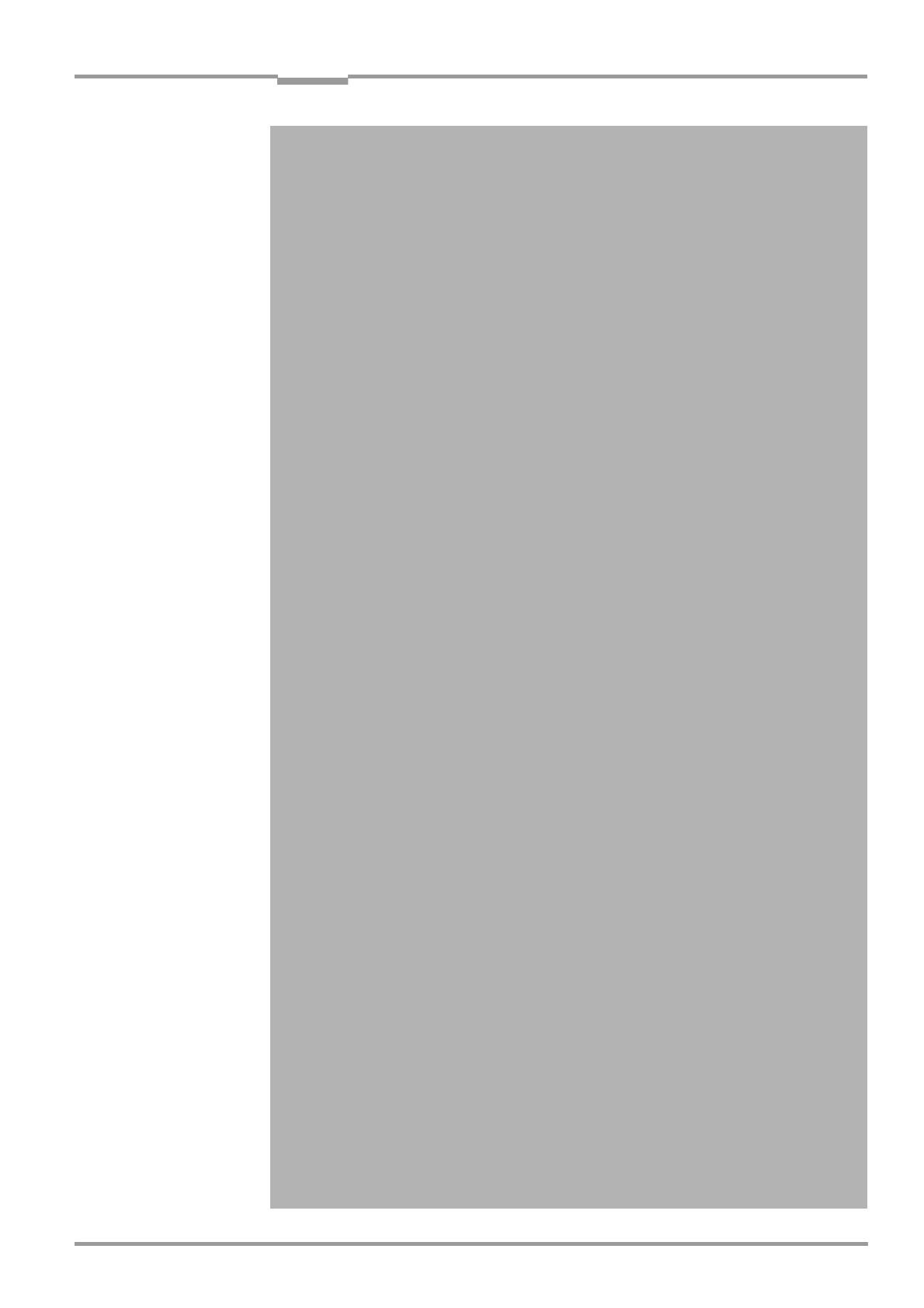
Operating Instructions
MUX400 Multiplexer
Contents
8010685/TE89/2009-08-17 © SICK AG · Division Auto Ident · Germany · All rights reserved 3
Table of Contents
1 Notes on this document ................................................................................................9
1.1 Purpose....................................................................................................................... 9
1.2 Target audience ......................................................................................................... 9
1.3 Information content ................................................................................................... 9
1.4 Symbols used............................................................................................................. 9
2 Safety information ...................................................................................................... 11
2.1 Authorized users ...................................................................................................... 11
2.2 Intended use ............................................................................................................11
2.3 General safety instructions and protection measures.......................................... 12
2.4 Quick stop and quick restart ...................................................................................12
2.5 Environmental information...................................................................................... 12
3 Product description..................................................................................................... 14
3.1 Design.......................................................................................................................14
3.2 Method of operation ................................................................................................17
3.3 Indicators and operating elements.........................................................................21
4 Installation ...................................................................................................................22
4.1 Selecting the installation site.................................................................................. 22
4.2 Installing the MUX400............................................................................................. 22
4.3 Removing the device ............................................................................................... 22
5 Electrical installation .................................................................................................. 23
5.1 Overview of the connection sequence ................................................................... 23
5.2 Electrical connections and cables .......................................................................... 23
5.3 Connector pin and terminal strips assignment ..................................................... 24
5.4 Planning the electrical installation ......................................................................... 26
5.5 Making electrical connections ............................................................................... 28
6 Startup and configuration.......................................................................................... 36
6.1 Overview of the starting up sequence.................................................................... 36
6.2 Default setting..........................................................................................................36
6.3 Operating modes/functions .................................................................................... 37
6.4 Configuration (parameterizing) ............................................................................... 38
6.5 Further operation steps...........................................................................................51
6.6 MUX400 messages.................................................................................................. 51
6.7 Switching off the MUX400....................................................................................... 52
7 Maintencance .............................................................................................................. 53
7.1 Maintenance during operation ............................................................................... 53
7.2 Cleaning external components ............................................................................... 53
7.3 Replacing a MUX400 (copying the parameter set) ..............................................53
8 Troubleshooting........................................................................................................... 55
8.1 Overview of the possible errors and malfunctions ................................................ 55
8.2 Monitoring error and malfunctions......................................................................... 55
8.3 Error messages ........................................................................................................55
8.4 Troubleshooting .......................................................................................................55
8.5 Querying error codes with command strings ......................................................... 58
8.6 SICK Support............................................................................................................ 60
9 Technical Data............................................................................................................. 61
9.1 Data sheet MUX400 Multiplexer ............................................................................61
9.2 Dimensional drawing ...............................................................................................62
10 Appendix....................................................................................................................... 63
10.1 Overview ...................................................................................................................63
10.2 Installation and operation of the PC-based "CLV Setup" program .......................64
10.3 Configuring the MUX400 with command strings.................................................. 74
10.4 Accessories ..............................................................................................................76
10.5 Supplementary documentation ..............................................................................76
10.6 Code table (Hex – ASCII) .........................................................................................77
10.7 Copy of the EC Declaration of Conformity..............................................................78