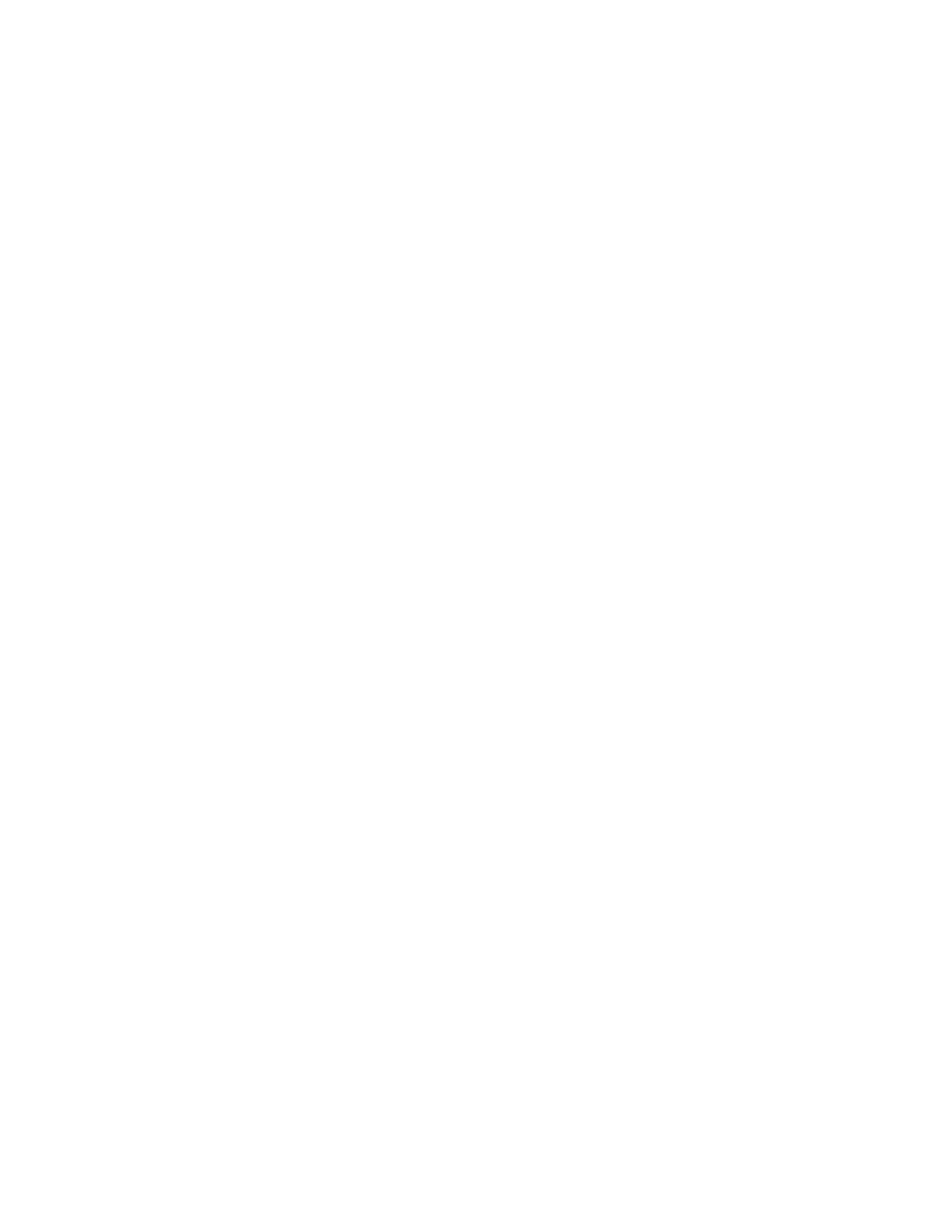
5
C4 Manual Rev 7.5.2
Invalid Loop Count Error ............................. 50
Setpoint Out of Range Error .......................... 50
6.8 Special Commands ........................................ 50
6.8.1 Controlled Program Looping ........................... 51
6.8.2 External Compressor On ............................. 52
6.8.3 External Compressor Off ............................. 52
6.8.4 Optional Aux/Power Control Port On .................... 52
6.8.5 Optional Aux/Power Control Port Off .................... 52
6.9 Common Programming Issues................................ 53
6.9.1 Step Numbering .................................... 53
6.9.2 Changing Substep Values ............................ 53
6.9.3 Control Ports....................................... 53
7. REMOTE MODE................................................. 55
7.1 EIA-232 Interface .......................................... 55
7.2 IEEE-488 Interface ......................................... 55
7.3 Command Summary (by functional group) ....................... 56
7.4 System Information Queries.................................. 57
7.4.1 QV Query Firmware Version........................... 57
7.4.2 QN Query Controller Serial Number..................... 57
7.4.3 QR Query Controller Temperature Range ................ 58
7.4.4 QS Query Setpoint & Control Probe Number .............. 58
7.4.5 QF, QFA Query Setup Parameter Value ................ 59
7.5 Operation Information Queries & Commands .................... 61
7.5.1 RS, RSA Request Status Byte ......................... 61
7.5.2 RE, REA Request Error Byte .......................... 61
7.5.3 QE, QEA Query Error/Status String..................... 62
7.5.4 QC Query Last Command............................ 64
7.5.5 ES Enable SRQ (Status Request Mode) ................. 64
7.5.6 DS Disable the SRQ ................................ 64
7.5.7 PT Read Temperature ............................... 65
7.6 Setup Parameter Commands ................................. 66
7.6.1 SC Set Probe Correction ............................. 66
7.6.2 WP Set PID Constants .............................. 67
7.6.3 BF & BO Blower Off & Blower On Commands ............ 68
7.6.4 SL Set UUT Temperature Limits ....................... 69
7.6.5 SD Set UUT Temperature Differential Limits.............. 69
7.6.6 UP Write Current Parameters to NV Memory ............. 69
7.7 System Operation Commands ................................ 70
7.7.1 SI Select Immediate Mode............................ 70
7.7.2 SP Select Program Mode ............................ 70
7.7.3 PN Select Active (control) Probe ....................... 70
7.7.4 GT, GTF Go To Temperature ......................... 71
7.7.5 RA, RAF Ramp to Temperature ....................... 71
7.7.6 DL Delay (Dwell Interval) ............................. 72
7.7.7 CO & CF Turn the Refrigeration Port On................. 72