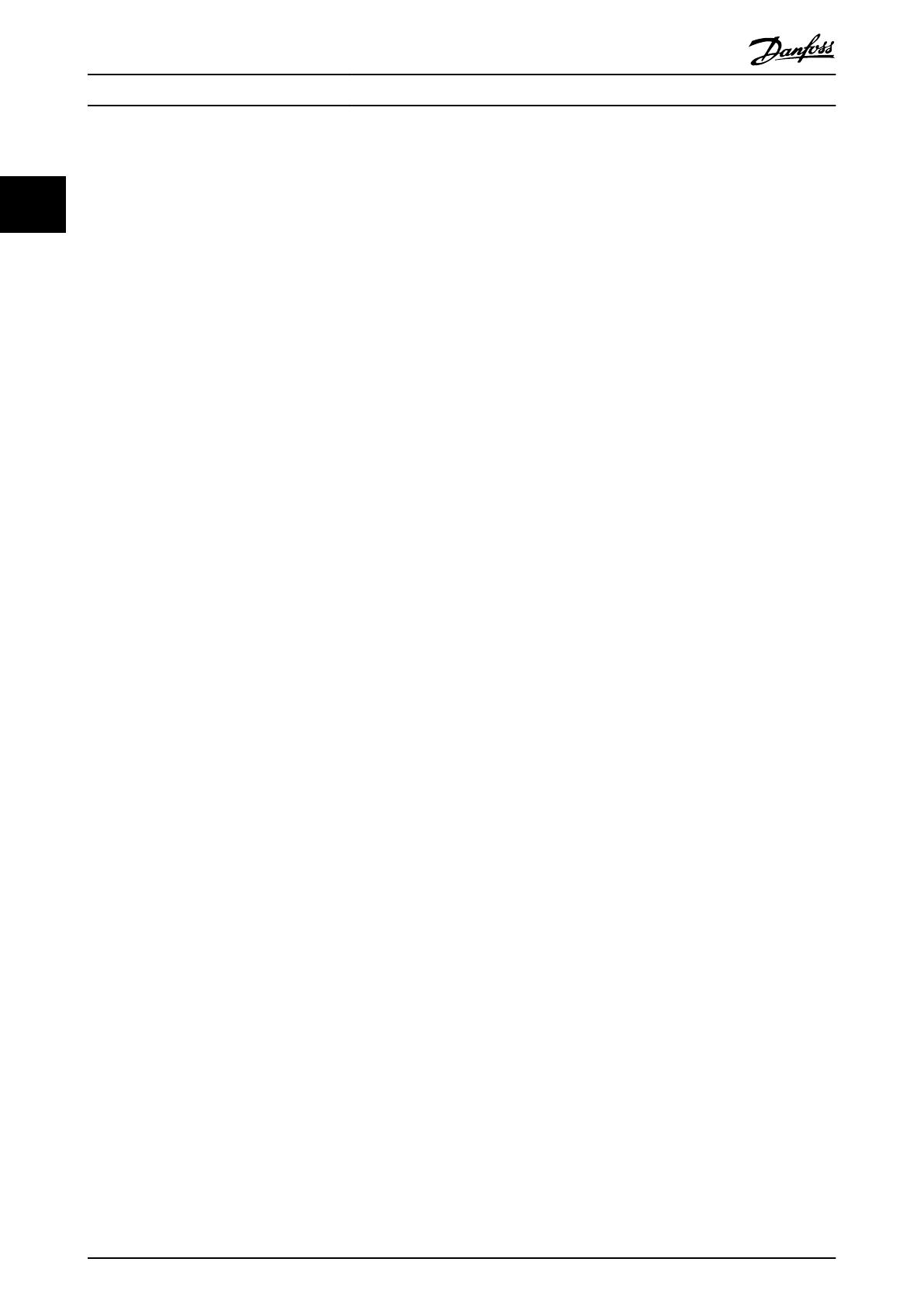
2 Introduction
2.1 About this Manual
First time users can obtain the most essential information
for quick installation and set-up in these chapters:
•
Chapter 2 Introduction
•
Chapter 3 How to Install
•
Chapter 5 How to Configure the System
For more detailed information including the full range of
set-up options and diagnosis tools, refer to the chapters:
•
Chapter 5 How to Configure the System
•
Chapter 6 How to Control the Frequency Converter
•
Chapter 8 Parameters
•
Chapter 10 Troubleshooting
Terminology
In this manual several terms for Ethernet are used.
•
PROFINET, is the term used to describe the
PROFINET protocol.
•
Ethernet, is a common term used to describe the
physical layer of the network and does not relate
to the application protocol.
2.2
Technical Overview
Since the introduction in 2001, PROFINET has been
updated to handle low and medium performance
requirement supported by PROFINET RT (Real Time) up to
High end servo performance in PROFINET IRT (Isochronous
Real Time). With this, PROFINET is the Ethernet Based
Fieldbus offering the most scalable and versatile
technology today.
PROFINET provides users with the network tools to deploy
standard Ethernet technology for manufacturing
applications while enabling Internet and enterprise
connectivity.
2.3
Assumptions
These operating instructions are under the conditions that
the Danfoss PROFINET option is used with a Danfoss FC
102/FC 202/FC 301/FC 302/FCD 302 frequency converter. It
is also assumed that the installed controller supports the
interfaces described in this document and that all the
requirements stipulated in the controller, as well as the
frequency converter, are strictly observed along with all
limitations herein.
2.4
Hardware
This manual relates to the PROFINET option MCA 120, type
no. 130B1135 (uncoated) and 130B1235 (conformal
coated).
2.5 Background Knowledge
The Danfoss PROFINET Option Card is designed to
communicate with any system complying with the
PROFINET schema version 2.2 and 2.3 standards. For earlier
versions of PROFINET, which support schema version 2.1
and earlier, Danfoss recommends an upgrade of the
master and other devices connected to the PROFINET
network to schema version 2.2 and version 2.3. Familiarity
with this technology is assumed. Issues regarding hardware
or software produced by other manufacturers, including
commissioning tools, are beyond the scope of this manual,
and are not the responsibility of Danfoss.
For information regarding commissioning tools, or
communication to a non-Danfoss node, consult the
appropriate manuals.
2.6 Available Literature
Available Literature for FC 102/FC 202/FC 301/FC
302/FCD 302
•
The Operating Instructions, provides the necessary
information for getting the central frequency
converter up and running.
•
The FCD 302 Operating Instructions, provides the
necessary information for getting the de-central
frequency converter up and running.
•
The Design Guide, includes all technical
information about the central frequency
converter design and applications including
encoder, resolver, and relay options.
•
The FCD 302 Design Guide, includes all technical
information about the de-central frequency
converter design and applications including
encoder, resolver, and relay options.
•
The VLT
®
AutomationDrive Profibus Operating
Instructions provides the information required for
controlling, monitoring, and programming the
frequency converter via a Profibus fieldbus.
•
The VLT
®
AutomationDrive DeviceNet Operating
Instructions provides the information required for
controlling, monitoring, and programming the
frequency converter via a DeviceNet fieldbus.
•
The VLT
®
AutomationDrive MCT 10 Set-up Software
Operating Instructions, provides information for
Introduction
Operating Instructions
6 Danfoss A/S © Rev. 2014-02-27 All rights reserved. MG90U302
22