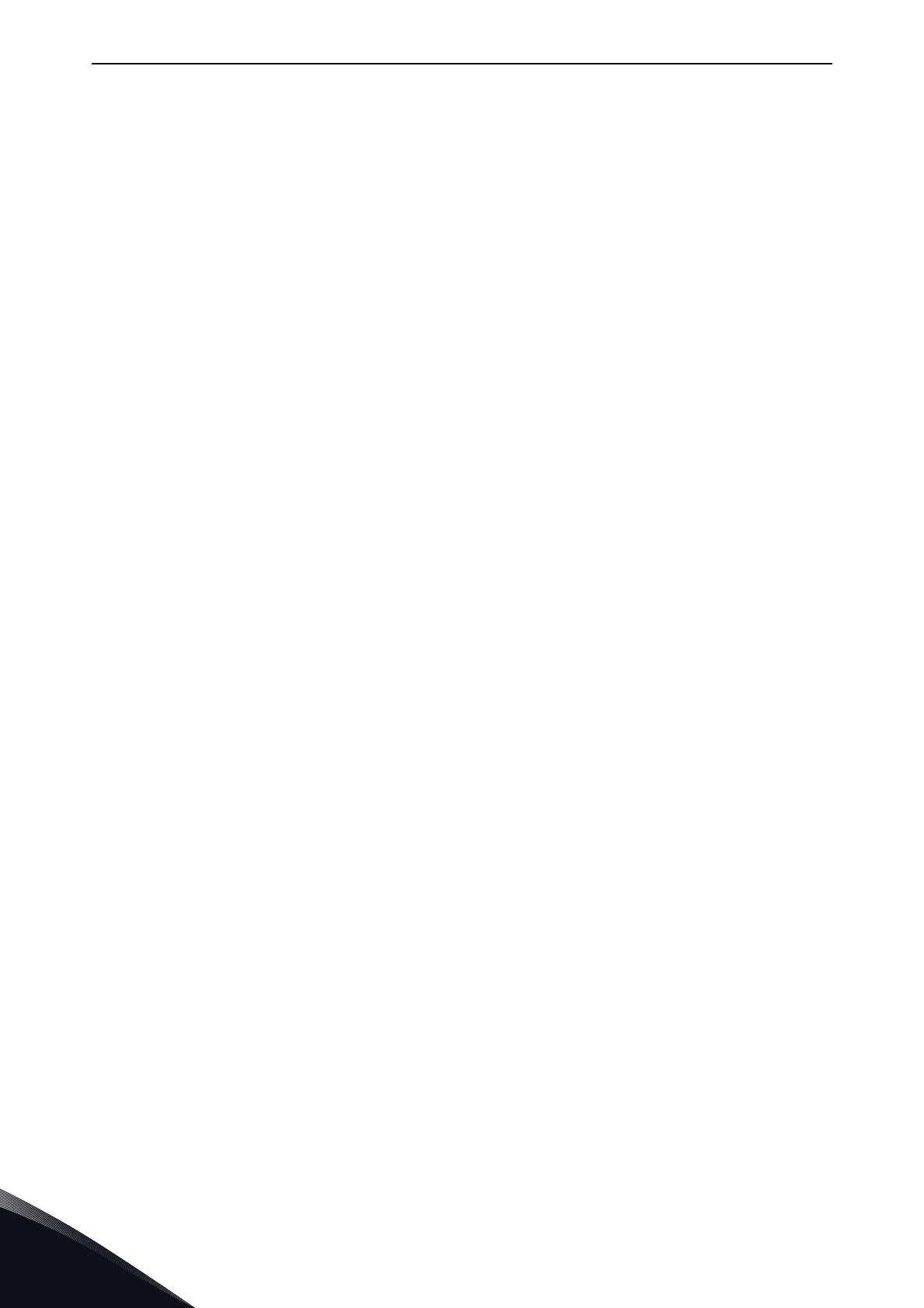
vacon • 2
Local contacts: http://drives.danfoss.com/danfoss-drives/local-contacts/
6.2.3 Control terminal signals ..................................................................................................98
6.2.4 Control unit mounting box .............................................................................................103
6.3 Internal connections ......................................................................................................106
6.3.1 Connections between Power Unit ASIC and Driver Boards ..........................................106
6.3.2 Connections between power unit ASIC and the control unit.........................................109
6.3.3 Connections between mains device and inverter power module .................................113
7. Control keypad.............................................................................................116
7.1 Indications on the Keypad display .................................................................................116
7.1.1 Drive status indications .................................................................................................116
7.1.2 Control place indications ...............................................................................................117
7.1.3 Status LEDs (green – green – red) ................................................................................117
7.1.4 Text lines .......................................................................................................................117
7.2 Keypad push-buttons .....................................................................................................118
7.2.1 Button descriptions........................................................................................................118
7.3 Navigation on the control keypad ..................................................................................119
7.3.1 Monitoring menu (M1)....................................................................................................120
7.3.2 Parameter menu (M2)....................................................................................................122
7.3.3 Keypad control menu (M3).............................................................................................123
7.3.4 Active faults menu (M4) .................................................................................................125
7.3.5 Fault history menu (M5).................................................................................................127
7.3.6 System menu (M6) .........................................................................................................128
7.3.7 Expander board menu (M7)............................................................................................141
7.4 Further keypad functions...............................................................................................142
8. Commissioning ............................................................................................143
8.1 Safety..............................................................................................................................143
8.2 Commissioning of the AC drive......................................................................................144
9. Fault tracing.................................................................................................146
9.1 Fault codes.....................................................................................................................146
9.2 Load test with motor ......................................................................................................152
9.3 DC link test (without motor)...........................................................................................153
10. Active front end (NXA).................................................................................. 154
10.1 Introduction....................................................................................................................154
10.2 Diagrams ........................................................................................................................154
10.2.1 Active Front End Unit block diagram.............................................................................154
10.3 Type designation code....................................................................................................155
10.4 Active Front End unit technical data..............................................................................156
10.5 Power ratings.................................................................................................................160
10.6 Liquid-Cooled RLC filters ..............................................................................................162
10.6.1 Introduction....................................................................................................................162
10.6.2 Wiring diagrams.............................................................................................................162
10.6.3 Power rating and dimensions........................................................................................163
10.6.4 Technical data ................................................................................................................165
10.6.5 Removing discharging resistors....................................................................................165
10.6.6 Removing HF capacitors ................................................................................................166
10.7 Active front end - fuse selection....................................................................................168
10.7.1 Fuse sizes, Active Front End units (AC supply) .............................................................168
10.8 Pre-Charcing circuit ......................................................................................................170
10.9 Parelling.........................................................................................................................172
10.10 Common pre-charging circuit .......................................................................................173
10.11 Each Active Front End unit has the pre-charcing circuit ..............................................174
11. Non-regenerative front end.........................................................................175
11.1 Introduction....................................................................................................................175
11.2 Diagrams ........................................................................................................................175