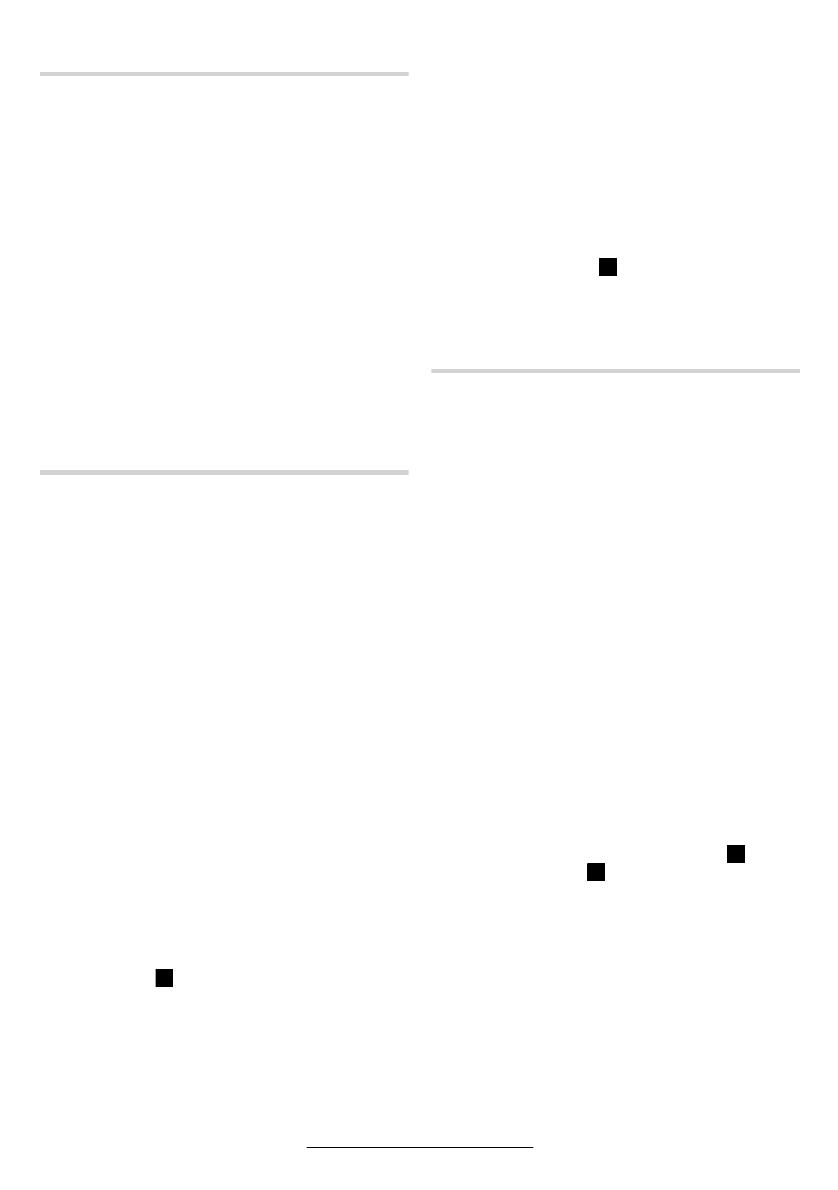
English–6
3 609 929 935 • (03.10) T
4 MOUNTING
Suspension and clamping device
If you wish to operate the tool in a suspension or
clamping device, make sure that the tool is first
mounted in the device before you connect it to
the air supply. In this way you avoid starting the tool
accidentally.
You can use the hanging hoop 33 (Type 0 607 161 1..)
or 2 (Type 0 607 161 5..) to attach the tool to a sus-
pension device.
Regularly check the condition of the hanging hoop and
the hook of the suspension device.
You can use the clamping area 10 to mount the tool in
a clamping device. If possible, use the entire clamping
area. The smaller the clamping area, the stronger the
clamping force.
Do not overstrain the clamping area and make sure
that the clamping device holds the tool securely and
tightly.
Exhaust Line
You can use an exhaust line to carry exhaust air away
from your workplace and, at the same time, achieve
optimal muffling. You also improve the operating con-
ditions, because your workplace will no longer be con-
taminated by oil-containing air and there are no longer
any raised dust or chips.
Type 0 607 161 100 – … 103
Slip the exhaust hose (combined) 28, which carries the
exhaust air away from your workplace, over the air inlet
hose 5. Then connect the tool to the air supply (see
section Connection to the Air Supply) and pull the ex-
haust hose (combined) 28 over the mounted air inlet
hose to the end of the tool.
Alternatively, direct the exhaust air into an exhaust
tank by first attaching the exhaust assembly (separate)
31. Make sure that the hose nipple 4 is not screwed
into the connector at the air inlet 3 and that the O-ring
32 lies in the recess between the housing and the ex-
haust assembly, so that the exhaust air can only es-
cape to the exhaust hose. Tightly screw first the con-
nector 30 of the exhaust assembly into the connector
3 at the air inlet and then the hose nipple 4 into the
connector 30. Replace the muffler 29 on the exhaust
assembly with the hose nipple 24 of the exhaust as-
sembly (see Fig. ).
Loosen the hose clamp 6 of the exhaust hose 25 and
attach the exhaust hose over the hose nipple 24 by
firmly tightening the hose clamp.
Type 0 607 161 500 – … 507
Slip the exhaust hose (combined) for the pistol design
7, which carries the exhaust air away from your work-
place, over the air inlet hose 5. Then connect the tool
to the air supply (see section Connection to the Air
Supply) and pull the exhaust hose (combined) for the
pistol design 7 over the mounted air inlet hose to the
end of the tool.
Alternatively, conduct the exhaust air into an exhaust
tank by replacing the muffler on the air outlet 8 with the
hose nipple 24 (see Fig. ).
Loosen the hose clamp 6 of the exhaust hose 25 and
attach the exhaust hose over the hose nipple 24 by
firmly tightening the hose clamp.
Connection to the Air Supply
The air tool is designed for an operating pressure of
6.3 bar (91 psi). For maximum performance, the inner
diameter of the hose is 10 mm with connection
threads of G 1/4". To maintain full performance, use
only hoses with a maximum length of 4 m.
The supplied air must be free of foreign material and
moisture to protect the air tool from damage, contam-
ination, and rust.
The use of a compressed air maintenance unit is
necessary.
This ensures optimum functioning of compressed air
tools. Observe the operating instructions of the main-
tenance unit.
All fittings, connecting lines, and hoses must be di-
mensioned for the required air pressure and volume.
Avoid restrictions in the air supply resulting from, e.g.,
pinching, kinking, or stretching!
In case of doubt, measure the pressure with a pres-
sure gauge at the air inlet with the tool switched on.
Connection of the Air Supply to the Air Tool
Screw the hose nipple 4 into the connector at the air
inlet 3 (Type 0 607 161 1.. see Fig. , Type
0 607 161 5.. see Fig. ).
To prevent damage to the internal valve components
of the tool, you should use an open end wrench
(22 mm) to apply a counterforce at the protruding con-
nector of the air inlet 3 when screwing/unscrewing the
hose nipple 4.
Loosen the hose clamps 6 of the air inlet hose 5 with
a maximum length of 4 m and attach the air inlet hose
over the hose nipple 4 by firmly tightening the hose
clamp.
B
D
A
C