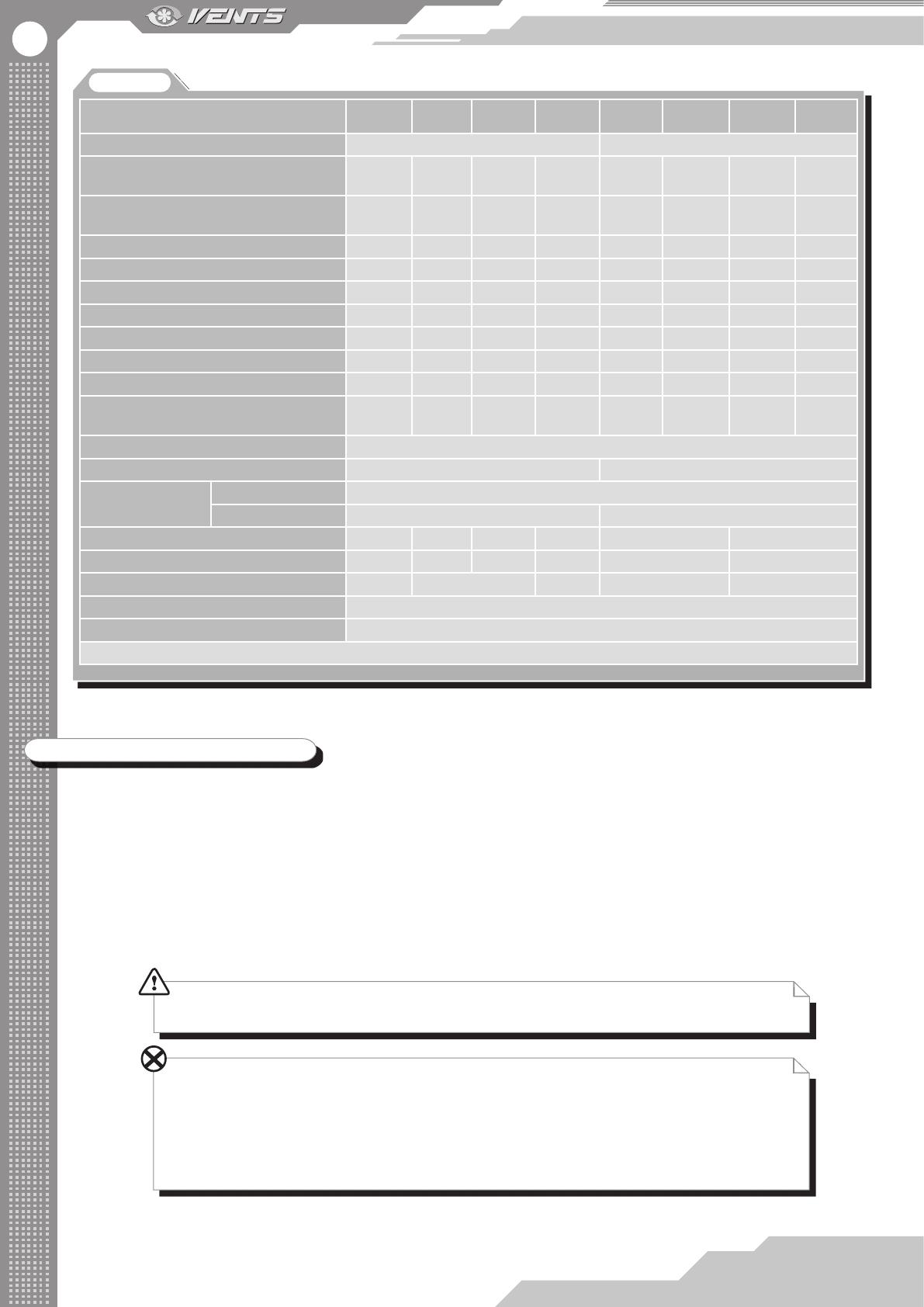
6
Table 3
Type
VUT 350
EH
VUT
500 EH
VUT 530
EH
VUT 600
EH
VUT 800
EH
VUT
1000 EH
VUT
1500 EH
VUT
2000 EH
Supply voltage, 50 Hz [V] 1~230 3~400
Max. fan power [W]
2 items х
130
2 items
х 150
2 items
х 150
2 items х
195
2 items
х 245
2 items х
410
2 items х
490
2 items
х 650
Max. fan current [A]
2 items х
0,60
2 items
х 0,66
2 items
х 0,66
2 items х
0,86
2 items
х 1,08
2 items х
1,8
2 items х
2,15
2 items
х 2,84
Electric heater power [kW] 3,0 3,0 4,0 4,0 9,0 9,0 18,0 18,0
Electric heater current [A] 13 13 17,4 17,4 13 13 26 26
Total unit power [kW] 3,26 3,3 4,3 4,39 9,49 9,8 18,98 19,30
Total unit current [A] 14,2 14,32 18,72 19,1 15,16 16,6 30,3 31,7
Max. air capacity, m
3
/h 350 500 530 600 800 1200 1750 2200
Rotation speed [min
-1
] 1150 1100 1100 1350 1650 1850 1100 1150
Noise level, 3 m [dB(A)] 24-45 28-47 28-47 32-48 48 60 49 65
Transported air temperature [°C]
-25 up to
+55
-25 up
to +50
-25 up
to +50
-25 up
to +55
-25 up
to +45
-25 up to
+40
-25 up to
+45
-25 up
to +40
Casing material aluzinc
Insulation 25 mm mineral wool 50 mm mineral wool
Filter:
extract G4
supply F7 G4 (F7)*
Connected air duct diameter [mm] Ø 125 Ø 150 Ø 160 Ø 200 Ø 250 Ø 315
Weight [kg] 45 49 49 54 85 96
Heat recovery eciency [%] up to 78 up to 88 up to 85 up to 78 up to 77
Heat exchanger type cross ow
Heat exchanger material aluminium
*option
SAFETY REQUIREMENTS
DO NOT!
• DO NOT OPERATE THE UNIT BEYOND THE SPECIFIED TEMPERATURE RANGE OR IN AN
AGGRESSIVE AND EXPLOSIVE MEDIUM!
• DO NOT CONNECT CLOTHES DRYERS OR SIMILAR EQUIPMENT TO THE VENTILATION SYSTEM!
• DO NOT OPERATE THE UNIT IN THE AIR AND DUST MIXTURE MEDIUM!
DISCONNECT THE UNIT FROM POWER SUPPLY PRIOR TO MOUNTING, MAINTENANCE,
CONNECTION AND REPAIR WORKS!
While operating and mounting the unit consider the requirements of the present operation manual as well as general requirements
of all applicable local and national building and electrical codes and standards.
The unit must be grounded!
Before connecting the unit to power mains make sure that the unit is free of any visible damages or any other foreign objects inside
the casing that can damage the impeller blades.
Mounting and connection of the unit to power mains only by duly qualied electricians with valid electric work permit!
The unit is not rated for operation in an environment that contains toxic or aggressive substances as acids, alkalis, organic solvents,
soot, paint as well as sputtered particles of explosive or aggressive substances. The unit is not rated for use in areas where atmospheric
conditions are determined by sea climate or hot springs.