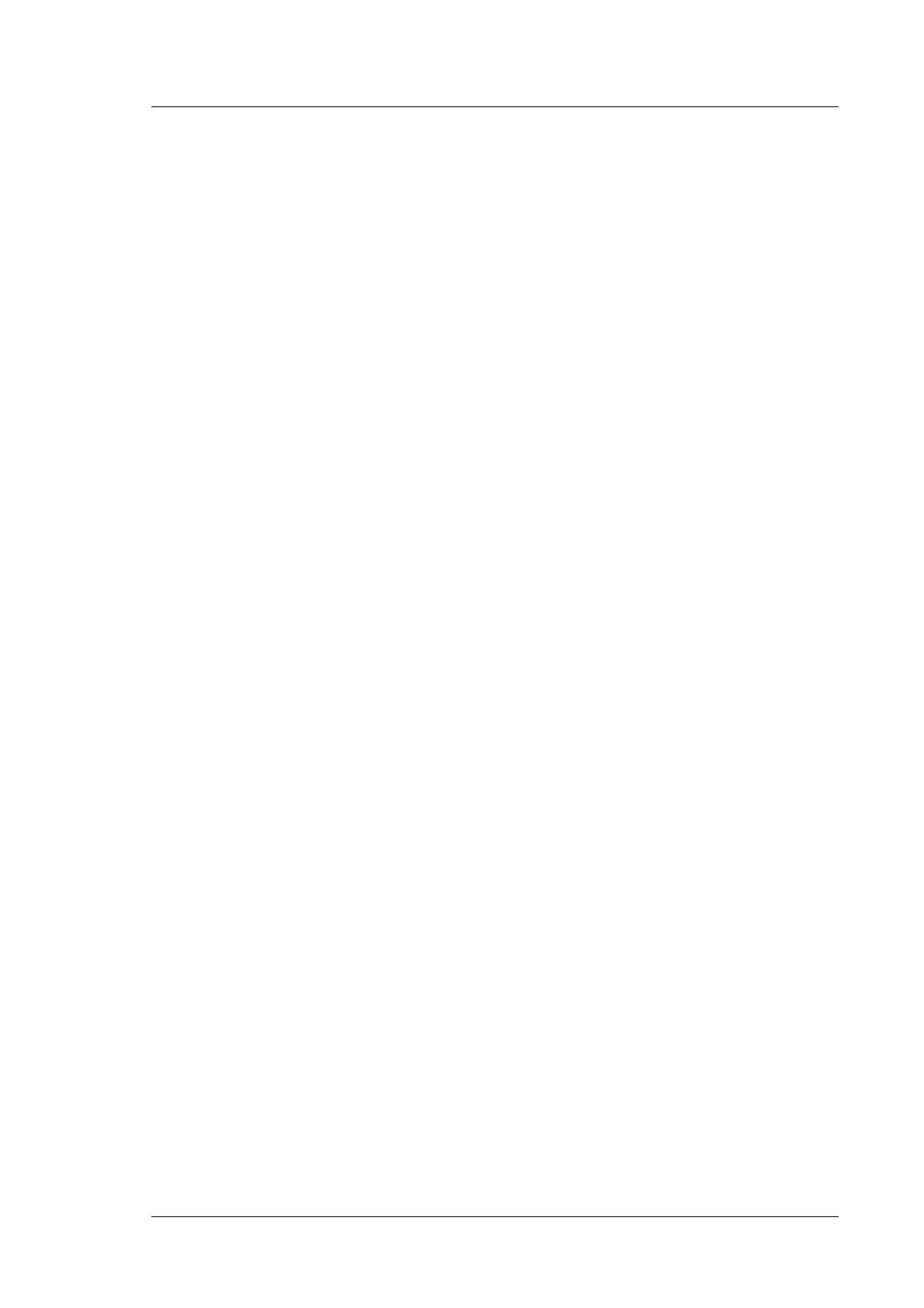
UltiMate 3000 Series:
FLM-3x00 Flow Managers
Table of Contents
1 Introduction................................................................................................................... 1
1.1 Operating Instructions ...........................................................................................1
1.2 Safety Information................................................................................................. 1
1.2.1 Symbols on the Instrument and in the Manual .................................................. 2
1.2.2 General Safety Precautions................................................................................ 3
1.2.3 Consignes Générales de Sécurité....................................................................... 5
1.3 Intended Use .......................................................................................................... 8
1.4 Federal Communications Commission (FCC) Note.............................................. 8
2 Overview........................................................................................................................ 9
2.1 Unit Description..................................................................................................... 9
2.2 Operating Principle (UltiFlow)............................................................................11
2.3 Supported Configurations....................................................................................12
2.3.1 General.............................................................................................................12
2.3.2 Biocompatible Flow Managers........................................................................ 13
2.4 Interior Components ............................................................................................ 17
2.5 Front Panel Elements........................................................................................... 19
2.6 Rear Panel............................................................................................................ 20
2.7 Column Switching Valve.....................................................................................20
2.8 Flow Splitter ........................................................................................................ 21
2.9 Leak Sensors........................................................................................................ 22
2.10 System Wellness and Diagnostics ....................................................................... 23
3 Installation................................................................................................................... 25
3.1 Facility Requirements.......................................................................................... 25
3.2 Unpacking............................................................................................................ 25
3.3 Positioning the Flow Manager in the UltiMate 3000 System..............................26
3.4 Connecting the Flow Manager............................................................................. 27
3.4.1 USB.................................................................................................................. 27
3.4.2 Power Connection............................................................................................27
3.4.3 Digital I/O........................................................................................................ 28
3.5 Setting Up the Flow Manager in Chromeleon.....................................................28
3.5.1 Loading the USB Driver for the Flow Manager.............................................. 28
3.5.2 Installing the Flow Manager............................................................................ 30
3.5.3 Configuring the Flow Manager........................................................................ 31
3.5.3.1 Initial Installation ....................................................................................31
3.5.3.2 Changing the Basic Configuration or Selecting Advanced Settings....... 33
3.5.4 Assigning the Flow Splitter ............................................................................. 36
4 Preparation for Operation (Startup) ........................................................................ 37
4.1 Overview of Actions............................................................................................ 37
4.2 Opening the Front Panel Door............................................................................. 38
4.3 Connecting a Waste Tubing................................................................................. 39
4.4 Connecting the Drain System .............................................................................. 40
Operating Instructions Page i