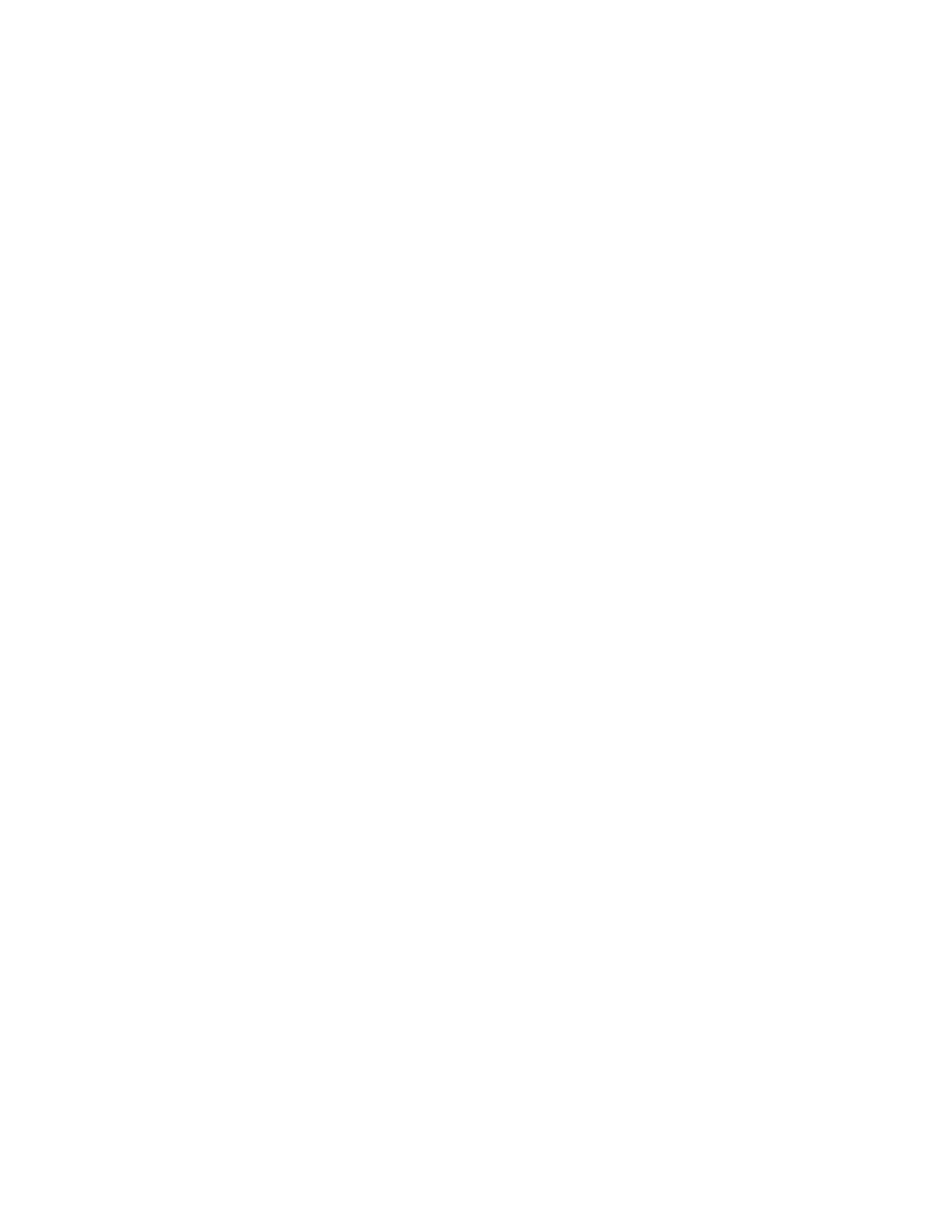
Contents
1 About This Document .....................................................................................................
4
1.1 Important . . . Read This Before Proceeding! .................................................................................4
1.1.1 Use of Warnings and Cautions ...........................................................................................4
1.1.2 EC Declaration of Conformity (DoC) .................................................................................. 4
2 Introduction .................................................................................................................. 5
2.1 Features ................................................................................................................................. 5
2.2 System Description .................................................................................................................. 5
2.3 Appropriate Applications and Limitations ..................................................................................... 6
2.3.1 Examples: Appropriate Applications .................................................................................. 7
2.3.2 Examples: Inappropriate Applications ................................................................................7
2.4 Control Reliability and Safety Categories ...................................................................................... 7
2.5 Operating Features ....................................................................................................................8
2.5.1 Trip/Latch Output ...........................................................................................................8
2.5.2 Wiring Options for Emitter/Receiver Swapability ................................................................. 9
2.5.3 Manual Reset/Remote Test Input and EDM .........................................................................9
2.5.4 Status Indicators ............................................................................................................9
3 Mechanical Installation .................................................................................................11
3.1 Mechanical Installation Considerations .......................................................................................11
3.1.1 Calculating the Safety Distance (Minimum Distance) ...........................................................11
3.1.2 Reducing or Eliminating Pass-Through Hazards .................................................................14
3.1.3 Supplemental Safeguarding ............................................................................................15
3.1.4 Other Considerations ......................................................................................................15
3.2 Mounting System Components ..................................................................................................20
3.2.1 Overview of Emitter/Receiver Mounting Hardware ..............................................................20
3.2.2 Mounting and Initial Alignment of Emitter/Receiver Pairs .....................................................21
4 Electrical Installation and Testing ................................................................................ 23
4.1 Routing Cordsets .....................................................................................................................23
4.2 Initial Electrical Connections .................................................................................................... 23
4.3 Initial Checkout Procedure ........................................................................................................25
4.3.1 Configuring the System for Initial Checkout ......................................................................25
4.3.2 Initial Power-Up ............................................................................................................26
4.3.3 Optical Alignment ......................................................................................................... 26
4.3.4 Optical Alignment Procedure with Mirrors .........................................................................28
4.3.5 Trip Test ......................................................................................................................28
4.4 Electrical Connections to the Guarded Machine ...........................................................................29
4.4.1 OSSD Output Connections ............................................................................................. 30
4.4.2 FSD Interfacing Connections .......................................................................................... 30
4.4.3 Machine Primary Control Elements and EDM Input ..............................................................31
4.4.4 Manual Reset/Remote Test Input and EDM .......................................................................31
4.4.5 Preparing for System Operation ......................................................................................33
4.4.6 Commissioning Checkout ...............................................................................................33
4.5 Reference Wiring Diagrams .......................................................................................................34
4.5.1 Generic Emitter Wiring Diagram ......................................................................................34
4.5.2 Generic Wiring to FSDs (manual reset) ............................................................................ 35
4.5.3 Generic Wiring — Interface Module (2-Channel EDM, Manual Reset) .................................... 36
5 System Operation ........................................................................................................ 37
5.1 Security Protocol ....................................................................................................................37
5.2 Reset Procedures ................................................................................................................... 37
5.2.1 Receiver Resets ............................................................................................................37
5.2.2 Emitter Resets ..............................................................................................................37
5.3 Status Indicators ....................................................................................................................37
5.3.1 Receiver ......................................................................................................................38
5.3.2 Emitter ........................................................................................................................38
5.4 Normal Operation ...................................................................................................................39
5.4.1 System Power-Up .........................................................................................................39
5.4.2 Run Mode ....................................................................................................................39
5.4.3 Manual Reset Procedure ................................................................................................ 39
5.5 Periodic Checkout Requirements ...............................................................................................39
6 Troubleshooting and Maintenance ............................................................................... 40
6.1 Troubleshooting and Lockout Conditions ....................................................................................40
6.2 Recovery Procedures .............................................................................................................. 40
6.2.1 Receiver (System Reset) ................................................................................................40
6.2.2 Emitter Reset ...............................................................................................................40
EZ-SCREEN
®
Type 2 Light Screen
Phone: 800.894.0412 - Fax: 888.723.4773 - Web: www.clrwtr.com - Email:
[email protected]