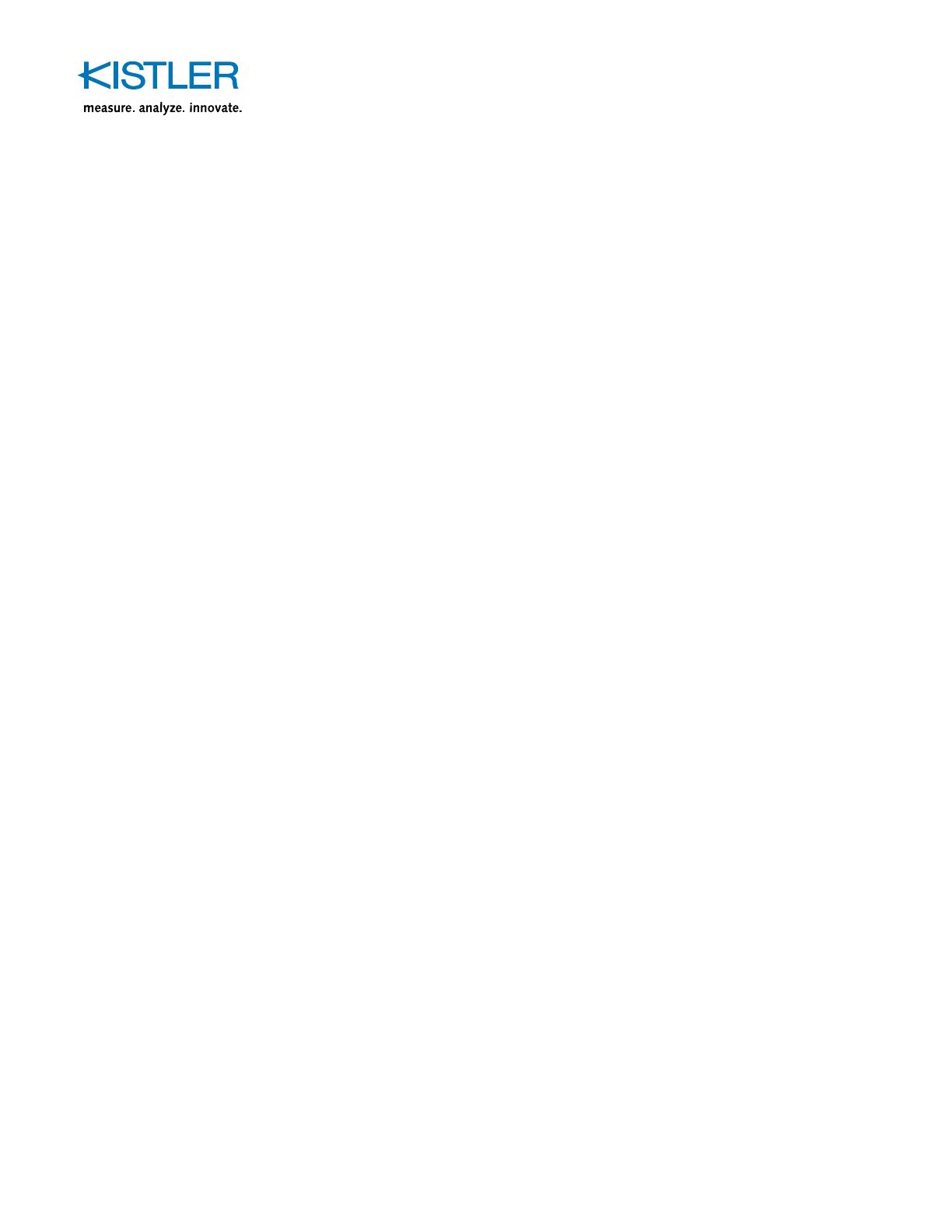
002-086e-11.21Page 2
Single-Axis K-Shear and PiezoStar Accelerometers
Content
1. Introduction .......................................................................................................................................4
2. Important information ......................................................................................................................5
2.1 For your safety .......................................................................................................................5
2.2 Precautions ............................................................................................................................6
2.3 Disposal of electronic equipment ...........................................................................................6
2.4 Nomenclature .........................................................................................................................7
3. Product description ..........................................................................................................................8
3.1 Piezoelectric measurement concept ......................................................................................8
3.2 K-Shear background ..............................................................................................................9
3.3 PiezoStar background ..........................................................................................................10
3.4 Low impedance (IEPE) output..............................................................................................10
3.5 Accessories ..........................................................................................................................11
3.5.1 Studs .......................................................................................................................12
3.5.2 Adhesive mounting pads .........................................................................................13
3.5.3 Magnetic mounting bases .......................................................................................13
3.5.4 Triaxial mounting cubes ..........................................................................................14
3.5.5 Cables .....................................................................................................................15
4. Installation.......................................................................................................................................16
4.1 Surface preparation ..............................................................................................................16
4.2 Stud mounting ......................................................................................................................17
4.3 Direct adhesive mounting .....................................................................................................18
4.4 Mounting with wax ................................................................................................................19
4.5 Mounting with magnet ..........................................................................................................20
4.6 Summary of mounting methods ...........................................................................................21
4.7 Securing cables ....................................................................................................................22
4.8 Mass loading effects .............................................................................................................23
5. Operating instructions ...................................................................................................................24
5.1 Powering ..............................................................................................................................24
5.1.1 Using "Built-In" power sources................................................................................24
5.1.2 Kistler couplers .......................................................................................................25
5.1.3 The constant current power supply/coupler ............................................................25
5.1.4 Sensor power-up ....................................................................................................28
5.1.5 Overload recovery ..................................................................................................28
5.1.6 Supply voltage effects .............................................................................................29
5.1.7 Driving long cables .................................................................................................29