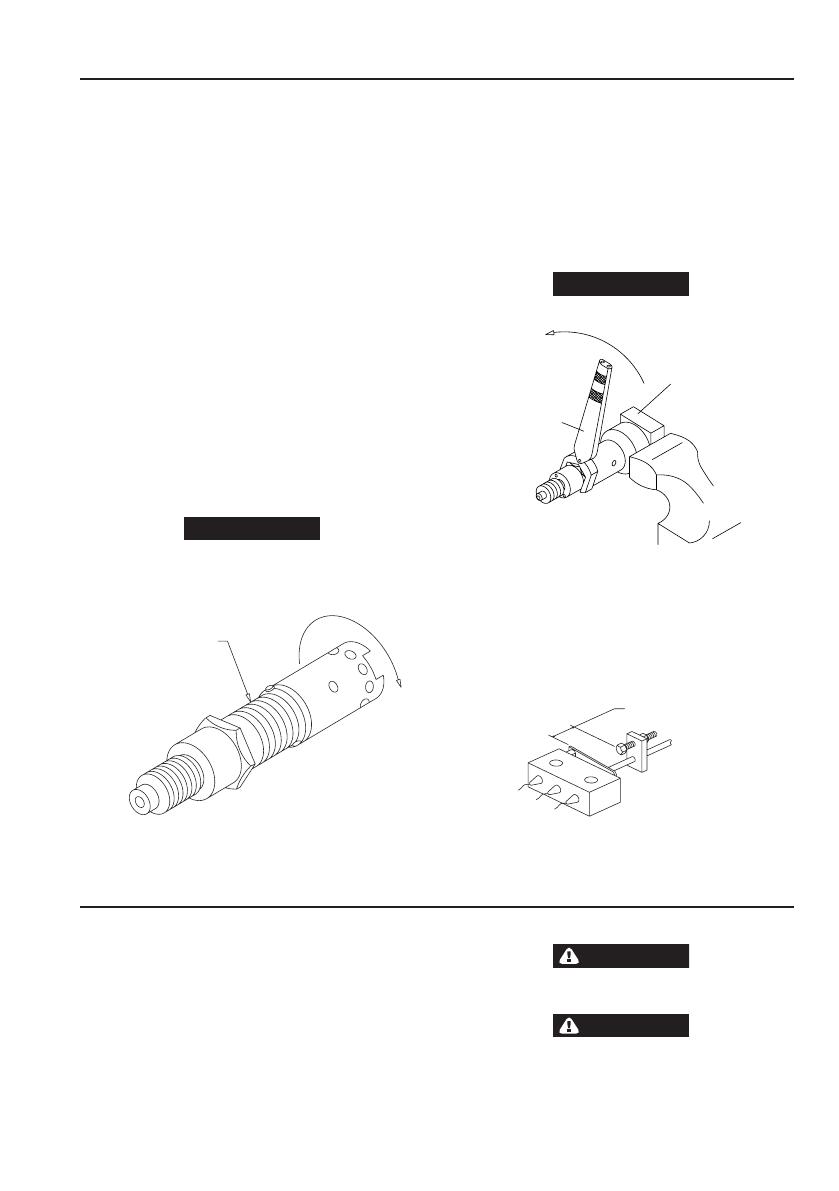
45527785_ed1 5
Assembly
To assemble these tools, reverse the disassembly procedure.
There are certain assembly and lubrication instructions which are
important for optimum performance and they are as follows:
Keep the commutator surface of the armature free from all
contaminants.
Use good quality, properly sized snap ring pliers when installing
the Stop Ring (32E or 33E) on the Bit Holder (31A or 32A) and
do not expand the Stop Ring more than required to install it on
the Holder. Excessive expansion may cause the Ring to deform
and fail.
To assemble the Clutch Housing Assembly to the Gear Case
Assembly, proceed as follows:
Apply 0.3 cc of Ingersoll Rand No. 67 Grease to the Spindle
Assembly (24 or 25).
Insert the Cam (25, 26A or 27), small end rst, into the Gear
Case (21 or 22).
Inject a small amount of grease into the holes for the Cam
Guide Balls (28C or 29B) and insert a Cam Guide Ball into each
hole.
For model ES5OP, insert a Cam Pin (26B or 27B) between each
of the two Cam Guide Balls and hold each in position with a
small amount of grease.
For Model ES1OOP or ES1OOT, insert a Cam Pin between
each of the four Cam Guide Balls and hold each in position
with a small amount of grease.
Being careful not to dislodge the Cam Guide Balls or Cam
Guide Pins, thread the Gear Case onto the Clutch Housing
about two threads.
This is a left-hand thread.
e. At the middle of the Clutch Housing thread, apply Loctite
Threadlocker 242, or equivalent, to approximately three
threads.
(Dwg. TPD1044)
f. Carefully thread the Clutch Housing into the Gear Case until
contact is made with the Cam. When contact is made, unscrew
the Clutch Housing two full thread revolutions.
1.
2.
3.
a.
b.
c.
d.
g. Insert a 114” tee wrench or hex wrench into the end of the Bit
Holder (31A or 32A). While pushing the Bit Holder inward with
the wrench, rotate the Gear Case until the jaws of the Cam
Guide (28B or 29A) engage the Cam. The wrench will move
inward noticeably when engagement occurs.
h. While maintaining engagement with the wrench, hand
tighten the Gear Case as much as possible.
i. With the assembly xture held in vise jaws, position the
notches in the Gear Case onto the xture and, using a torque
wrench, tighten the Clutch Housing to 21 ft-lb (28.5 Nm)
torque. Refer to Drawing TPD1053 on Page 3.
Recalibrate the torque wrench every six months.
orque Wrench
Assembly Fixture
(Dwg. TPD1045)
4. The brake switch must be timed to actuate when the clutch cams
over. To adjust the timing, loosen the Adjusting Screw Nut (13B or
14B) and turn the Adjusting Screw (13A or 14A) in or out until the
microswitch (12A or 13A) is actuated at the same time the clutch
cams over or slightly before it cams over, If the motor lug before
the brake switch actuates, shorten the Adjusting Screw.
Clutch Shut-o/Brake Switch
(Dwg. TPD1046)
Lubrication
Whenever an Electric Screwdriver is disassembled for maintenance
or repair, lubricate the following components in the recommended
manner with Ingersoll Rand No. 67 Grease.
Inject a tiny amount of grease into the hole in the Pilot (31B or
32B) for the Pilot Ball (31C or 32C).
Wipe a lm of grease on the tapered inner surface of the Slide
Ring (32A or 33A) and the Taper Ring Assembly (29 or 30).
Apply a moderate amount of grease to the outer surfaces of the
Cam (25, 26A or 27), the Cam Guide (28B or 29A) and the Cam
Guide Balls (28C or 29B).
Wipe a thin coat of grease on each of the Spindle Gears (24A or
25A).
1.
2.
3.
4.
Do not pack the gearing with grease. Excess grease may be
pulled into the motor by the Armature Fan (18 or 19).
Pilot Rod “G” (20 or 21) must be totally free of grease. Grease on
this Rod could cause electric shock.