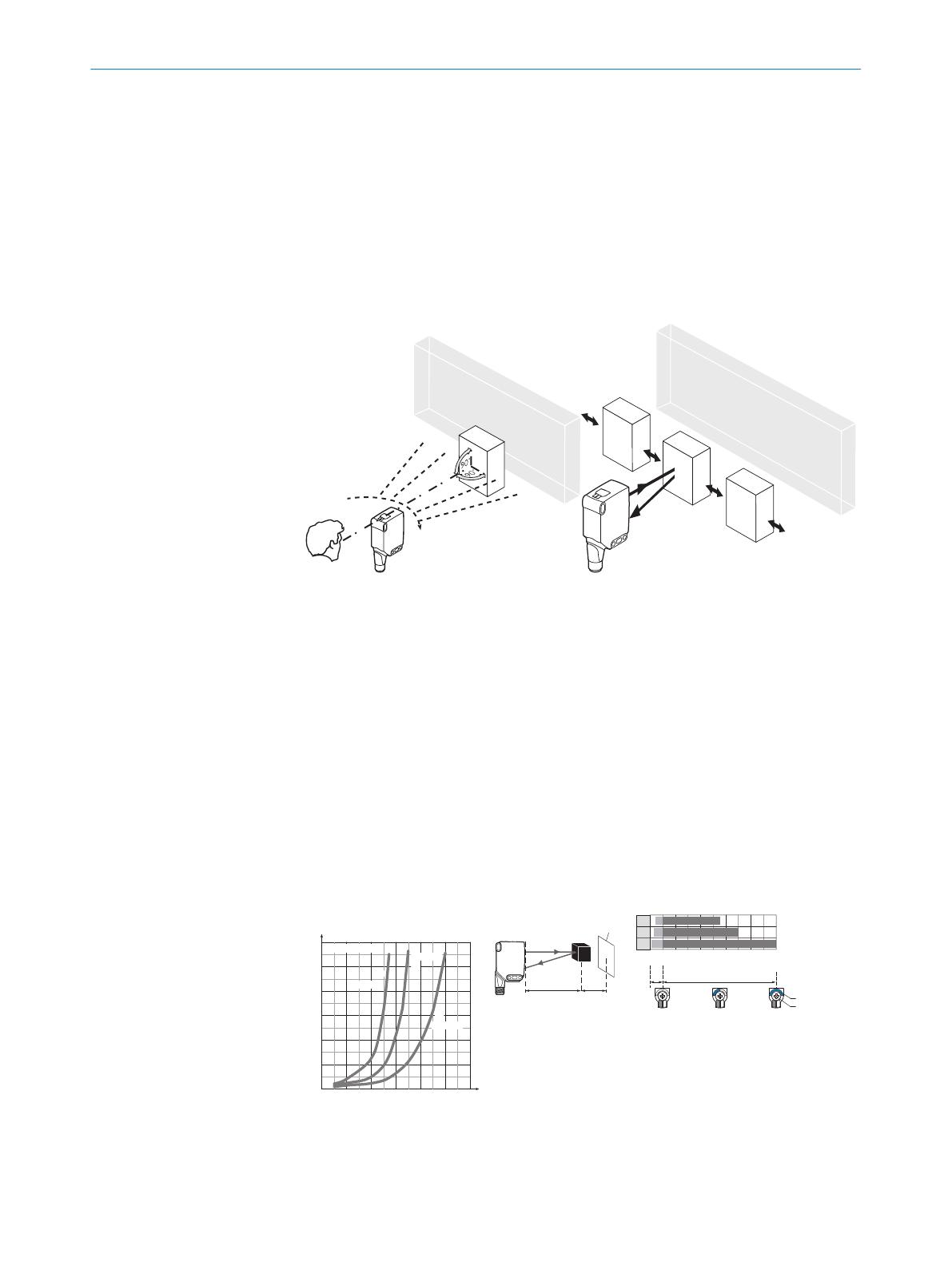
7 Commissioning
1 Alignment
WTB16P: Align sensor on object. Select the position so that the red emitted light beam hits
the center of the object. You must ensure that the optical opening (front screen) of the sen‐
sor is completely clear [see figure 1, see figure 2].
WTB16I: Align the sensor with the object. Select the position so that the infrared light (not
visible) hits the center of the object. The correct alignment can only be detected via the
LED indicators. see figure 1, figure 2, table 2, table 3 and table 4. You must ensure that
the optical opening (front screen) of the sensor is completely clear.
Figure 1: Alignment 1 Figure 2: Alignment 2
2 Sensing range
WTBXX are photoelectric proximity sensors with background suppression. Depending on
the remission of the object to be detected, and perhaps the background behind it, a mini‐
mum distance (y) between the set sensing range (x) and the background is to be main‐
tained.
Check the application conditions: Adjust the sensing range and distance to the object or
background as well as the remission capability of the object according to the correspond‐
ing diagram [see figures 5 and 7] (x = sensing range, y = minimum distance between set
sensing range and background [white, 90%]) Remission: 6% = black 1, 18% = gray 2,
90% = white 3 (referring to standard white as per DIN 5033). We recommend that the
adjustment be performed with an object of low remission.
The minimum distance (= y) for the background suppression can be determined from the
diagram [figure 3 1] as follows:
Example: x = 400 mm, y = 25 mm. That is, the background (white, 90%) is suppressed at a
distance of > 25 mm from the sensor.
0
20
40
60
100
80
120
200
(7.87)
400
(15.75)
600
(23.62)
800
(31.5)
1,200
(47.24)
1,000
(39.37)
0
1
2
3
WTB16P-xxxxx1xx
6%/90%
18%/90%
90%/90%
y
x
yx
Minimum distance in mm (y) between the set sensing
range and background (white, 90%)
white background (90%)
Example:
Sensing range on black, 6%,
x = 400 mm, y = 25 mm
Distance in mm (inch)
Figure 3: Characteristic line 1, WTB16P-xxxxx1xx, red
light
200
(7.87)
100
(3.94)
400
(15.75)
Adjustment range
Distance in mm (inch)
A
600
(23.62)
800
(31.5)
1,000
(39.37)
0
1
2
3
50
/
100
550
25 700
10 1,000
BluePilot:
Sensing range
indicator (blue LED)
Teach-Turn
adjustment
A = Detection distance (depending on object remission)
100
100
7 COMMISSIONING
8
8020346.14CS | SICK
Subject to change without notice