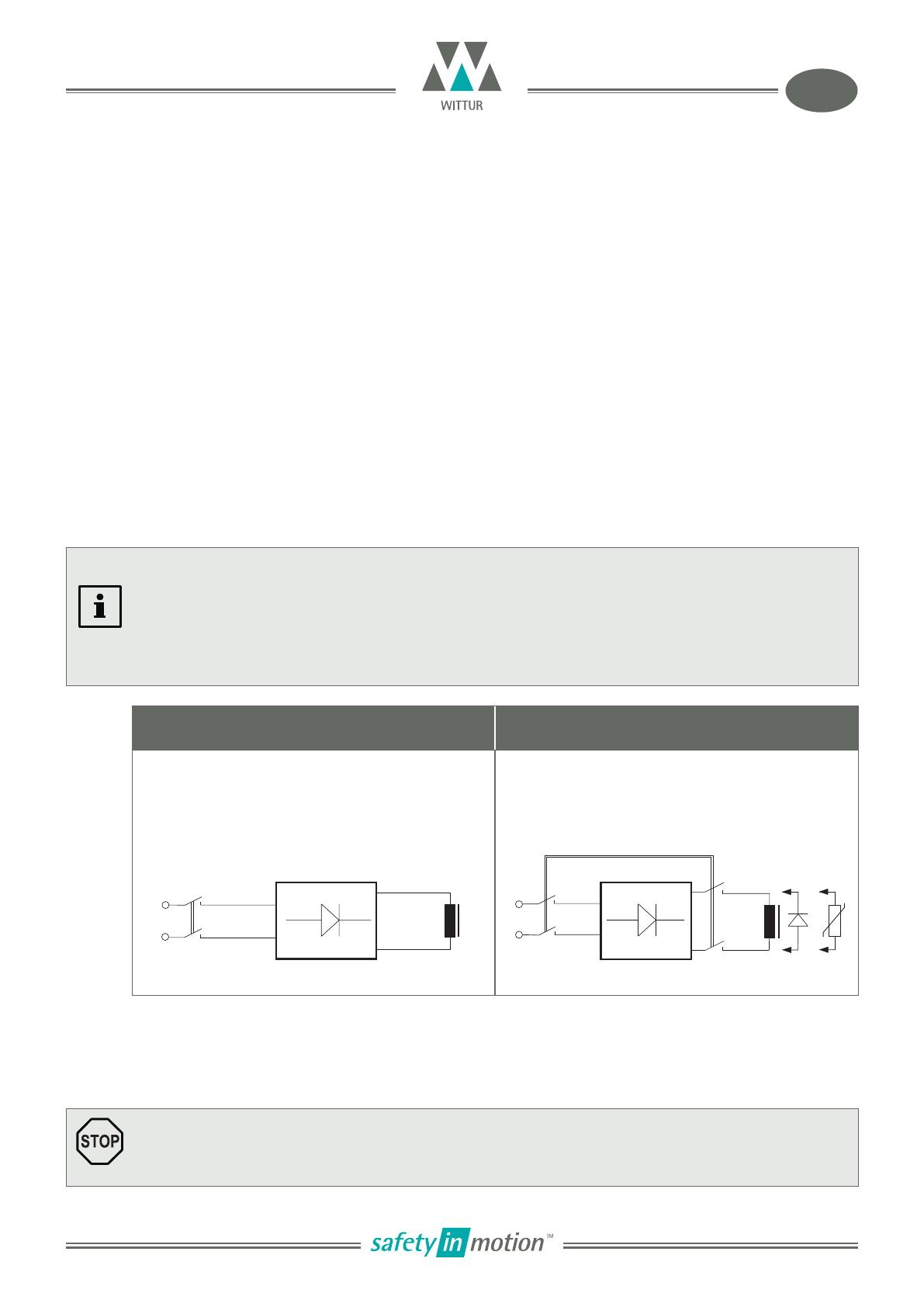
Subject to changes without notice ! Änderungen vorbehalten !
Gearless Lift Machine
WSG-SF
Operating Instructions
EN
Code: GM.8.004284.EN
Date: 28. Jan 2020
Version: 0.16
Page: 12
5.3.4. Brake
•Please refer also to the operating instructions for the brake on pages 62.
•The brakes are supplied with DC voltage by the overexcitation rectiers, which are supplied separately or in the
terminal box.
•Only the brake control units which are included in our scope of supply are to be used for the brake activation.
•Repeated switching of the brake magnets during the overexcitation period must be avoided as this will result in
overloading of the brake control unit. Therefore, a minimum brake operating time of approx. 1.5 – 2 s should be
maintained, especially during an inspection or commissioning drive.
•To reduce the switch-off time, switching can be effected from the DC side. However, switching must also be performed
from the AC side at the same time ! (Wiring with a varistor as shown in the „Circuitry suggestion for brake control“ on
page 14.)
•The brakes must be protected with varistors against overvoltage from switching operations. The varistor must be
directly connected to the coil.
Note on the use of DC/AC side switching
fAC side switching is recommended for normal operation, since the lift machine is then decelerated in a controlled
manner to zero speed and the switching noise of the brake is negligible.
fWhen braking in the event of a breakdown (emergency stop) or during an inspection drive, the switching should
be performed from the DC side, since this ensures a faster braking effect with the car being stopped earlier. We
therefore recommend the use of 2 separate contactors for the brake control circuitry, one of which switches at the
DC side, the other at the AC side.
AC side switching DC side switching
fLow-noise switching of the brake
fNo protective measures required for switching
contact
fSlow application of the brake.
fNoisy switching
fBurn-up protection for switching contact required (e.g.
varistor, free-wheeling diode)
fFast application of the brake.
~
+
Br ~
+
-
Br
Attention: Schematic diagram! Attention: Schematic diagram!
Monitoring the brakes
•The switching states of the brakes are monitored by means of dust-proof microswitches. In the standard version the
n.c. contact is available. In the version with a terminal box both the n.c. and the n.o. contact connections are available.
•Please assure that the contact-current is at least 10 mA to keep the contacts clean.
fThe micro-switches must be evaluated separately for each partial brake to ensure compliance with the
requirements of the type examination.