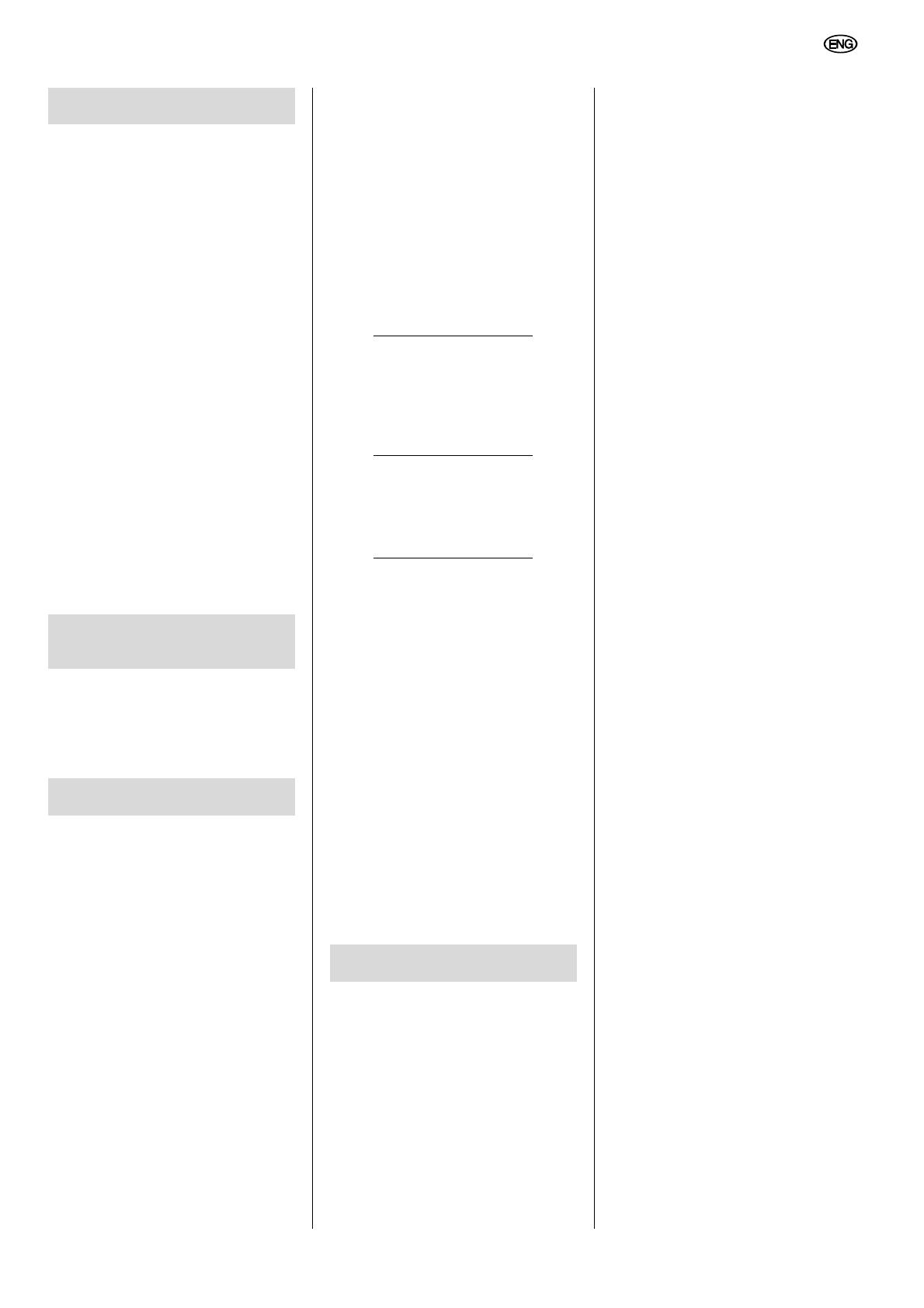
ENGLISH
11
1. Component Overview /
Standard Delivery...................10
2. EC Declaration of
Conformity ..............................11
3. Please Read First! ..................11
4. Safety.......................................11
4.1 Specified conditions of use.......11
4.2 General safety instructions.......11
4.3 Symbols on the machine..........12
4.4 Safety devices..........................13
5. Operation ................................13
5.1 Prior to initial operation.............13
5.2 Installation ................................13
5.3 Mains connection .....................13
5.4 Generating compressed air ......13
6. Care and Maintenance ...........14
6.1 Periodic maintenance...............14
6.2 Machine storage.......................15
7. Troubleshooting.....................15
8. Repairs ....................................15
9. Environmental Protection......15
10. Technical Data........................16
We hereby declare that this machine
complies with the basic requirements
and provisions of the applicable direc
-
tives.
These operating instructions have been
written so that you can quickly learn
how to operate your device safely. Here
is how to read the instructions:
– Read these instructions completely
before use. Pay special attention to
the safety information.
– These instructions are intended for
persons with basic technical knowl
-
edge in the handling of machines
such as the one described here. In
-
experienced persons are strongly
advised to seek competent advice
and guidance from an experienced
person before operating this ma
-
chine.
– Retain all documents delivered to-
gether with this device so that you
and other users have access to the
relevant information at all times. Re-
tain proof of purchase for any future
warranty claims.
– If you lend or sell this device be
sure to have these Operating In
-
structions go with it.
– The manufacturer is not liable for
any damage arising from disregard
of these instructions.
Information in these Operating Instruc-
tions is denoted as follows:
ADanger!
Risk of personal injury or environmental
damage.
BRisk of electric shock!
Risk of personal injury by electric
shock.
A Caution!
Risk of material damage.
3 Note:
Additional information.
– Numbers in illustrations (1, 2, 3
etc.
)
– denote component parts;
– are consecutively numbered;
– relate to the corresponding
number(s) in brackets
(1), (2), (3)
etc. in the neighbouring text.
– Numbered steps must carried out in
sequence.
– Instructions which can be carried
out in any sequence are indicated
by a bullet point (•).
– Listings are preceded by a dash (–).
4.1 Specified conditions of
use
This machine is designed to generate
compressed air required for the opera
-
tion of air tools. The machine should
only be used under supervision.
Any use for medical purposes, food
processing or filling of oxygen cylinders
for breathing equipment is not permit
-
ted.
Gas or dust which is explosive, com-
bustible or detrimental to health may
not be compressed. Operation in explo
-
siver or dusty environments is prohibit-
ed.
Any other use is not as specified. Use
not as specified, alteration of the ma
-
chine or use of parts that are not ap-
proved by the equipment manufacturer
can cause unforeseeable damage!
Children, juveniles and persons not in-
structed in use of this machine are not
permitted to operate the machine or
any air tools connected to it.
4.2 General safety instruc-
tions
When using this electric tool ob-
serve the following safety instruc-
tions to exclude the risk of personal
injury or material damage.
Please also observe the special
safety instructions in the respective
chapters.
Keep all documents supplied with
the machine for future reference.
Observe the statutory accident in-
surance institution guidelines and
regulations for the prevention of ac
-
cidents pertaining to the operation
of air compressors and air tools
where applicable.
Observe the legal regulations re-
garding operation of systems sub-
ject to technical inspections.
When operating and storing the ma-
chine be aware that leaking conden-
sate and operating materials can
contaminate the environment and
lead to environmental damage.
AGeneral hazard!
Keep your work area tidy – a messy
work area invites accidents.
Be alert. Know what you are doing.
Set out to work with reason. Do not
operate the electric tool while under
the influence of drugs, alcohol or
medication.
Consider environmental conditions.
Keep work area well lighted.
Prevent adverse body positions. En-
sure firm footing and keep your bal-
ance at all times.
Do not operate the electric tool near
inflammable liquids or gases.
Keep bystanders, particularly chil-
dren, out of the work area. Do not
permit other persons to touch the
tool or power cable while the elec-
tric tool is running.
Table of Contents
2. EC Declaration of Con-
formity
3. Please Read First!
4. Safety