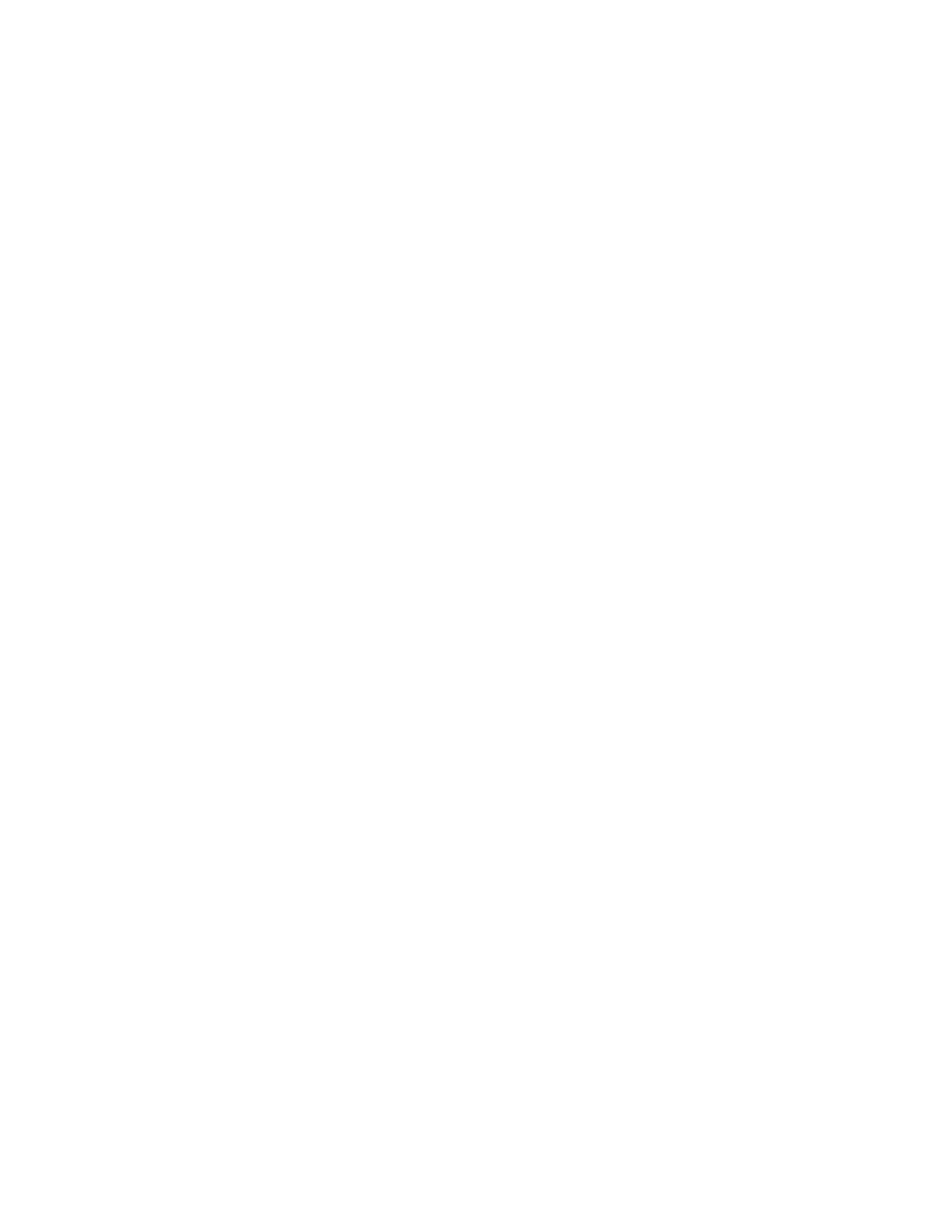
CHAPTER 7. ETHERNET/IP SERVER...................................................................55
7.1. Overview.............................................................................................................55
7.2. Tag Types Supported.........................................................................................56
7.3. 2572-A Configuration .........................................................................................56
7.4. Application Example...........................................................................................56
CHAPTER 8. TROUBLESHOOTING......................................................................61
8.1. Troubleshooting Aids..........................................................................................61
8.2. General Troubleshooting Techniques ...............................................................62
8.3. Module Startup Problems...................................................................................63
8.4. Communications Problems................................................................................65
8.5. Performance Problems.......................................................................................67
8.6. Serial Communications Problems......................................................................68
8.7. PLC Logic Problems...........................................................................................69
8.8. Development and Debugging Tips ....................................................................70
APPENDIX A. 2572-A LED INDICATORS ............................................................73
Module Status and Network Status LED ..................................................................73
Other LEDs................................................................................................................75
APPENDIX B. ERROR CODES .............................................................................77
2572-A System Error Codes.....................................................................................77
General Memory Transfer Error Codes....................................................................79
Server Error Codes....................................................................................................82
PLC Client Error Codes.............................................................................................84
APPENDIX C. PLC COMMAND INTERFACE.......................................................89
General Description...................................................................................................89
WX/WY Description...................................................................................................91
WX/WY Quick Reference..........................................................................................96
Command Timing Diagrams .....................................................................................98
APPENDIX D. IP ADDRESS INFORMATION .....................................................105
IP Address Nomenclature .......................................................................................105
Private IP Addresses...............................................................................................105
Subnet Mask............................................................................................................106
Port Number.............................................................................................................107
APPENDIX E. USING DHCP.................................................................................109
DHCP Overview.......................................................................................................109
Configuring a DHCP Server....................................................................................110
APPENDIX F. UPDATING FIRMWARE................................................................113
Overview..................................................................................................................113
Update Preparation .................................................................................................113
Updating 2572-A Firmware .....................................................................................114
Firmware Update Process.......................................................................................115
Troubleshooting Firmware Update Problems.........................................................116
HARDWARE SPECIFICATIONS ..........................................................................119
LIMITED PRODUCT WARRANTY........................................................................120
REPAIR POLICY....................................................................................................121