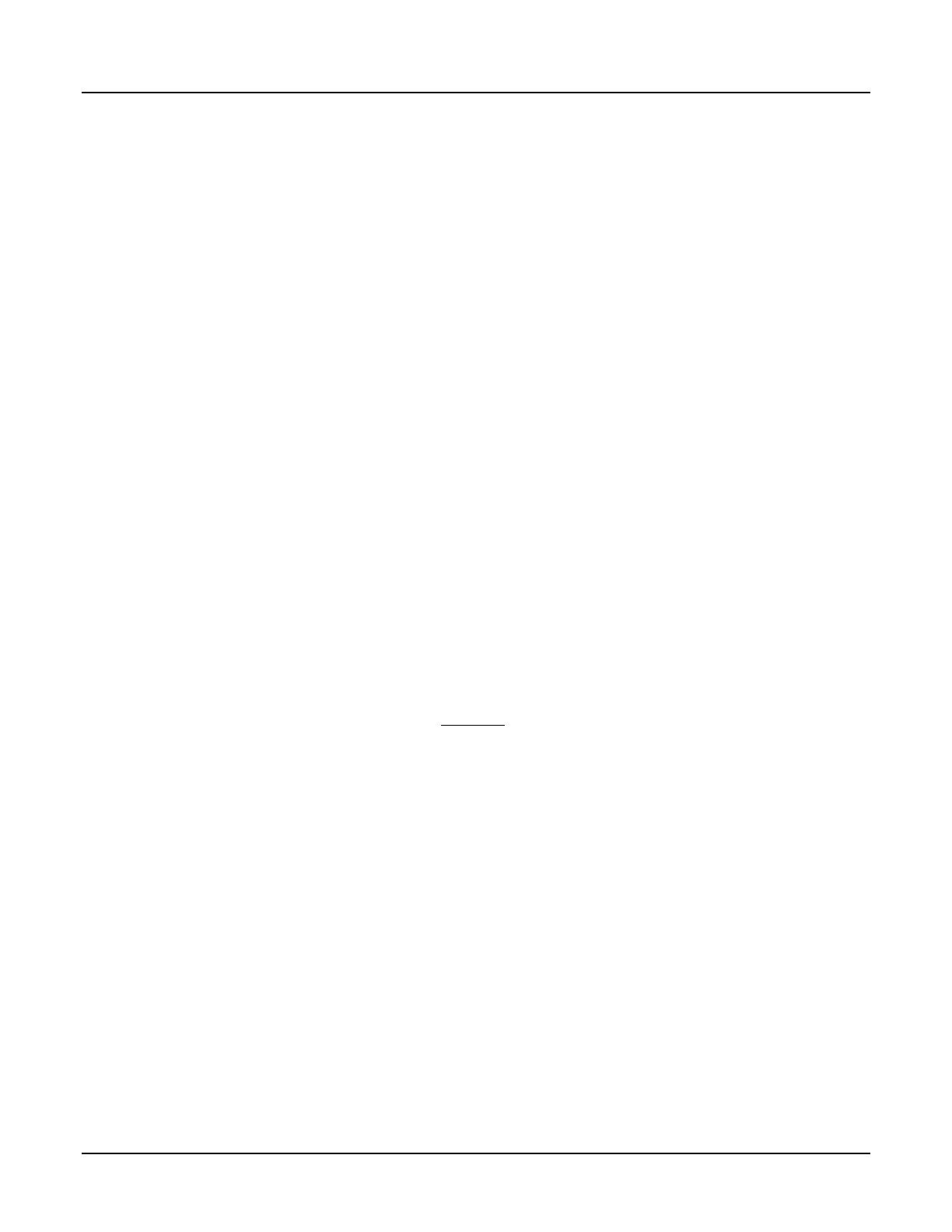
SECTION 2-1
EQUIPMENT DESCRIPTION FLOWMAX RO MANUAL REV: B 05/1999
USFilter United States Filter Corporation
2.0 EQUIPMENT DESCRIPTION
2.1 GENERAL SYSTEM DESCRIPTION
The purpose of this section is to introduce the user to the equipment. A thorough understanding of the
equipment will help when installing, testing, and operating the system. Refer to the drawings supplied
in the Appendix for further clarification.
MAX Membrane Systems are the standard 8” RO product line for USFilter . There are four different
sub groups of MAX RO units, tailored to the specific needs of the pharmaceutical and beverage industry
as well as general industrial and commercial applications. These are described below.
PharmMAX™
The PharmMAX™ RO system is packaged for the pharmaceutical and biotech industries. These units
feature Filmtec RO-390-FF full fit membrane elements, Codeline FRP, 80A side port direct connect,
pressure vessels, Grundfos CRN SST pumps and Allen Bradley PLC based control systems. We have
three standard sizes available, with your choice of either PP or SST sanitary product piping. The feed
piping is PVC, but SST piping is also available. These systems feature Thornton 200 series conductivity
and flow monitors, and the new Fluidyne vortex shedding flow sensors. Another new feature is virtual
product flow display, with flow sensors in the feed and reject lines, and no dirty intrusions into the
product line. The Thornton 200F flow monitor allows you to display the product flow as the difference
of the two measured flows. (For lower flow rates, please see the new Pharm40 Series of pharmaceutical
RO units.) .
FlowMAX™
The FlowMAX™ RO system is packaged for general industrial applications. There are 10 different
sizes that come standard with Filmtec BW30-365 membrane elements, Codeline FRP, 80A side port
direct connect, pressure vessels. There are two standard pump choices, the T&T horizontal booster
pump or the Grundfos BM series submersible pump. The standard control package is a Allen Bradley
MicroLogix PLC control system. (There are standard SCL 5/04 and Remote I/O panels that can be used
if required.) The feed piping and product piping are PVC. Like the PharmMAX™ , the FlowMAX™
systems feature Thornton 200 series conductivity and flow monitors, and the new Fluidyne vortex
shedding flow sensors. The two piece frame design allow you flexibility in layout configurations, for
jobs with limited floor space. Important to note that due to the different feed flow requirements, and
depending on which membrane you select, the cartridge filter housing is not standard and mounted on
the RO frame, so must be sized and ordered separately.
BevMAX™
The BevMAX™ RO system is packaged for the beverage industry or any application that requires all
piping to be SST. They are similar to the FlowMAX, except all piping is mill finish 316L SST. These
units are available with either Filmtec BW30-365 or BW30-440LE membrane elements, and Codeline
FRP, side port, direct connect, pressure vessels. The feed pumps are all SST, T&T horizontal booster
pumps. The standard control package is a AB MicroLogix PLC based control system. Like the other
MAX RO systems, they feature Thornton 200 series conductivity and flow monitors, and the new
Fluidyne vortex shedding flow sensors. Like the FlowMAX™, the cartridge filter housing is not
mounted on the RO frame, and must be ordered separately.