddiM129nottuBnOkcoL1641pmalCelbaT2
8323×8.4tSwercSgnippaT439reggirT174141×8MtloB4
93revoCesaC
raeG14961×6MwercS284161×8MtloBdaeHdnuoR4
0420108gniraeB2596rehsaW29418MrehsaW4
14ediuGnaF1696rehsaWgnirpS2051dnatS2
24naF179BeldnaH11
51)thgiR(esaBdexiF1
34rotoR18921×6MwercS5251esaB1
44rotatS1996rehsaWgnirpS5351)tfeL(esaBdexiF1
54lioCelbaC5001eldnaHgnitavelE145
161×6MtloBdaeHdnuoR4
64pilCelbaC1101paCmrA156161x6MwercS4
745.9×5.3tSwercSgnippaT120121×4MwercS2661gnisuoH1
84revoCelbaC130141
MtuNtelloC1761gnihsuB1
9461×9.3tSwercSgnippaT240141rehsaW1
0501×4MwercS2501pmalCdroC1
15paCdnE1601eriWdaeL1
25tuNpirG1701)tfeL(l
ebaLelacS1
35kcuhCtelloClacinoC1801mrA1
45redloHhsurB21-801wercSdaeHtalFknusretnuoC8
55hsurBnobraC22-801liaR2
65paChsurB2901)
thgiR(lebaLelacS1
Parts List