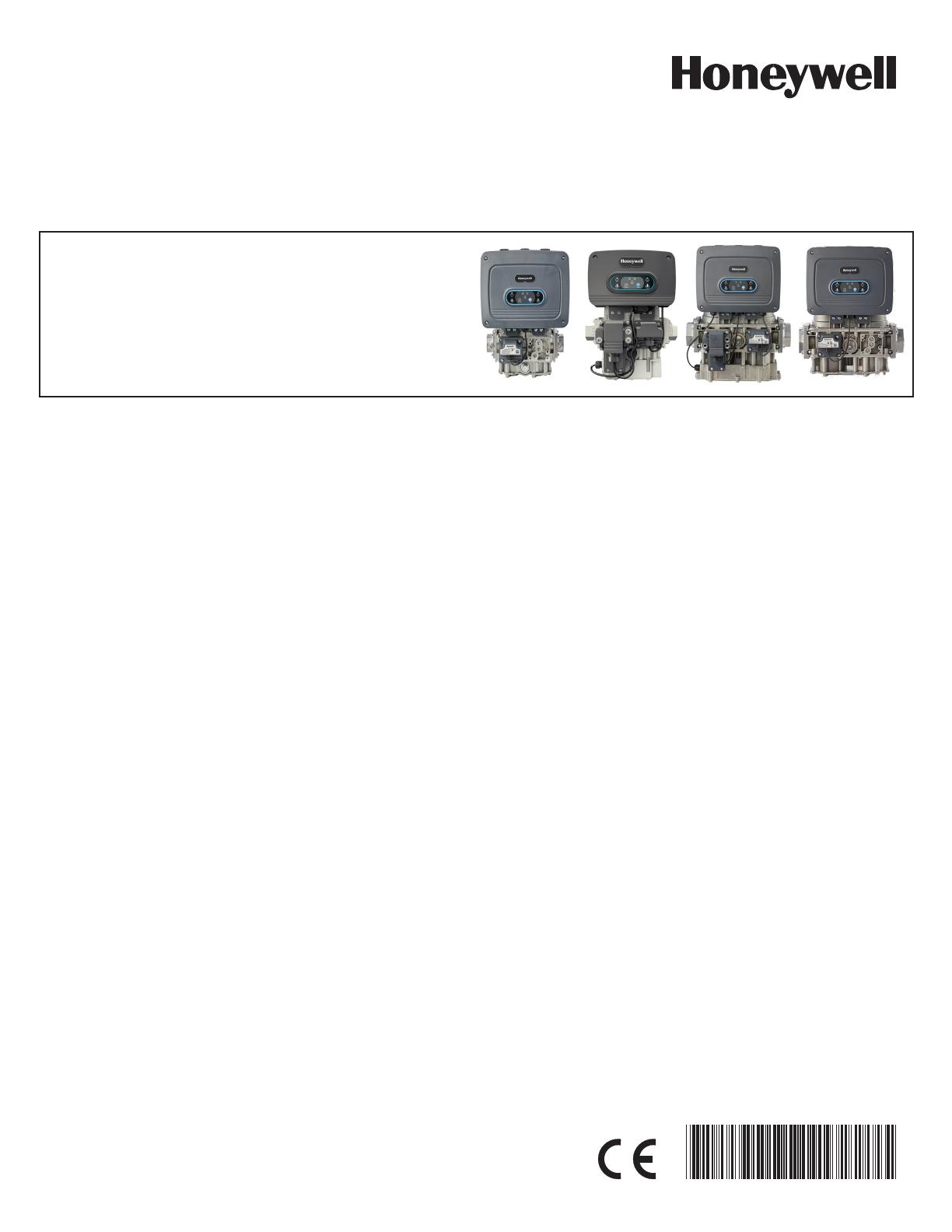
SV2 Series Safety Shut-off Valves
V2F, V2V
USER MANUAL
VALVE AND HMI/PC TOOL SOFTWARE REVISION 12.01 / 12.01.002 OR LATER
CONTENTS
CHAPTER 1 INTRODUCTION .........................................................2
DOCUMENTATION ..................................................................................2
APPLICABLE MODELS / VERSIONS.................................................2
FEATURES ..................................................................................................2
WHEN INSTALLING THIS PRODUCT… .............................................2
CYBER SECURITY NOTICE ................................................................... 2
VALVES ......................................................................................................... 3
ACCESSORIES ........................................................................................... 3
REPLACEMENT PARTS ..........................................................................4
VALVE SPECIFICATIONS .......................................................................4
Environmental Usage Conditions: .....................................................6
VALVE ACCESSORIES AND REPLACEMENT PARTS ...................8
DIMENSIONAL INFORMATION ..........................................................10
VALVE CAPACITY RATINGS ..................................................................12
VALVE CAPACITY CURVES ....................................................................13
GAS VALVE SIZING ...................................................................................19
CHAPTER 2 VALVE FEATURES ......................................................20
Overview ........................................................................................ 20
Power Saving Feature .............................................................. 21
Valve Interface ............................................................................ 21
INSTALLATION OVERVIEW ..................................................................27
Installation Quick Start Guide ............................................. 29
2. MOUNTING OVERVIEW ..................................................... 32
3. WIRING OVERVIEW ............................................................. 35
CHECKOUT AND OPERATION OVERVIEW .....................................41
5. PROGRAMMING AND SETUP OVERVIEW ................. 44
6. FINAL WIRING AND STATIC CHECKOUT OVERVIEW . 44
CHAPTER 3 COMMUNICATION / CONNECTIVITY .................. 46
Introduction ................................................................................. 46
Programming Tools .................................................................. 47
Connectivity Notes ................................................................... 47
Valve Modbus Bias Setup ...................................................... 48
Modbus Addressing ................................................................. 49
CHAPTER 4 ACCESSORIES, FIELD REPLACEMENTS AND
INTELLIGENT FEATURES ...............................................................49
C6097 Pressure Switches ...................................................... 49
Specifications ........................................................ 49
Introduction ............................................................ 50
C6097 Pressure Switch Selection ................. 50
Mounting ................................................................. 51
Programming Tools .................................................................. 51
Specifications ........................................................ 53
Connectivity ............................................................ 54
Safety Features ..................................................... 54
Programming and Setup ................................... 55
Pressure Module........................................................................ 56
Specifications ........................................................ 56
Pressure Module Selection............................... 57
Mounting ................................................................. 58
Theory of Operation ............................................ 59
Low Gas Pressure and High Gas Pressure Operation 60
Valve Proving Sequence (VPS) Operation .. 62
Field Replacement ............................................... 64
Flanges .......................................................................................... 65
Specifications ........................................................ 65
Introduction and Flange Selection ............... 66
Mounting Valve to Flange(s) and Piping .... 66
Replacement Electronics ....................................................... 67
Specifications ........................................................ 67
Introduction and Replacement Assembly Selection 67
Field Replacement ............................................... 68
Replacement Solenoids .......................................................... 69
Specifications ........................................................ 69
Introduction and Replacement Solenoid Selection 69
Field Replacement ............................................... 70
CHAPTER 5 PREMIX TECHNOLOGY ............................................ 71
Fuel/Air Module ......................................................................... 71
Fuel/Air Accessories ................................................................75
Control Possibilities Via Parameter Settings ................ 75
SV2 Series Fuel/Air Valve Theory of Operation ............. 83
CHAPTER 6 ACCESS LEVELS ......................................................... 112
Password Configuration ......................................................... 112
OEM Password Configuration ............................................. 116
Installer Password Configuration ....................................... 118
Access Levels Assignment .................................................... 124
Installer and OEM Password Reset Procedure .............126
CHAPTER 7 VALVE PRODUCTION CLONING ............................ 133
Unconfigured Valve Procedure ........................................... 136
Valve Configuration without Passwords .......................... 137
Valve Configuration with Passwords ................................. 138
Configured Valve Procedure ................................................. 141
CHAPTER 8 FUEL/AIR RATIO MODULE CHANGE-OUT
PROCEDURE .......................................................................................146
FARMOD Replacement Background ................................. 146
Previously Configured/Used FARMOD procedure ...... 150
CHAPTER 9 VALVE MAIN ELECTRONICS CHANGE-OUT
PROCEDURE .......................................................................................154
Valve Main Electronics Replacement Background ..... 154
New Valve Main Electronics Procedure ........................... 154
CHAPTER 10 .......................................................................................158
CHANGING VALVE / ELECTRONICS ORIENTATION ................... 158
Introduction ................................................................................. 158
Electronics Orientation Change Process ........................ 159
LED Orientation Change Process ...................................... 163
Final Wiring Check and Static Checkout ......................... 163
APPENDIX ...........................................................................................164
Burner Control Interface Wiring .......................................... 164
VALVE FAULT CODES .............................................................. 176
TIGHTENING TORQUES ......................................................... 208
MODBUS COMMUNICATION ADDRESSING................. 210