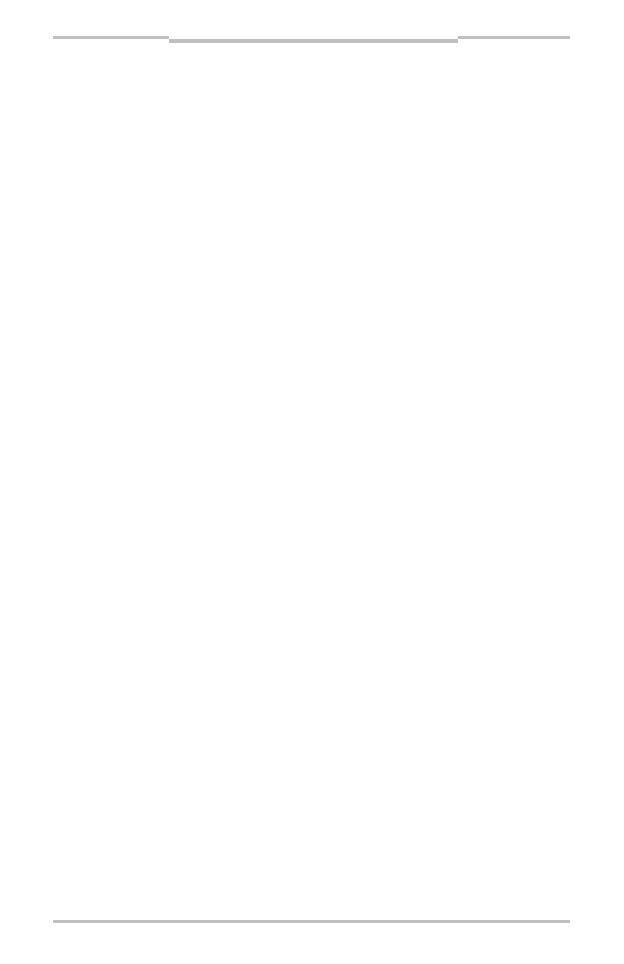
O
perating Instructions Chapter
2
T4000 Direct Unicode
© SICK AG • Industrial Safety Systems • Germany • Subject to change without notice • 8012206/UC32/2010-11-15
145
On safety
For the control this means that
switch-on commands that produce dangerous states
are only allowed to become effective when the guards
are in the protective position,
and
dangerous states must be terminated before the
protective position is left.
Prior to the use of the safety switches, a risk assessment
must be performed on the machine as per:
EN ISO 14121, Safety of machinery, principles of risk
assessment
EN ISO 13849-1 Safety-related parts of control systems
EN 12100, Safety of machinery, basic concepts
EN 62061, Safety of machinery, functional safety of
safety-related electrical, electronic and programmable
electronic control systems.
Correct use includes observance of the applicable
requirements on installation and operation, in particular
EN 1088, Safety of Machinery. Interlocking devices
associated with guards. Principle for design and
selection,
EN 999
1)
, Safety of machinery – The positioning of
protective equipment in respect of approach speeds of
parts of the human body,
EN 60204J1, Electrical equipment of machines
EN 60 947J5-3, Specification for low-voltage switchgear
and controlgear – Control circuit devices and switching
elements,
EN 60 947J5-1, Specification for low voltage switch
gear and control gear; Control circuit devices and
switching elements. Electromechanical control circuit
devices,
EN 61 000J6-2, Electromagnetic compatibility (EMC).
Generic standards. Immunity standard for industrial
environments.
The safety switches must be regularly subjected to a
technical inspection as per section 2.4 “General safety
notes and protective measures”.
1)
EN 999 will be replaced by EN ISO 13855 in future. The basic formula for the calculation
will not change.