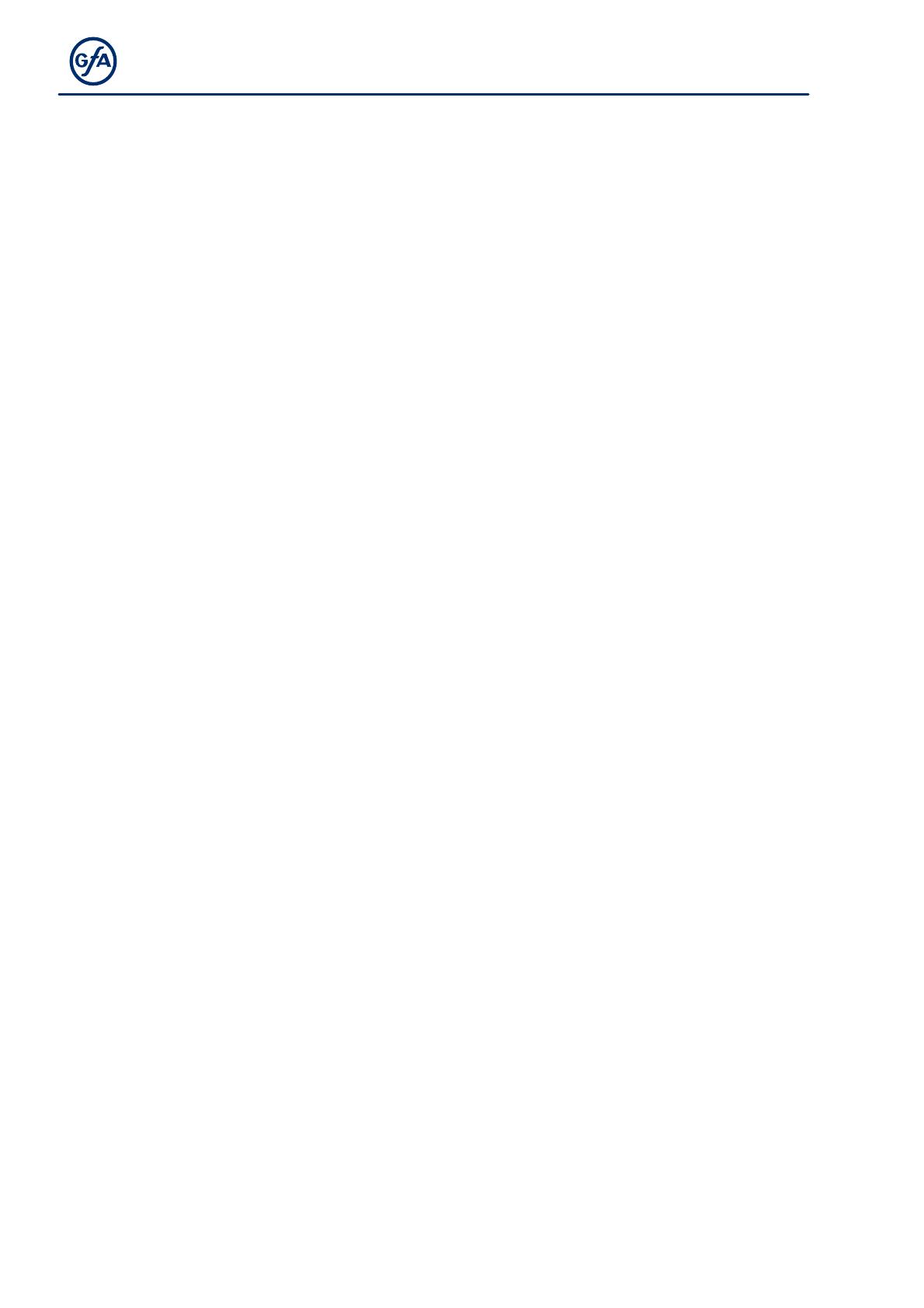
TS 400 basic information
8
TS 400 basic information
The control TS 400 is designed for use with GfA Sliding-door-drives ELEKTROMATEN® with /
without magnetic brake. It has to be installed separately and to be wired with the
ELEKTROMATEN®. The main board contains contactors for open (K1) and close (K2).
Additional modules e.g. for loop detection are available.
The TS 400 is designed for 3-phase motors 3x400 V/N/PE, 3 x 230 V//N/PE or single phase
a.c. motors 1 x 230 V/N/PE with symmetric winding. Correct switching operation of the
contactors is controlled through phase-monitoring of U/V/W while movement and also in
standstill. While programming the control setting for phase-monitoring for single-phase or 3-
phase has to be done. Also it is possible to turn the monitoring off in this menu.
An integrated power supply for 24 V/DC is for internal use and also for supply of external
devices construed. Through this the control is impassibly against voltage fluctuation. All
external commands and safety devices are connected to the 24V/DC control circuit. In case
of overload the power supply turns off and resets after a few seconds.
The travel way is determined through limit switches mounted inside the ELEKTROMATEN®
or separate, at the sliding-door mounted (mechanic or inductive) limit switches. If internal limit
switches in ELEKTROMATEN® are used these might be mechanic (NES) or digital (DES).
For both pluggable cables can be used.
The control is equipped with a 4-row 20-signs LC-Display. This is used for programming,
information about door status and for clear information about fault status. The Encoder (DCS)
and the display enable an easy guided adjustment of the control unit.
Next to the DCS two switches are mounted direct to the mainboard. These are marked with
open (AUF) and close (ZU) and can be used for direct command during the adjustment of the
limits. The switches also can be used in dead man mode, so the control has to be mounted in
full view of the door.
A weekly timer is also integrated in the control unit. The processor works according to the
real-time principle and is buffered by a standard CR2032 battery. Therefore, the internal clock
continues to run for approx. 5 years in case of a power failure. When replacing the battery,
date and time must be re-entered. The programmed times (up to 33 cycles) are saved
permanent. For use of the timer automatic closing has to be activated (Open time > 0).
Up to 6 safety edges with Resistor 8K2 are evaluated. Two moveable and four stationary
safety edges can be connected. There are two possibilities for signal transmission of the
moveable safety edges:
- Wired with system of cable handling
- Inductive transmission – ASO module necessary
Attention: max. length of cable from control unit to stationary coil is 5m!
It is possible to program an intermediate door position „partly-open“ e.g. for passenger use
or for different openings for cars and trucks. With a separate command this position can be
requested. For use with mechanic limit switches an additional opening limit switch has to be
mounted at this position. Before first programming this switch must be installed, otherwise
there will be no possibility for programming in the menu.