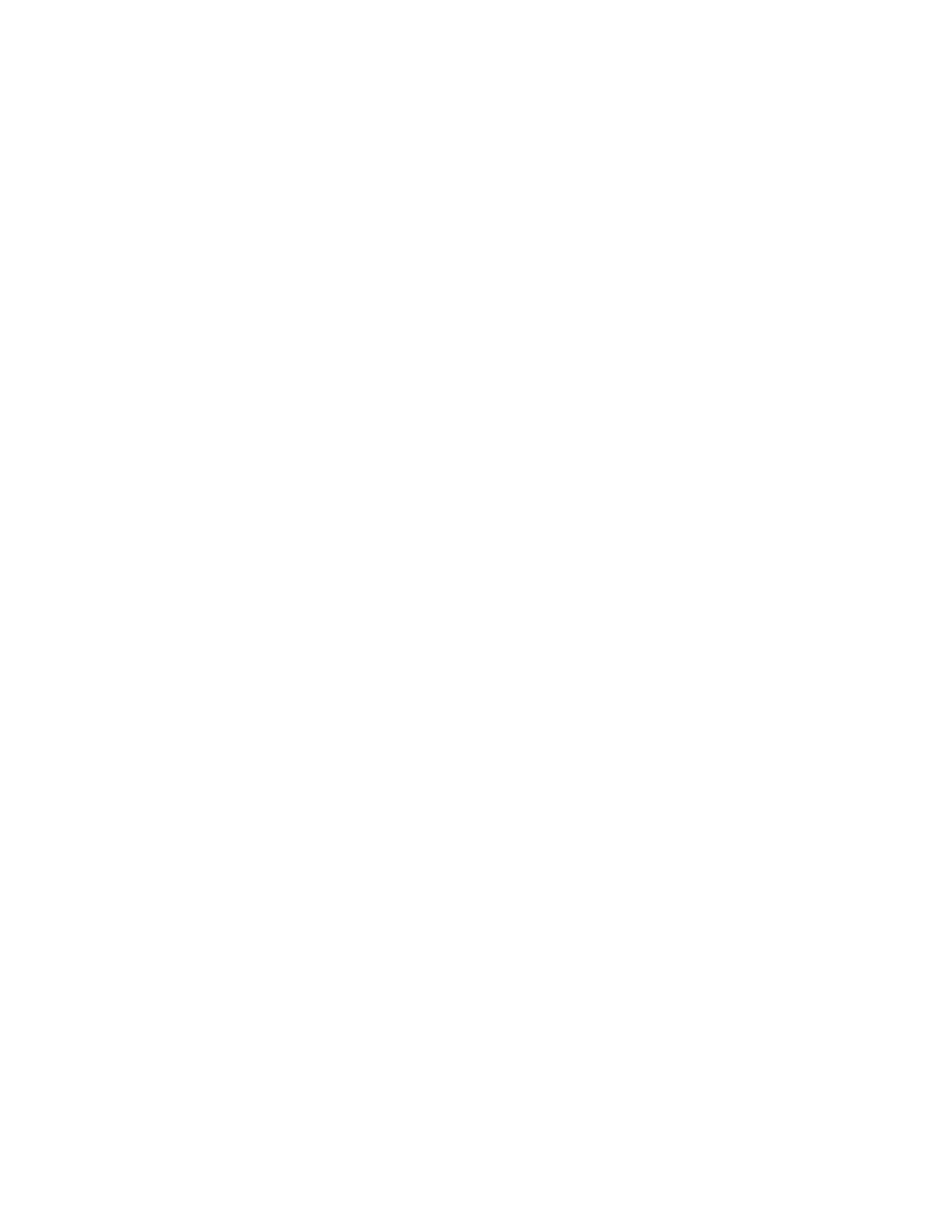
Contents
2 3A2894F
Contents
Contents . . . . . . . . . . . . . . . . . . . . . . . . . . . . . . . . . . 2
Related Manuals . . . . . . . . . . . . . . . . . . . . . . . . . . . 3
Models . . . . . . . . . . . . . . . . . . . . . . . . . . . . . . . . . . . 4
Base Machines . . . . . . . . . . . . . . . . . . . . . . . . . . 4
Hose Kits . . . . . . . . . . . . . . . . . . . . . . . . . . . . . . . 5
Dispense Valves . . . . . . . . . . . . . . . . . . . . . . . . . 5
Warnings . . . . . . . . . . . . . . . . . . . . . . . . . . . . . . . . . 6
Important Isocyanate (ISO) Information . . . . . . . . 8
Isocyanate Conditions . . . . . . . . . . . . . . . . . . . . 8
Material Self-ignition . . . . . . . . . . . . . . . . . . . . . . 8
Keep Components A and B Separate . . . . . . . . . 8
Moisture Sensitivity of Isocyanates . . . . . . . . . . . 9
Changing Materials . . . . . . . . . . . . . . . . . . . . . . . 9
Component Identification . . . . . . . . . . . . . . . . . . . 10
S100 Models . . . . . . . . . . . . . . . . . . . . . . . . . . . 10
U100 Models . . . . . . . . . . . . . . . . . . . . . . . . . . . 11
P100 Models . . . . . . . . . . . . . . . . . . . . . . . . . . . 12
Display Module (DM) . . . . . . . . . . . . . . . . . . . . . 14
User Interface . . . . . . . . . . . . . . . . . . . . . . . . . . 14
Electrical Enclosure . . . . . . . . . . . . . . . . . . . . . 17
Integrated Air Controls . . . . . . . . . . . . . . . . . . . 18
Fluid Control Module (FCM) . . . . . . . . . . . . . . . 20
Installation . . . . . . . . . . . . . . . . . . . . . . . . . . . . . . . 22
Grounding . . . . . . . . . . . . . . . . . . . . . . . . . . . . . 32
Setup . . . . . . . . . . . . . . . . . . . . . . . . . . . . . . . . . . . . 33
Startup . . . . . . . . . . . . . . . . . . . . . . . . . . . . . . . . . . 42
Base Purge . . . . . . . . . . . . . . . . . . . . . . . . . . . . . . . 44
Pressure Relief Procedure . . . . . . . . . . . . . . . . . . 46
Shutdown . . . . . . . . . . . . . . . . . . . . . . . . . . . . . . . . 48
Calibration Check . . . . . . . . . . . . . . . . . . . . . . . . . 49
Maintenance . . . . . . . . . . . . . . . . . . . . . . . . . . . . . . 52
Adjust Packing Nuts . . . . . . . . . . . . . . . . . . . . . 52
Filters . . . . . . . . . . . . . . . . . . . . . . . . . . . . . . . . 52
Seals . . . . . . . . . . . . . . . . . . . . . . . . . . . . . . . . . 52
DM - Battery Replacement and Screen Cleaning 53
Software Update Procedure . . . . . . . . . . . . . . . 54
Troubleshooting . . . . . . . . . . . . . . . . . . . . . . . . . . . 55
Mechanical and Electrical . . . . . . . . . . . . . . . . . 55
Display Module . . . . . . . . . . . . . . . . . . . . . . . . . 58
Accessories and Kits . . . . . . . . . . . . . . . . . . . . . . . 60
Light Tower 24R824 . . . . . . . . . . . . . . . . . . . . . . 60
Low Level Sensors, 24R935
(S100 and P100 only) . . . . . . . . . . . . . . . . . 60
USB Kit, 24R936 . . . . . . . . . . . . . . . . . . . . . . . . 61
MD2 Nose Pieces . . . . . . . . . . . . . . . . . . . . . . . 61
Catalyst (B) Hoses . . . . . . . . . . . . . . . . . . . . . . . 61
Restrictor Kit, 24R804 . . . . . . . . . . . . . . . . . . . . 61
Caster Kit, 24T091 . . . . . . . . . . . . . . . . . . . . . . . 62
Mixer Elements for MD2 . . . . . . . . . . . . . . . . . . 62
Appendix A - DM Icons Overview . . . . . . . . . . . . . 64
Setup Screen Icons . . . . . . . . . . . . . . . . . . . . . . 64
Run Screen Icons . . . . . . . . . . . . . . . . . . . . . . . 65
Appendix B - DM Setup Screens Overview . . . . . 66
Appendix C - DM Run Screens Overview . . . . . . 68
Appendix D - DM Error Codes . . . . . . . . . . . . . . . 70
Schematics . . . . . . . . . . . . . . . . . . . . . . . . . . . . . . . 72
Dimensions . . . . . . . . . . . . . . . . . . . . . . . . . . . . . . . 76
Technical Data . . . . . . . . . . . . . . . . . . . . . . . . . . . . 77
Graco Standard Warranty . . . . . . . . . . . . . . . . . . . 78
Graco Information . . . . . . . . . . . . . . . . . . . . . . . . . 78