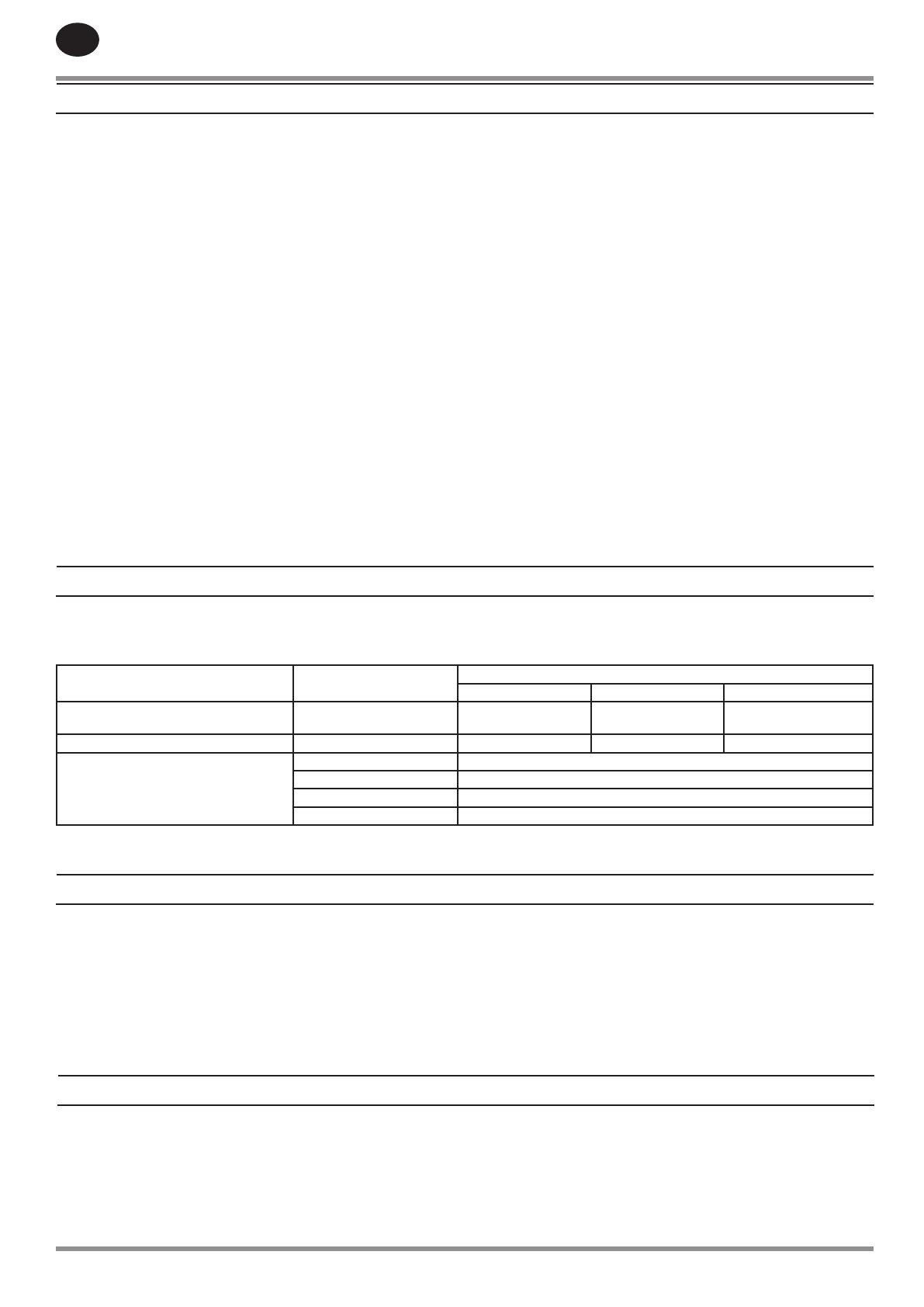
ES
80446354 Rev D ES-2
ACERCA DE ESTE MANUAL . . . . . . . . . . . . . . . . . . . . . . . . . . . . . . . . . .2
PERSONAL . . . . . . . . . . . . . . . . . . . . . . . . . . . . . . . . . . . . . . . . . . . . . . . . .2
SEGURIDAD . . . . . . . . . . . . . . . . . . . . . . . . . . . . . . . . . . . . . . . . . . . . . . . .2
MANTENIMIENTO DEL COMPRESOR DE AIRE. . . . . . . . . . . . . . . . .3
Mensajes de Mantenimiento. . . . . . . . . . . . . . . . . . . . . . . . . . . . . . . .3
Tabla de Mantenimiento . . . . . . . . . . . . . . . . . . . . . . . . . . . . . . . . . .3
Mantenimiento Periódico . . . . . . . . . . . . . . . . . . . . . . . . . . . . . . . . . .4
Vericando el nivel de refrigerante . . . . . . . . . . . . . . . . . . . . . . . . . . . . . 4
Añadir refrigerante. . . . . . . . . . . . . . . . . . . . . . . . . . . . . . . . . . . . . . . . . . . . 4
Drenado de refrigerante . . . . . . . . . . . . . . . . . . . . . . . . . . . . . . . . . . . . . . . 4
Analizando el refrigerante de grado alimentario . . . . . . . . . . . . . . . . 4
Muestras de refrigerante. . . . . . . . . . . . . . . . . . . . . . . . . . . . . . . . . . . . . . . 4
Cambio del ltro del refrigerante. . . . . . . . . . . . . . . . . . . . . . . . . . . . . . . 5
Controlar el elemento del separador. . . . . . . . . . . . . . . . . . . . . . . . . . . . 5
Cambio del elemento separador. . . . . . . . . . . . . . . . . . . . . . . . . . . . . . . . 5
Inspección del tanque del separador / sistema de presión . . . . . . . . 5
Limpieza / control de la pantalla de purga. . . . . . . . . . . . . . . . . . . . . . . 6
Cambio de manguitos del refrigerante. . . . . . . . . . . . . . . . . . . . . . . . . . 6
Vericación de la válvula de control de la presión mínima (MPCV) 6
Cambio del ltro de aire . . . . . . . . . . . . . . . . . . . . . . . . . . . . . . . . . . . . . . . 6
Reengrasado del motor. . . . . . . . . . . . . . . . . . . . . . . . . . . . . . . . . . . . . . . . 6
Limpieza del sistema de refrigeración secuencial de aire . . . . . . . . . 6
Retirar/instalar el refrigerante de aire. . . . . . . . . . . . . . . . . . . . . . . . . . . 6
Limpieza del refrigerador de agua (para versiones de agua limpia y
dura) . . . . . . . . . . . . . . . . . . . . . . . . . . . . . . . . . . . . . . . . . . . . . . . . . . . . . . . . . 7
Control del sensor de temperatura del extremo del compresor alto 7
Limpieza del capó del motor . . . . . . . . . . . . . . . . . . . . . . . . . . . . . . . . . . . 7
Retirar / sustituir el módulo de conducción de la caja de arranque
(PDM) elemento de ltro (solo para VSD) . . . . . . . . . . . . . . . . . . . . . . . 7
Limpieza/control del drenaje de condensado. . . . . . . . . . . . . . . . . . . . 8
Limpieza/instalación del preltro del paquete .. . . . . . . . . . . . . . . . . . 8
Vericación/limpieza de la trampilla de drenaje sin pérdida (si hay)
. . . . . . . . . . . . . . . . . . . . . . . . . . . . . . . . . . . . . . . . . . . . . . . . . . . . . . . . . . . . . . 8
Control del análisis de uido y cojinetes de “Shock Pulse” . . . . . . . . 8
RESOLUCIÓN DE PROBLEMAS . . . . . . . . . . . . . . . . . . . . . . . . . . . . . . .9
R3775 MANTENIMIENTO DEL SECADOR INTEGRADO . . . . . . 14
Tabla de Mantenimiento . . . . . . . . . . . . . . . . . . . . . . . . . . . . . . . . 14
Limpieza de los drenajes de condensado (solo drenajes
planicados) . . . . . . . . . . . . . . . . . . . . . . . . . . . . . . . . . . . . . . . . . . . . . . . . . 14
Prueba de drenajes de condensado (sólo drenajes sin pérdida) . . 14
Resolución de problemas Drenajes de condensado (sólo drenajes
electrónicos). . . . . . . . . . . . . . . . . . . . . . . . . . . . . . . . . . . . . . . . . . 14
Desmonte el secador integrado . . . . . . . . . . . . . . . . . . . . . . . . . . . 14
Retirada del servicio del secador integrado . . . . . . . . . . . . . . . . . . 14
CONTENIDO
ACERCA DE ESTE MANUAL
PERSONAL
SEGURIDAD
El uso, inspecciones y mantenimiento adecuados aumentan la vida y la
utilidad del compresor. Es extremadamente importante que todos los
involucrados en el mantenimiento del compresor estén familiarizados con
los procedimientos de mantenimiento y reparaciones de estos compresores
y que sean físicamente capaces de realizar los procedimientos. Este personal
debe ser capaz de realizar lo siguiente:
1. Manejo seguro y adecuado de herramientas mecánicas comunes,
así como de herramientas especiales o recomendadas por
Ingersoll Rand.
2. Procedimientos de seguridad, precauciones y hábitos de trabajo
establecidos por normas industriales aceptadas.
Algunos procedimientos de mantenimiento son técnicos en su naturaleza
y exigen herramientas especiales, maquinaria, formación y experiencia
para ser realizados correctamente. En dichas situaciones, sólo permita
que técnicos formados de Ingersoll Rand realicen el mantenimiento del
compresor. El personal operativo no debe intentar llevar a cabo el servicio o
las inspecciones más allá de los procedimientos indicados en este manual.
Para más información, póngase en contacto con la planta de Ingersoll Rand
o el técnico más cercano.
Antes de realizar cualquier trabajo en el compresor, asegúrese de haber
aíslado, bloqueado y marcado la alimentación eléctrica y de que el compresor
haya sido liberado de toda presión. Asegúrese de que el compresor está
aislado eléctricamente durante al menos 15 minutos antes de comenzar todo
trabajo de mantenimiento. Consulte el manual de información de seguridad
del producto para más información.
Ingersoll Rand no puede saber ni facilitar todos los procedimientos con
los que realizar las reparaciones ni los riesgos/resultados de cada método.
Si se realizan procedimientos de mantenimiento no recomendados
concretamente por el fabricante, asegúrese de que las acciones realizadas no
pongan en peligro la seguridad.
Si no está seguro del procedimiento o pasos para el mantenimiento, coloque
el compresor en una situación segura antes de consultar con un técnico.
El uso de piezas de repuesto que no sean de Ingersoll Rand puede suponer
en riesgo para la seguridad, disminuir el rendimiento, aumentar la necesidad
de mantenimiento e invalidar todas las garantías.
Para más información, póngase en contacto con la planta de Ingersoll Rand
o el técnico más cercano.
El objetivo de este manual es facilitar directrices para el mantenimiento y la resolución de problemas del compresor.
Para ver documentación de apoyo, consulte la Tabla 1.
Tabla 1: Manuales de producto
Publicación Producto
Número de pieza o documento por región
América EMEA * Pacíco asiático
Manual de información de seguridad del
producto
Todos 80446313 80446156 80446321
Manuales de información del producto Todos 80446339 80446164 80446347
Manual de información de piezas de
producto
R37-45 kW 80448095
R55-75 kW 80446271
R132-160 kW Fase individual 80446057
R90-160 kW Bifásico 80446065
* Europa, Oriente Medio y África
También están disponibles las hojas de especicación del producto y los diseños de referencia.
121714.07.03