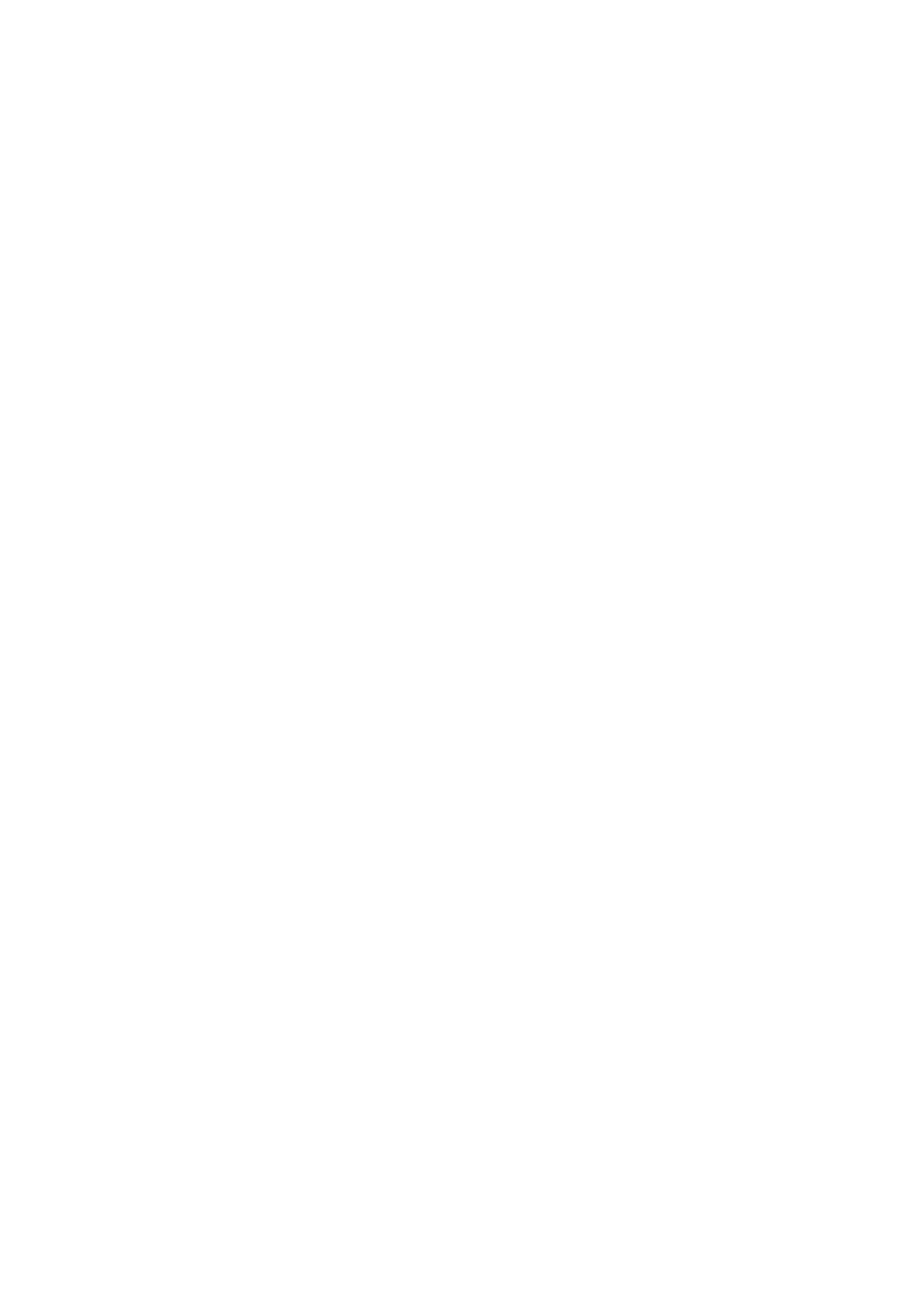
(2/n)
LEN080334E
CONTENTS
1. General Description ......................................................................................................................................... 3
2. Specification ..................................................................................................................................................... 4
3. Configuration Conditions of CC-Link System................................................................................................... 5
3.1 Remote net ver.1 mode ............................................................................................................................ 5
3.2 Remote net ver.2 mode ............................................................................................................................ 6
4. Programming .................................................................................................................................................... 8
4.1 Programming Procedure .......................................................................................................................... 8
5. Parameter Settings .......................................................................................................................................... 9
5.1 Procedure from Parameter Settings to Data Link Startup ........................................................................ 9
5.1.1 CPU Parameter Area and Master Module Parameter Memory .................................................... 9
5.1.2 Procedure for Parameter Settings to Data Link Startup with GX Developer ................................ 9
5.2 Example of Parameter Settings with GX Developer .............................................................................. 10
5.2.1 Master Station Network Parameter Settings ............................................................................... 10
6. Communication Between the Master Station and ME96 ............................................................................... 14
6.1 Communication Guideline ...................................................................................................................... 14
6.2 Initial Communication ............................................................................................................................. 15
6.3 Error Communication .............................................................................................................................. 15
6.4 Normal Communication .......................................................................................................................... 16
7. Remote I/O and Remote Register .................................................................................................................. 17
7.1 Remote Input RX, Remote Output RY ................................................................................................... 17
7.1.1 Remote input RX ......................................................................................................................... 17
7.1.2 Remote Output RY ...................................................................................................................... 19
7.2 Remote Register (RWr, RWw) ................................................................................................................ 21
7.2.1 Supported Commands ................................................................................................................ 24
7.2.2 Details of Commands .................................................................................................................. 25
7.2.3 Data format ................................................................................................................................. 42
7.2.4 Multiplying Factor ........................................................................................................................ 53
7.2.5 About Error Occurrence .............................................................................................................. 54
8. Abbreviations and Special Terms ................................................................................................................... 55
9. Program Example .......................................................................................................................................... 56
9.1 Program Example 1 ................................................................................................................................ 56
9.1.1 Program Content ......................................................................................................................... 56
9.1.2 Parameter Settings ..................................................................................................................... 57
9.1.3 Program example ........................................................................................................................ 61
9.2 Program Example 2 ................................................................................................................................ 69
9.2.1 Program Content ......................................................................................................................... 69
9.2.2 Parameter Settings ..................................................................................................................... 70
9.2.3 Device Allocation ......................................................................................................................... 73
9.2.4 Program Example ....................................................................................................................... 74
10. Test Mode ....................................................................................................................................................... 85
10.1 ME96SSH/SSR/SSHA/SSRA/SSHB/SSRB-MB .................................................................................... 85
10.2 ME96NSR ............................................................................................................................................... 86