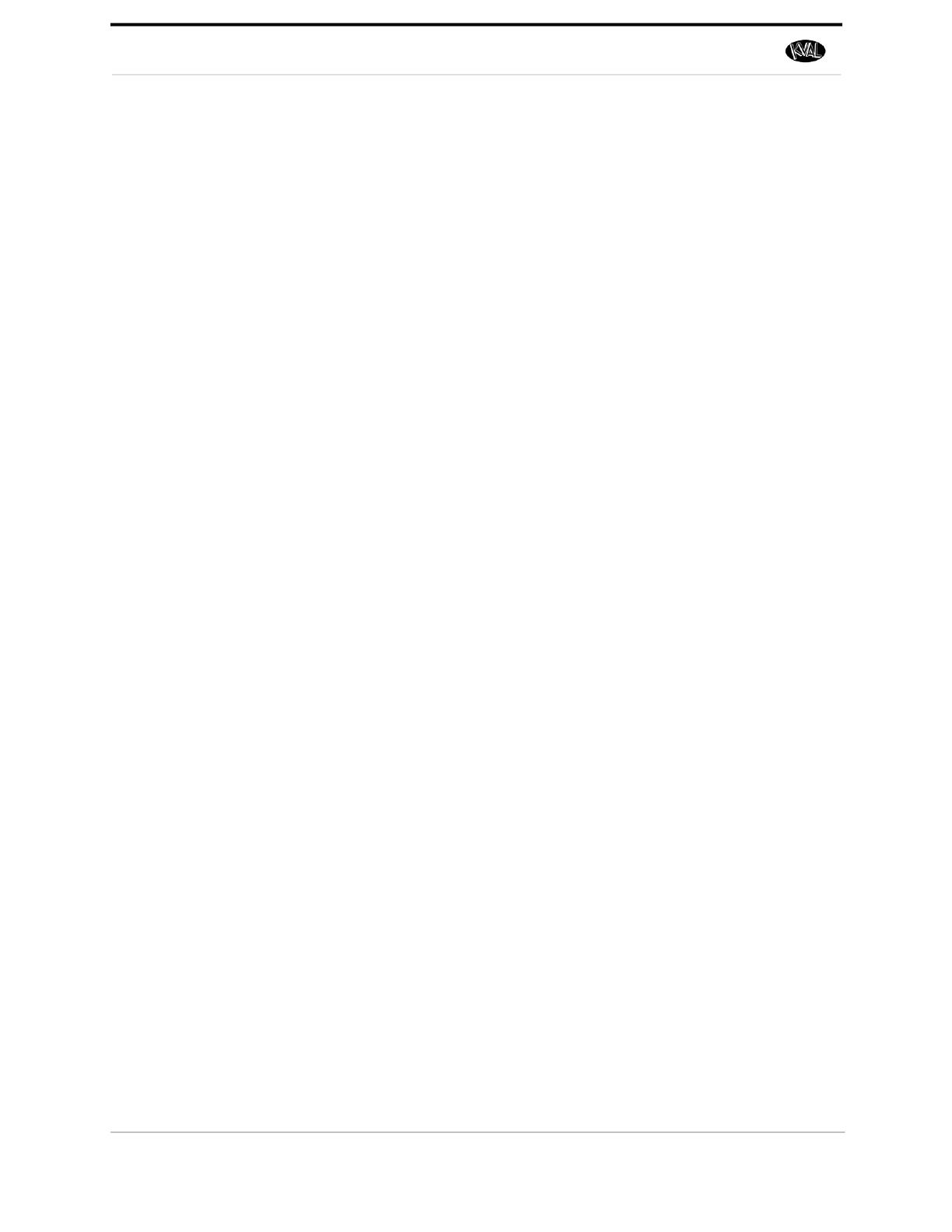
Table of Contents
700-C Operation and Service Manual
Proprietary Notice.................................................................................1-2
Contacting KVAL...................................................................................1-2
Kval Website.........................................................................................1-3
CHAPTER 1 .................................................................................Introduction 1-1
Safety First!.............................................................................. 1-2
Lockout and Tagout Guidelines ............................................... 1-4
Follow the P-R-O-P-E-R lockout rule of thumb. ...................................1-4
Zero-Energy State to Start-Up to Operating State................... 1-5
Lockout Tagout Procedure....................................................... 1-7
Pre-Steps Before Lockout Tagout.........................................................1-7
Lockout Tagout Power ..........................................................................1-7
Lockout Tagout Air Supply ....................................................................1-8
Start Maintenance.................................................................................1-8
Post Maintenance Steps.......................................................................1-8
Safety Sign-Off Sheet .............................................................. 1-10
A Note to the Operator........................................................................1-10
Initial Set up ............................................................................. 1-11
CHAPTER 2 .................................................................................... Operation 2-2
Machine Tour ........................................................................... 2-3
About the 24 VDC Electrical Box..........................................................2-4
Quick Start ............................................................................... 2-5
Load the Door into the Machine............................................................2-5
Getting the Door Ready to Process......................................................2-6
Summary of Hand Control Presses......................................2-7
Firing Staple Guns and Nailer..............................................2-7
End Process.........................................................................2-7
Turning the 700-C On and Off ................................................. 2-11
Powering Up the 700-C ......................................................................2-11
Powering Down the 700-C..................................................................2-11
Main Control Panel .................................................................. 2-12
Width Adjust............................................................................. 2-13
Length Adjust (Option D) ......................................................... 2-15
About the Touch Screen Interface ........................................... 2-16
Screen Paths ......................................................................................2-16
About the Main Screen .......................................................................2-17