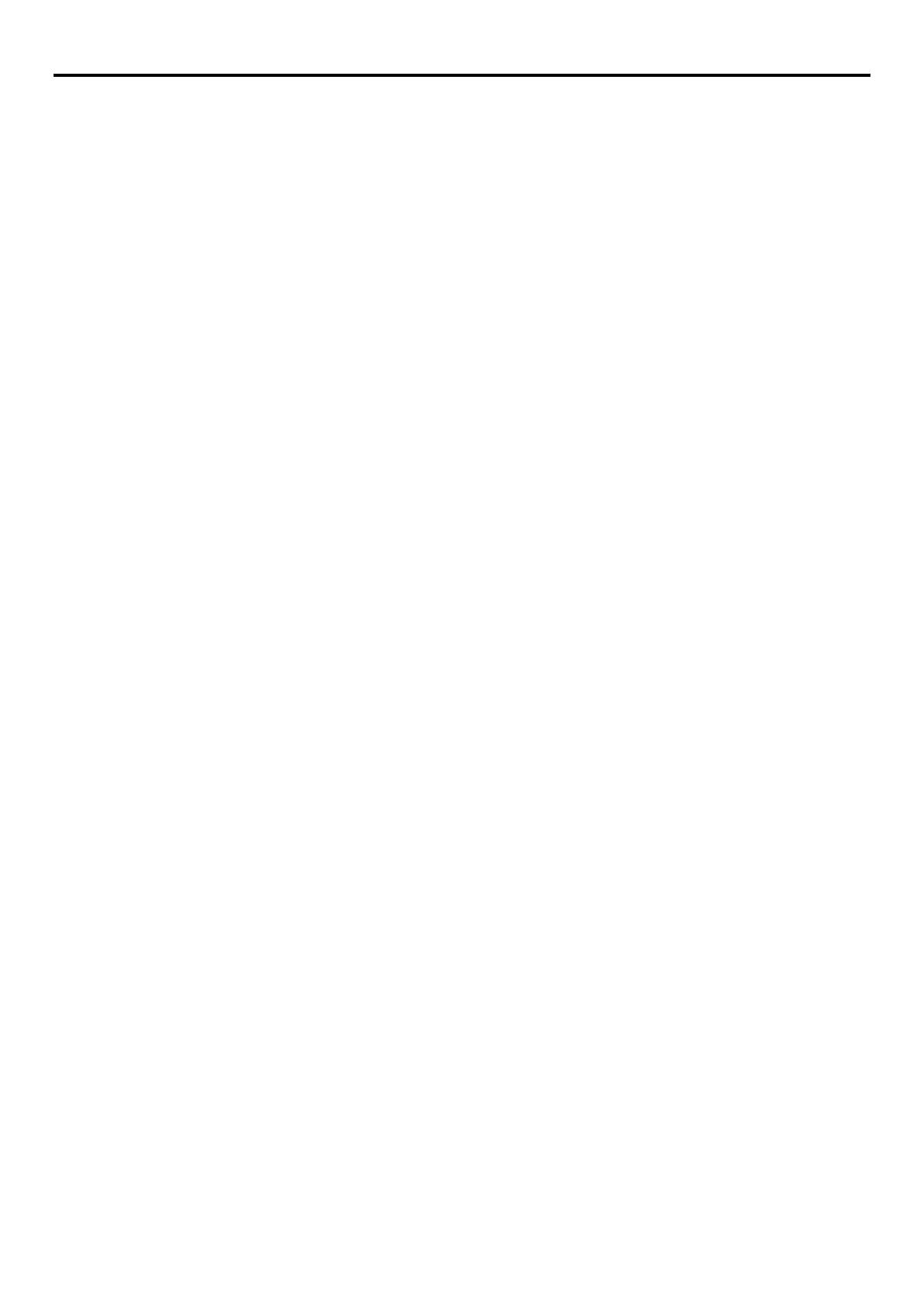
5
1. Table of Contents
1. Table of Contents __________________________________________________________________ 5
ACS255 – IP20 (115V) EASY START-UP GUIDE _________________________________________ 7
ACS255 – IP66 (115-480V Switched Variants) EASY START-UP GUIDE ____________________________ 8
ACS255 – IP66 (115-480V Non-Switched Variants) EASY START-UP GUIDE ________________________ 9
2. Safety ___________________________________________________________________________ 11
2.1. What this chapter contains______________________________________________________________ 11
2.2. Use of warnings _______________________________________________________________________ 11
2.3. Safety in installation and maintenance ____________________________________________________ 11
2.4. Safety in start-up and operation _________________________________________________________ 12
3. General Information and Ratings _____________________________________________________ 14
3.1. Type designation key __________________________________________________________________ 14
3.2. Drive Model Numbers – IP20 ____________________________________________________________ 15
3.3. Drive Model Numbers – IP66 ____________________________________________________________ 15
4. Mechanical Installation_____________________________________________________________ 16
4.1. General _____________________________________________________________________________ 16
4.2. Mechanical Dimensions and Mounting – IP20 Open Units _____________________________________ 16
4.3. Guidelines for Enclosure Mounting – IP20 Units _____________________________________________ 16
4.4. Mechanical Dimensions – IP66 (Nema 4X) Enclosed Units _____________________________________ 17
4.5. Guidelines for Mounting Enclosed Units ___________________________________________________ 17
4.6. Gland Plate and Lock Out _______________________________________________________________ 18
4.7. Removing the Terminal Cover ___________________________________________________________ 18
5. Power Wiring _____________________________________________________________________ 19
5.1. Grounding the Drive ___________________________________________________________________ 19
5.2. Wiring Precautions ____________________________________________________________________ 20
5.3. Connection Diagram ___________________________________________________________________ 21
5.4. Drive & Motor Connections _____________________________________________________________ 22
5.5. Motor Terminal Box Connections _________________________________________________________ 22
5.6. Using the REV/Off/FWD Selector Switch (IP66 Switched Version Only) __________________________ 23
6. Control Wiring ____________________________________________________________________ 24
6.1. Control Terminal Connections ___________________________________________________________ 24
6.2. RJ45 Data Connection __________________________________________________________________ 24
7. Operation ________________________________________________________________________ 25
7.1. Managing the Keypad __________________________________________________________________ 25
7.2. Changing Parameters __________________________________________________________________ 25
7.3. Resetting to Factory Default Settings ______________________________________________________ 25
8. Quick Start-up and Control __________________________________________________________ 26
8.1. Quick Start-up Terminal Control _________________________________________________________ 26