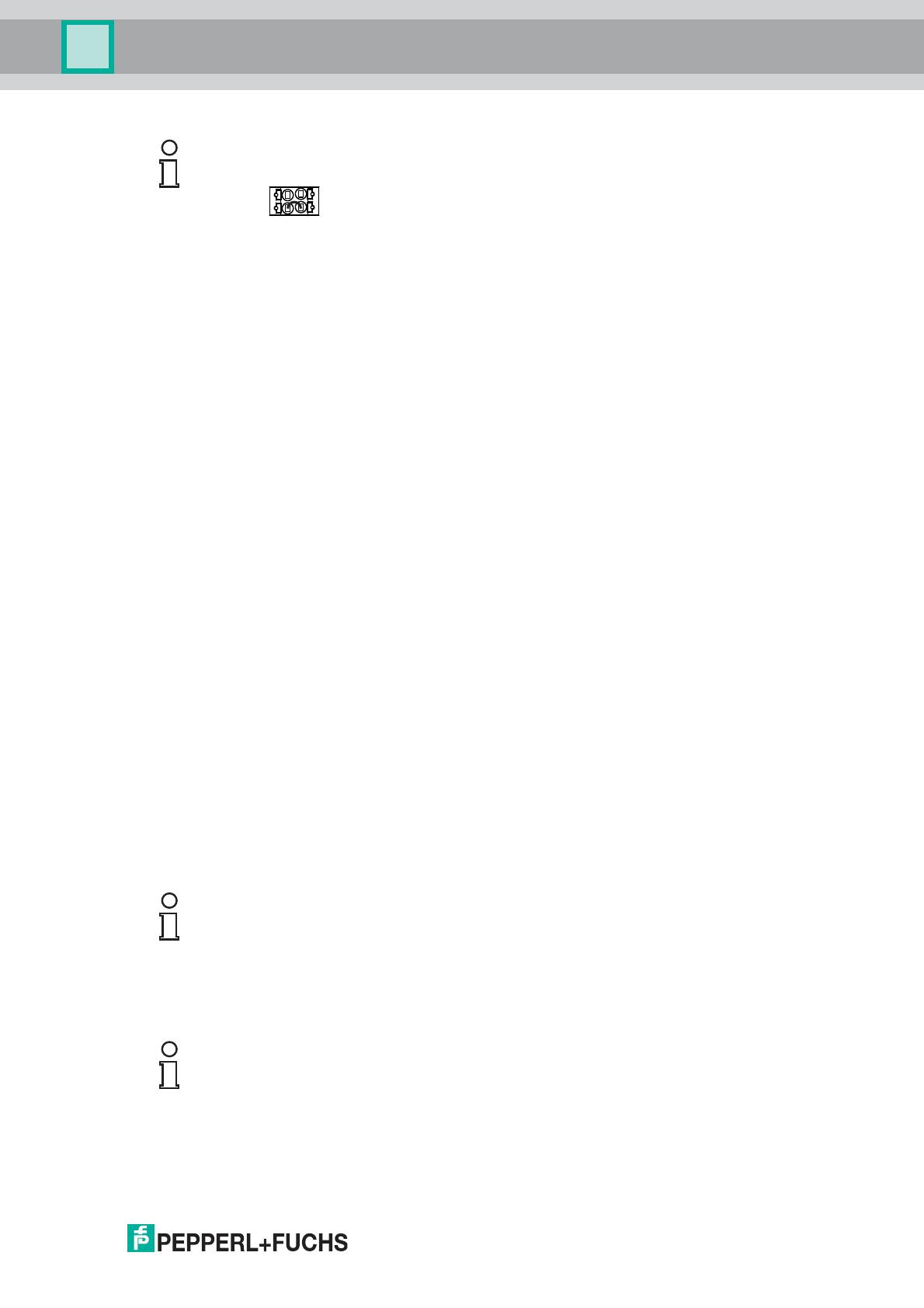
VBA-2E-KE5-IJL/UJL
Product Description
2018-07
9
3.4 Automatic Detection of the Sensor Type
Each of the two input channels can be operated either as a current or a voltage input. The
analog input module automatically detects the type of sensor connected. 0 V 10 V or 0/4
20 mA measurement sensors can be connected as sensor types. The automatic detection
process occurs after the device is switched on. The detected sensor type is saved in the non-
volatile memory and reactivated when the device is switched on again.
The valid signal values that ensure unambiguous detection of the type of sensor connected
are:
■
Voltage: 1 ... 11.5 V
■
Current: 1 ... 23 mA
If the module cannot clearly establish which sensor type is connected, the last detected sensor
type is provisionally activated. For example, the module may not detect which sensor type is
connected if the signal values are not within the specified thresholds or if two different sensor
types are simultaneously applied to one channel.
A specific sensor type is finally activated when the signal values measured are within the
specified thresholds.
3.5 Resetting the Automatically Detected Sensor Types
Any sensor types saved through automatic detection are reset when the input configuration of
the module is manually changed. For this, there are two available options:
1. Switch off the module power supply. Place or remove the jumper between 1CH and GND,
then switch on the supply voltage again.
2. Change the status of parameter P1 or P3 (see chapter 5.3). In this case, it is not necessary
to switch the supply voltage off and on.
Repeat this process if necessary to return to the required input configuration.
Note!
Switching Off the Second Channel
Figure 3.3 Jumper for switching off input channel 2
Input channel 2 can be deactivated using a jumper between the GND and 1CH connections or
using parameter P1. The jumper has priority. If no jumper is set and P1 = 1, then both channels
are active.
Note!
Any change made to the input configuration via a jumper between 1CH and GND is only
detected once the supply voltage is switched on. Changes made via parameter P1 and P3 can
also be implemented during ongoing operation. See chapter 5.3.
Do not connect the 1CH and GND connections to external potentials. The length of the
jumpers must not exceed 5 cm.
Note!
If you connect two different sensor types to one channel simultaneously, fault-free operation is
not guaranteed. The module will not be damaged by this.