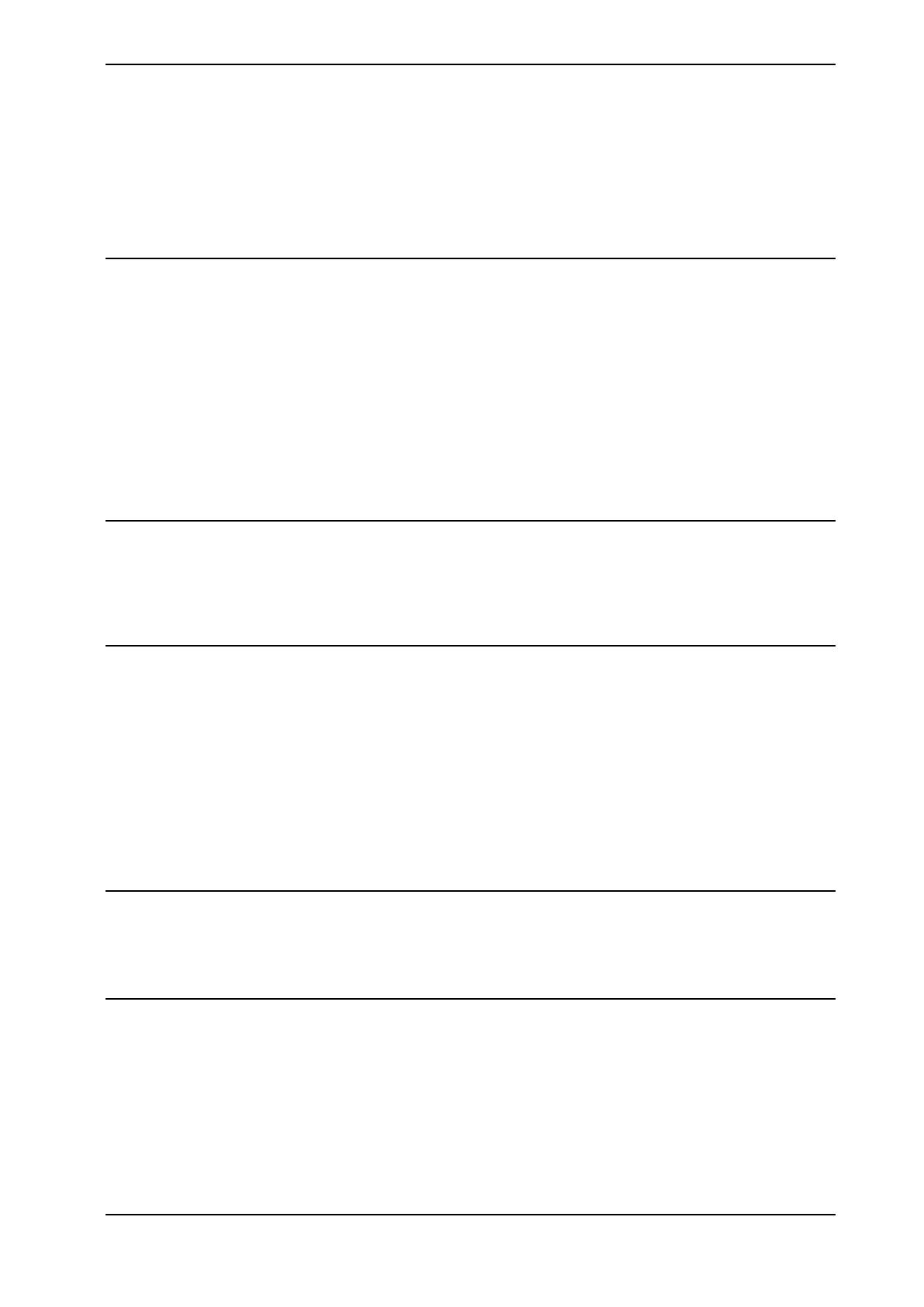
Table of contents
7Overview of this manual ...................................................................................................................
9Product documentation ....................................................................................................................
111 Safety
111.1 About this chapter .............................................................................................
121.2 Applicable safety standards ................................................................................
141.3 Safety actions ...................................................................................................
141.3.1 Stop the system ......................................................................................
151.3.2 Recover from emergency stops .................................................................
161.3.3 Extinguishing fires ...................................................................................
171.4 Working in a safe manner ...................................................................................
171.4.1 For your own safety .................................................................................
181.4.2 About the manual mode ...........................................................................
191.4.3 About the automatic mode ........................................................................
201.5 Safety terminology ............................................................................................
201.5.1 Safety signals in the manual ......................................................................
221.5.2 Protective stop and emergency stop ...........................................................
232 Introduction to the IRB 14000 robot system
232.1 What is IRB 14000? ...........................................................................................
242.2 What is a FlexPendant? ......................................................................................
252.3 What is RobotWare? ..........................................................................................
262.4 What is RobotStudio? ........................................................................................
272.5 What is RobotStudio Online? ...............................................................................
293 Using the IRB 14000
293.1 Axes and coordinate systems ..............................................................................
313.2 Jogging ...........................................................................................................
313.2.1 What is jogging? .....................................................................................
333.2.2 Motion modes .........................................................................................
343.2.3 Coordinated jogging ................................................................................
363.3 Lead-through ....................................................................................................
373.4 Operating modes ..............................................................................................
393.5 Collision avoidance ...........................................................................................
413.6 Collision ..........................................................................................................
423.7 Programming and testing ....................................................................................
453.8 I/O signals .......................................................................................................
463.9 User authorization .............................................................................................
474 Calibration
474.1 Introduction ......................................................................................................
484.2 Calibration scale and correct axis position .............................................................
504.3 Updating revolution counters ...............................................................................
564.4 Verifying the calibration position ..........................................................................
575 System parameters
575.1 Introduction ......................................................................................................
585.2 Topic I/O System ...............................................................................................
585.2.1 Collision Avoidance .................................................................................
595.2.2 Connection Timeout Multiplier ...................................................................
605.3 Topic Motion ....................................................................................................
605.3.1 Coll-Pred Safety Distance .........................................................................
615.3.2 Global Speed Limit ..................................................................................
625.3.3 Arm Check Point Speed Limit ....................................................................
635.3.4 Arm-Angle Definition ................................................................................
Operating manual - IRB 14000 5
3HAC052986-001 Revision: E
© Copyright 2015-2018 ABB. All rights reserved.
Table of contents